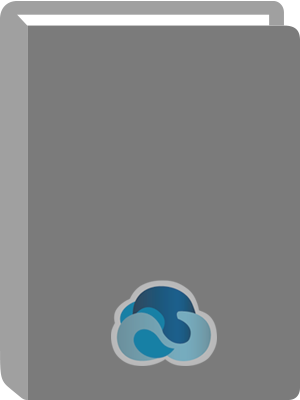
Chemical Engineering Design : Principles, Practice and Economics of Plant and Process Design.
Title:
Chemical Engineering Design : Principles, Practice and Economics of Plant and Process Design.
Author:
Towler, Gavin.
ISBN:
9780080966601
Personal Author:
Edition:
2nd ed.
Physical Description:
1 online resource (1321 pages)
Contents:
Front Cover -- Chemical Engineering Design: Principles, Practice and Economics of Plant and Process Design -- Copyright -- Table of Contents -- Preface to the Second Edition -- How to Use This Book -- Part I: Process Design -- Part II: Plant Design -- Supplementary Material -- Acknowledgments -- Part 1: Process Design -- 1 Introduction to Design -- 1.1 Introduction -- 1.2 Nature of Design -- 1.2.1 The Design Objective (The Need) -- 1.2.2 Setting the Design Basis -- 1.2.3 Generation of Possible Design Concepts -- 1.2.4 Fitness Testing -- 1.2.5 Economic Evaluation, Optimization, and Selection -- 1.2.6 Detailed Design and Equipment Selection -- 1.2.7 Procurement, Construction, and Operation -- 1.3 The Organization of a Chemical Engineering Project -- 1.4 Project Documentation -- 1.4.1 Design Documents -- Calculation Sheets -- Drawings -- Specification Sheets -- Process Manuals -- Operating Manuals -- 1.4.2 Design Reports -- 1.5 Codes and Standards -- 1.6 Design Factors (Design Margins) -- 1.7 Systems of Units -- 1.8 Product Design -- 1.8.1 New Chemical Products -- New Molecules -- New Formulations -- New Materials -- New Equipment and Devices -- 1.8.2 Understanding Customer Needs -- 1.8.3 Developing Product Specifications -- Quality Function Deployment -- 1.8.4 Fitness Testing -- Prototype Testing -- Safety and Efficacy Testing -- References -- Nomenclature -- Problems -- 2 Process Flowsheet Development -- 2.1 Introduction -- 2.2 Flowsheet Presentation -- 2.2.1 Block Diagrams -- 2.2.2 PFD Symbols -- 2.2.3 Presentation of Stream Flow Rates -- 2.2.4 Information to be Included -- Essential Information -- Optional Information -- 2.2.5 Layout -- 2.2.6 Precision of Data -- 2.2.7 Basis of the Calculation -- 2.2.8 Batch Processes -- 2.2.9 Utilities -- 2.2.10 Equipment Identification -- 2.2.11 Flowsheet Drafting Programs.
2.3 The Anatomy of a Chemical Manufacturing Process -- 2.3.1 Components of a Chemical Process -- Stage 1. Raw Material Storage -- Stage 2. Feed Preparation -- Stage 3. Reaction -- Stage 4. Product Separation -- Stage 5. Purification -- Stage 6. Product Storage -- Ancillary Processes -- 2.3.2 Continuous and Batch Processes -- Choice of Continuous versus Batch Production -- 2.3.3 Effect of Reactor Conversion and Yield on Flowsheet Structure -- Conversion -- Selectivity -- Yield -- Effect of Conversion, Selectivity, and Yield on Flowsheet Structure -- Use of Excess Reagent -- Sources of Conversion, Selectivity, and Yield Data -- 2.3.4 Recycles and Purges -- Purge -- Bypass -- 2.4 Selection, Modification, and Improvement of Commercially-Proven Processes -- 2.4.1 Sources of Information on Manufacturing Processes -- Patents -- Consultants -- Vendors -- 2.4.2 Factors Considered in Process Selection -- Freedom to Practice -- Safety and Environmental Performance -- Government and International Restrictions -- Experience and Reliability -- 2.4.3 Modification and Improvement of Established Processes -- Modifications to Improve Process Economics -- Modifications to Improve Plant Safety -- Modifications to Improve Plant Reliability -- Modifications to Improve Environmental Impact -- 2.5 Revamps of Existing Plants -- 2.5.1 Flowsheet Development in Revamp Projects -- 2.5.2 Major Equipment Debottlenecking -- Reactor Debottlenecking -- Separation Column Debottlenecking -- 2.5.3 Revamp of Heat Exchange Networks -- Heat Exchangers -- Heaters and Coolers -- 2.5.4 Revamp of Plant Hydraulics -- Compressors -- Pumps -- Control Valves -- 2.6 Synthesis of Novel Flowsheets -- 2.6.1 Overall Procedure for Flowsheet Synthesis -- Step 1. Initial Economics -- Step 2. Set Yield Targets -- Step 3. Preliminary Economic Assessment -- Step 4. Refine Process Structure.
Step 5. PFD Review -- Step 6. Preliminary Process Hazard Analysis (PHA) -- Step 7. Revise Economic Assessment -- 2.6.2 Economic Analysis in Process Synthesis -- 2.6.3 Use of Targets in Process Synthesis -- 2.6.4 Use of Heuristic Rules in Process Synthesis -- 2.6.5 Role of Optimization in Process Synthesis -- 2.7 PFD Review -- 2.7.1 PFD Review Procedure -- 2.7.2 PFD Review Documentation and Issue Resolution -- 2.8 Overall Procedure for Flowsheet Development -- References -- Nomenclature -- Problems -- 3 Utilities and Energy Efficient Design -- 3.1 Introduction -- 3.2 Utilities -- 3.2.1 Electricity -- 3.2.2 Fired Heat -- 3.2.3 Steam -- 3.2.4 Hot Oil and Heat Transfer Fluids -- 3.2.5 Cooling Water -- 3.2.6 Refrigeration -- 3.2.7 Water -- Demineralized Water -- 3.2.8 Compressed Air -- Cooling Air -- 3.2.9 Nitrogen -- 3.3 Energy Recovery -- 3.3.1 Heat Exchange -- 3.3.2 Waste-heat Boilers -- 3.3.3 High-temperature Reactors -- 3.3.4 High-pressure Process Streams -- Gas Streams -- Liquid Streams -- 3.3.5 Heat Pumps -- 3.4 Waste Stream Combustion -- 3.4.1 Reactor Off-gases -- 3.4.2 Liquid and Solid Wastes -- 3.5 Heat-exchanger Networks -- 3.5.1 Pinch Technology -- Simple Two-stream Problem -- Four-stream Problem -- Thermodynamic Significance of the Pinch -- 3.5.2 The Problem Table Method -- Summary -- 3.5.3 Heat-exchanger Network Design -- Grid Representation -- Network Design for Maximum Energy Recovery -- Network Design Above the Pinch -- Network Design Below the Pinch -- Stream Splitting -- Summary -- 3.5.4 Minimum Number of Exchangers -- 3.5.5 Threshold Problems -- 3.5.6 Determining Utility Consumption -- 3.5.7 Process Integration: Integration of Other Process Operations -- 3.5.8 Computer Tools for Heat-exchanger Network Design -- 3.6 Energy Management in Unsteady Processes -- 3.6.1 Differential Energy Balances.
3.6.2 Energy Recovery in Batch and Cyclic Processes -- Semi-continuous Operation -- Sequencing Multiple Batches -- Indirect Heat Recovery -- References -- Nomenclature -- Problems -- 4 Process Simulation -- 4.1 Introduction -- 4.2 Process Simulation Programs -- 4.3 Specification of Components -- 4.3.1 Pure Components -- 4.3.2 Pseudocomponents -- 4.3.3 Solids and Salts -- 4.3.4 User Components -- 4.4 Selection of Physical Property Models -- 4.4.1 Sources of Physical Property Data -- 4.4.2 Prediction of Physical Properties -- Group Contribution Methods -- Reduced Properties -- 4.4.3 Phase-equilibrium Models -- 4.4.4 Prediction of Phase-equilibrium Constants -- Group Contribution Methods -- Sour-water Systems -- Electrolyte Systems -- Vapor-liquid Equilibrium at High Pressures -- Liquid-liquid Equilibrium -- 4.4.5 Choice of Phase-equilibrium Model for Design Calculations -- 4.4.6 Validation of Physical Property Models -- 4.5 Simulation of Unit Operations -- 4.5.1 Reactors -- Conversion Reactor (Stoichiometric Reactor) -- Equilibrium Reactor -- Gibbs Reactor -- Continuous Stirred Tank Reactor (CSTR) -- Plug-flow Reactor (PFR) -- Yield Shift Reactor -- Modeling Real Reactors -- 4.5.2 Distillation -- Shortcut Models -- Rigorous Models -- Column Convergence -- Complex Columns for Fractionation -- Column Sizing -- 4.5.3 Other Separations -- Component Splitter Models -- 4.5.4 Heat Exchange -- 4.5.5 Hydraulics -- 4.5.6 Solids Handling -- 4.6 User Models -- 4.6.1 Spreadsheet Models -- 4.6.2 User Subroutines -- 4.7 Flowsheets With Recycle -- 4.7.1 Tearing the Flowsheet -- 4.7.2 Convergence Methods -- Successive Substitution (Direct Substitution) -- Bounded Wegstein -- Newton and Quasi-Newton Methods -- 4.7.3 Manual Calculations -- 4.7.4 Convergence Problems -- 4.8 Flowsheet Optimization -- 4.8.1 Use of Controllers.
4.8.2 Optimization Using Process Simulation Software -- 4.9 Dynamic Simulation -- References -- Nomenclature -- Problems -- 5 Instrumentation and Process Control -- 5.1 Introduction -- 5.2 The P&I Diagram -- 5.2.1 Symbols and Layout -- 5.2.2 Basic Symbols -- Control Valves -- Actuators -- Instrument Lines -- Failure Mode -- General Instrument and Controller Symbols -- Distributed Control-Shared Display Symbols -- Other Common Symbols -- Type of Instrument -- 5.3 Process Instrumentation and Control -- 5.3.1 Instruments -- 5.3.2 Instrumentation and Control Objectives -- 5.3.3 Automatic Control Schemes -- Guide Rules -- 5.4 Conventional Control Schemes -- 5.4.1 Level Control -- 5.4.2 Pressure Control -- 5.4.3 Flow Control -- 5.4.4 Heat Exchangers -- Condenser Control -- Reboiler and Vaporizer Control -- 5.4.5 Cascade Control -- 5.4.6 Ratio Control -- 5.4.7 Distillation Column Control -- 5.4.8 Reactor Control -- 5.5 Alarms, Safety Trips, and Interlocks -- 5.5.1 Interlocks -- 5.6 Batch Process Control -- 5.7 Computer Control Systems -- References -- Problems -- 6 Materials of Construction -- 6.1 Introduction -- 6.2 Material Properties -- 6.3 Mechanical Properties -- 6.3.1 Tensile Strength -- 6.3.2 Stiffness -- 6.3.3 Toughness -- 6.3.4 Hardness -- 6.3.5 Fatigue -- 6.3.6 Creep -- 6.3.7 Effect of Temperature on the Mechanical Properties -- 6.4 Corrosion Resistance -- 6.4.1 Uniform Corrosion -- 6.4.2 Galvanic Corrosion -- 6.4.3 Pitting -- 6.4.4 Intergranular Corrosion -- 6.4.5 Effect of Stress -- 6.4.6 Erosion-corrosion -- 6.4.7 High-temperature Oxidation and Sulfidation -- 6.4.8 Hydrogen Embrittlement -- 6.5 Selection for Corrosion Resistance -- 6.5.1 Corrosion Charts -- 6.6 Material Costs -- 6.7 Contamination -- 6.7.1 Surface Finish -- 6.8 Commonly Used Materials of Construction -- 6.8.1 Iron and Steel -- 6.8.2 Stainless Steel -- Types.
Mechanical Properties.
Abstract:
"Bottom line: For a holistic view of chemical engineering design, this book provides as much, if not more, than any other book available on the topic" --Extract from Chemical Engineering Resources review Chemical Engineering Design is a complete course text for students of chemical engineering. Written for the Senior Design Course, and also suitable for introduction to chemical engineering courses, it covers the basics of unit operations and the latest aspects of process design, equipment selection, plant and operating economics, safety and loss prevention. It is a textbook that students will want to keep through their undergraduate education and on into their professional lives. New to this edition: Revised organization into Part I: Process Design, and Part II: Plant Design. The broad themes of Part I are flowsheet development, economic analysis, safety and environmental impact and optimization. Part II contains chapters on equipment design and selection that can be used as supplements to a lecture course or as essential references for students or practicing engineers working on design projects. New discussion of conceptual plant design, flowsheet development and revamp design Significantly increased coverage of capital cost estimation, process costing and economics New chapters on equipment selection, reactor design and solids handling processes New sections on fermentation, adsorption, membrane separations, ion exchange and chromatography Increased coverage of batch processing, food, pharmaceutical and biological processes All equipment chapters in Part II revised and updated with current information Updated throughout for latest US codes and standards, including API, ASME and ISA design codes and ANSI standards Additional worked examples and homework problems The most complete and up to date coverage of equipment selection 108 realistic
commercial design projects from diverse industries A rigorous pedagogy assists learning, with detailed worked examples, end of chapter exercises, plus supporting data and Excel spreadsheet calculations plus over 150 Patent References, for downloading from the companion website Extensive instructor resources: 1170 lecture slides plus fully worked solutions manual available to adopting instructors.
Local Note:
Electronic reproduction. Ann Arbor, Michigan : ProQuest Ebook Central, 2017. Available via World Wide Web. Access may be limited to ProQuest Ebook Central affiliated libraries.
Subject Term:
Genre:
Added Author:
Electronic Access:
Click to View