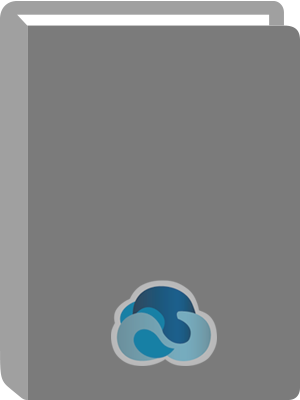
Handbook of Physical Vapor Deposition (PVD) Processing.
Title:
Handbook of Physical Vapor Deposition (PVD) Processing.
Author:
Mattox, Donald M.
ISBN:
9780815520382
Personal Author:
Edition:
2nd ed.
Physical Description:
1 online resource (793 pages)
Contents:
Front Cover -- Handbook of Physical Vapor Deposition (PVD) Processing -- Copyright Page -- Contents -- Preface to First Edition -- Preface to Second Edition -- Acknowledgements -- Acronyms -- Biography -- Chapter 1: Introduction -- 1.1 Surface Engineering -- 1.1.1 Physical Vapor Deposition (PVD) Processes -- 1.1.2 Non-PVD Thin Film Atomistic Deposition Processes -- 1.1.3 Applications of Vacuum-deposited Materials -- 1.2 Thin Film Processing -- 1.2.1 Stages of Fabrication -- 1.2.2 Factors that Affect Film Properties -- 1.2.3 Scale-Up and Manufacturability -- 1.3 Process Documentation -- 1.3.1 Process Specifications -- 1.3.2 Manufacturing Process Instructions (MPIs) -- 1.3.3 Travelers -- 1.3.4 Equipment and Calibration Logs -- 1.3.5 Commercial/Military Standards and Specifications (Mil Specs) -- 1.4 Safety and Environmental Concerns -- 1.5 Units -- 1.5.1 Temperature Scales -- 1.5.2 Energy Units -- 1.5.3 Prefixes -- 1.5.4 The Greek Alphabet -- 1.6 Summary -- Chapter 2: Substrate ("Real") Surfaces and Surface Modification -- 2.1 Introduction -- 2.2 Materials and Fabrication -- 2.2.1 Metals -- 2.2.2 Ceramics and Glasses -- 2.2.3 Polymers -- 2.3 Atomic Structure and Atom-particle Interactions -- 2.3.1 Atomic Structure and Nomenclature -- 2.3.2 Excitation and Atomic Transitions -- 2.3.3 Chemical Bonding -- 2.3.4 Probing and Detected Species -- 2.4 Characterization of Surfaces and Near-surface Regions -- 2.4.1 Elemental (Chemical) Compositional Analysis -- 2.4.2 Phase Composition and Microstructure -- 2.4.3 Molecular Composition and Chemical Bonding -- 2.4.4 Surface Morphology -- 2.4.5 Adsorption - Gases and Liquids -- 2.4.6 Mechanical and Thermal Properties of Surfaces -- 2.4.7 Surface Energy and Surface Tension -- 2.4.8 Acidic and Basic Properties of Surfaces -- 2.5 Bulk Properties -- 2.5.1 Outgassing -- 2.5.2 Outdiffusion.
2.6 Modification of Substrate Surfaces -- 2.6.1 Surface Morphology -- 2.6.2 Surface Hardness -- 2.6.3 Strengthening of Surfaces -- 2.6.4 Surface Composition -- 2.6.5 Surface "Activation" ("Functionalization") -- 2.6.6 Surface "Sensitization" -- 2.7 Summary -- Chapter 3: The "Good" Vacuum (Low Pressure) Processing Environment -- 3.1 Introduction -- 3.2 Gases and Vapors -- 3.2.1 Gas Pressure and Partial Pressure -- 3.2.2 Molecular Motion -- 3.2.3 Gas Flow -- 3.2.4 Ideal Gas Law -- 3.2.5 Vapor Pressure and Condensation -- 3.3 Gas-surface Interactions -- 3.3.1 Residence Time -- 3.3.2 Chemical Interactions -- 3.4 Vacuum Environment -- 3.4.1 Origin of Gases and Vapors -- 3.5 Vacuum Processing Systems -- 3.5.1 System Design Considerations and "Trade-Offs" -- 3.5.2 Processing Chamber Configurations -- 3.5.3 Equilibrium Conductance -- 3.5.4 Pumping Speed and Mass Throughput -- 3.5.5 Fixturing and Tooling -- 3.5.6 Feedthroughs and Accessories -- 3.5.7 Liners and Shields -- 3.5.8 Fail-Safe Designs -- 3.6 Vacuum pumping -- 3.6.1 Mechanical Pumps -- 3.6.2 Momentum Transfer Pumps -- 3.6.3 Capture Pumps -- 3.6.4 Hybrid Pumps -- 3.7 Vacuum- and Plasma-Compatible Materials -- 3.7.1 Metals -- 3.7.2 Ceramic and Glass Materials -- 3.7.3 Polymers -- 3.8 Assembly -- 3.8.1 Permanent Joining -- 3.8.2 Non-Permanent Joining -- 3.8.3 Lubricants for Vacuum Application -- 3.8.4 Heating and Cooling in Vacuums -- 3.9 Evaluating Vacuum System Performance -- 3.9.1 System Records -- 3.10 Purchasing a Vacuum System for PVD Processing -- 3.11 Cleaning of Vacuum Surfaces -- 3.11.1 Stripping -- 3.11.2 Cleaning -- 3.11.3 In Situ "Conditioning" of Vacuum Surfaces -- 3.12 System-related Contamination -- 3.12.1 Particulate Contamination -- 3.12.2 Vapor Contamination -- 3.12.3 Gaseous Contamination -- 3.12.4 Changes with Use -- 3.13 Process-related Contamination.
3.14 Safety Aspects of Vacuum Technology -- 3.15 Summary -- Chapter 4: The Sub-Atmospheric Processing Environment -- 4.1 Introduction -- 4.2 Pressure Monitoring and Control -- 4.3 Mass Flow Meters (MFMs) and Mass Flow Controllers (MFCs) -- 4.3.1 Liquid Precursors -- 4.4 Geometry of the Pumping Manifold -- 4.4.1 Pumps -- 4.5 Conduction -- 4.5.1 Downstream Flow Control (Throttling) -- 4.5.2 Transit Conductance -- 4.6 Distribution Manifolds for Gas Flow Uniformity -- 4.6.1 Changing Gas Cylinders -- 4.6.2 Effluent Removal -- 4.8 Conclusion -- Chapter 5: The Low Pressure Plasma Processing Environment -- 5.1 Introduction -- 5.2 The Plasma -- 5.2.1 Plasma Chemistry -- 5.2.2 Plasma Properties and Regions -- 5.3 Plasma-surface Interactions -- 5.3.1 Sheath Potentials and Self-bias -- 5.3.2 Applied Bias Potentials -- 5.3.3 Particle Bombardment Effects -- 5.3.4 Gas Diffusion into Surfaces -- 5.4 Configurations for Generating Plasmas -- 5.4.1 Electron Sources -- 5.4.2 Electric and Magnetic Field Effects -- 5.4.3 Direct Current (dc) Plasma Discharges -- 5.4.4 Pulsed Power Plasmas -- 5.4.5 Radio Frequency (rf) Capacitively Coupled Diode Discharge Plasmas -- 5.4.6 Arc Plasmas -- 5.4.7 Laser-Induced Plasmas -- 5.5 Ion and Plasma Sources -- 5.5.1 Plasma Sources -- 5.5.2 Ion Sources (Ion Guns) -- 5.5.3 Electron Sources -- 5.6 Plasma Processing Systems -- 5.6.1 Electrodes -- 5.6.2 Corrosion -- 5.6.3 Pumping Plasma Systems -- 5.7 Plasma-related Contamination -- 5.7.1 Desorbed Contamination -- 5.7.2 Sputtered Contamination -- 5.7.3 Arcing -- 5.7.4 Vapor Phase Nucleation -- 5.7.5 Cleaning Plasma Processing Systems -- 5.8 Some Safety Aspects of Plasma Processing -- 5.9 Summary -- Chapter 6: Vacuum Evaporation and Vacuum Deposition -- 6.1 Introduction -- 6.2 Thermal Vaporization -- 6.2.1 Vaporization of Elements -- 6.2.2 Vaporization of Alloys and Mixtures.
6.2.3 Vaporization of Compounds -- 6.2.4 Polymer Evaporation -- 6.3 Thermal Vaporization Sources -- 6.3.1 Single Charge Sources -- 6.3.2 Replenishing (Feeding) Sources -- 6.3.3 Baffle Sources -- 6.3.4 Beam and Confined Vapor Sources -- 6.3.5 Flash Evaporation -- 6.3.6 Radiant Heating -- 6.4 Transport of Vaporized Material -- 6.4.1 Masks -- 6.4.2 Post-Vaporization Ionization -- 6.4.3 Gas Scattering -- 6.5 Condensation of Vaporized Material -- 6.5.1 Condensation Energy -- 6.5.2 Deposition of Alloys and Mixtures -- 6.5.3 Deposition of Compounds from Compound Source Materials -- 6.5.4 Some Properties of Vacuum-Deposited Thin Films -- 6.6 Materials for Evaporation -- 6.6.1 Purity and Packaging -- 6.6.2 Handling of Source Materials -- 6.7 Vacuum Deposition Configurations -- 6.7.1 Deposition Chambers -- 6.7.2 Fixtures and Tooling -- 6.7.3 Shutters -- 6.7.4 Substrate Heating and Cooling -- 6.7.5 Liners and Shields -- 6.7.6 In Situ Cleaning -- 6.7.7 Getter Pumping Configurations -- 6.8 Process Monitoring and Control -- 6.8.1 Substrate Temperature Monitoring -- 6.8.2 Deposition Monitors - Rate and Total Mass -- 6.8.3 Vaporization Source Temperature Monitoring -- 6.8.4 In Situ Film Property Monitoring -- 6.9 Contamination from the Processing -- 6.9.1 Contamination from the Vaporization Source -- 6.9.2 Contamination from the Deposition System -- 6.9.3 Contamination from Substrates -- 6.9.4 Contamination from Deposited Film Material -- 6.10 Advantages and Disadvantages of Vacuum Deposition -- 6.11 Some Applications of Vacuum Deposition -- 6.11.1 Freestanding Structures -- 6.11.2 Graded Composition Structures -- 6.11.3 Multilayer Structures -- 6.11.4 Molecular Beam Epitaxy (MBE) -- 6.12 Gas Evaporation and Ultrafine (Nano) Particles -- 6.13 Other Processes -- 6.13.1 Reactive Evaporation and Activated Reactive Evaporation (ARE).
6.13.2 Jet Vapor Deposition Process -- 6.13.3 Field Evaporation -- 6.14 Summary -- Chapter 7: Physical Sputtering and Sputter Deposition (Sputtering) -- 7.1 Introduction -- 7.2 Physical Sputtering -- 7.2.1 Bombardment Effects on Surfaces -- 7.2.2 Sputtering Yields -- 7.2.3 Sputtering of Alloys and Mixtures -- 7.2.4 Sputtering Compounds -- 7.2.5 Distribution of Sputtered Flux -- 7.3 Sputtering Configurations -- 7.3.1 Cold Cathode Direct Current (dc) Diode (Non-magnetron) Sputtering -- 7.3.2 AC (Including Mid-frequency) Sputtering -- 7.3.3 Radio Frequency (rf) Sputtering -- 7.3.4 Direct Current (dc) Magnetron Sputtering -- 7.3.5 Pulsed Power Magnetron Sputtering -- 7.3.6 Dual (Redundant) "Anode" Sputtering -- 7.3.7 Ion and Plasma Beam Sputtering -- 7.4 Transport of the Sputter-vaporized Species -- 7.4.1 Thermalization -- 7.4.2 Scattering -- 7.4.3 Collimation -- 7.4.4 Post-vaporization Ionization -- 7.4.5 Gas Flow Sputtering -- 7.5 Condensation of Sputtered Species -- 7.5.1 Elemental and Alloy Deposition -- 7.5.2 Reactive Sputter Deposition -- 7.5.3 Deposition of Composite Films -- 7.5.4 Some Properties of Sputter-Deposited Thin Films -- 7.6 Sputter Deposition Geometries -- 7.6.1 Fixturing -- 7.6.2 Target Configurations -- 7.6.3 Ion and Plasma Sources -- 7.6.4 Plasma Activation Using Auxiliary Plasmas -- 7.7 Targets and Target Materials -- 7.7.1 Target Configurations -- 7.7.2 Target Materials -- 7.7.3 Target Cooling, Backing Plates, and Bonding -- 7.7.4 Target Shielding -- 7.7.5 Target Specifications -- 7.7.6 Target Surface Changes with Use -- 7.7.7 Target Conditioning (Pre-Sputtering) -- 7.7.8 Target Power Supplies -- 7.8 Process Monitoring and Control -- 7.8.1 Sputtering System -- 7.8.2 Pressure -- 7.8.3 Gas Composition -- 7.8.4 Gas Flow -- 7.8.5 Target Power and Voltage -- 7.8.6 Plasma Properties -- 7.8.7 Substrate Temperature.
7.8.8 Sputter Deposition Rate Monitoring.
Abstract:
This updated version of the popular handbook further explains all aspects of physical vapor deposition (PVD) process technology from the characterizing and preparing the substrate material, through deposition processing and film characterization, to post-deposition processing. The emphasis of the new edition remains on the aspects of the process flow that are critical to economical deposition of films that can meet the required performance specifications, with additional information to support the original material. The book covers subjects seldom treated in the literature: substrate characterization, adhesion, cleaning and the processing. The book also covers the widely discussed subjects of vacuum technology and the fundamentals of individual deposition processes. However, the author uniquely relates these topics to the practical issues that arise in PVD processing, such as contamination control and film growth effects, which are also rarely discussed in the literature. In bringing these subjects together in one book, the reader can understand the interrelationship between various aspects of the film deposition processing and the resulting film properties. The author draws upon his long experience with developing PVD processes and troubleshooting the processes in the manufacturing environment, to provide useful hints for not only avoiding problems, but also for solving problems when they arise. He uses actual experiences, called "war stories", to emphasize certain points. Special formatting of the text allows a reader who is already knowledgeable in the subject to scan through a section and find discussions that are of particular interest. The author has tried to make the subject index as useful as possible so that the reader can rapidly go to sections of particular interest. Extensive references allow the reader to pursue subjects in greater
detail if desired. The book is intended to be both an introduction for those who are new to the field and a valuable resource to those already in the field. The discussion of transferring technology between R&D and manufacturing provided in Appendix 1, will be of special interest to the manager or engineer responsible for moving a PVD product and process from R&D into production. Appendix 2 has an extensive listing of periodical publications and professional societies that relate to PVD processing. The extensive Glossary of Terms and Acronyms provided in Appendix 3 will be of particular use to students and to those not fully conversant with the terminology of PVD processing or with the English language. Fully revised and updated to include the latest developments in PVD process technology 'War stories' drawn from the author's extensive experience emphasize important points in development and manufacturing Appendices include listings of periodicals and professional societies, terms and acronyms, and material on transferring technology between R&D and manufacturing.
Local Note:
Electronic reproduction. Ann Arbor, Michigan : ProQuest Ebook Central, 2017. Available via World Wide Web. Access may be limited to ProQuest Ebook Central affiliated libraries.
Genre:
Electronic Access:
Click to View