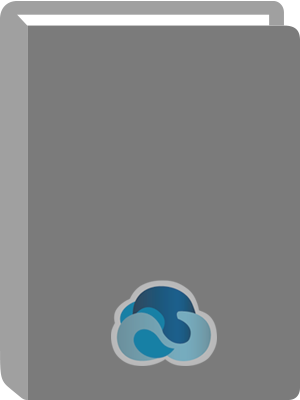
Performance-Based Gear Metrology : Kinematic - Transmission - Error Computation and Diagnosis.
Title:
Performance-Based Gear Metrology : Kinematic - Transmission - Error Computation and Diagnosis.
Author:
Mark, William D.
ISBN:
9781118357880
Personal Author:
Edition:
1st ed.
Physical Description:
1 online resource (290 pages)
Contents:
Performance-Based Gear Metrology -- Contents -- Preface -- Acknowledgments -- Chapter 1 Introduction -- 1.1 Transmission Error -- Frequency Spectrum -- Physical Sources of Harmonic Contributions -- 1.2 Mathematical Model -- Role of Discrete Fourier Transform (DFT) -- 1.3 Measurable Mathematical Representation of Working-Surface-Deviations -- Measurement Compatibility -- 1.4 Final Form of Kinematic-Transmission-Error Predictions -- Fundamental Assumptions and Parametric Dependence of Mesh-Attenuation Functions ˆφkl(n/N) -- 1.5 Diagnosing Transmission-Error Contributions -- Tooth-Meshing-Harmonic Contributions -- Kinematic-Transmission-Error Contributions -- 1.6 Application to Gear-Health Monitoring -- 1.7 Verification of Kinematic Transmission Error as a Source of Vibration Excitation and Noise -- 1.8 Gear Measurement Capabilities -- Contributions of Linear-Axis Errors -- Contributions of Rotary-Axis Errors -- Contributions of Probe Errors -- Effects of Statistical Averaging -- Summary of Required Measurement Capabilities -- Role of Working-Surface-Deviation Representation Method -- How Small is 0.1 μm (4 μin.)? -- References -- Chapter 2 Parallel-Axis Involute Gears -- 2.1 The Involute Tooth Profile -- 2.2 Parametric Description of Involute Helical Gear Teeth -- 2.3 Multiple Tooth Contact of Involute Helical Gears -- 2.4 Contact Ratios -- References -- Chapter 3 Mathematical Representation and Measurement of Working-Surface-Deviations -- 3.1 Transmission Error of Meshing-Gear-Pairs -- Definition of Transmission Error -- Additive Property of Transmission-Error Contributions -- 3.2 Tooth-Working-Surface Coordinate System -- Definition of Radial Coordinate -- 3.3 Gear-Measurement Capabilities -- 3.4 Common Types of Working-Surface Errors.
3.5 Mathematical Representation of Working-Surface-Deviations -- Legendre Polynomials -- Normalized Legendre Polynomials -- Representation Using Two-Dimensional Normalized Legendre Polynomials -- Interpretation of Expansion Coefficients -- Interpretation of Expansion Terms as Elementary Deviations or Errors -- Accumulated Tooth-Spacing (Index) Errors -- Rectangular Array of Expansion Coefficients -- 3.6 Working-Surface Representation Obtained from Line-Scanning Tooth Measurements -- Choice of Lead Measurements as Primary -- Choice of Profile Measurements as Primary -- Contributions from Secondary Measurement Sets -- 3.7 Example of Working-Surface Generations Obtained from Line-Scanning Measurements -- Individual Tooth Deviations -- Average Deviation Surfaces -- Appendix 3.A. Method for Estimating Required Number of Primary Line-Scanning Measurements Based on Surface-Roughness Criteria -- RMS Criterion Method -- Appendix 3.B. Method for Estimating Required Number of Primary Line-Scanning Measurements for Case of Known Ghost-Tone Rotational-Harmonic Number -- Minimum Number of Line-Scanning Measurements Required for Accurate Representation of Undulation Errors -- Example Calculation -- References -- Chapter 4 Rotational-Harmonic Analysis of Working-Surface Deviations -- 4.1 Periodic Sequence of Working-Surface Deviations at a Generic Tooth Location -- 4.2 Heuristic Derivation of Rotational-Harmonic Contributions -- 4.3 Rotational-Harmonic Contributions from Working-Surface Deviations -- Contributions from Mean-Working-Surface Deviations -- Contributions from Tooth-to-Tooth Variations in Working Surfaces -- Introduction of Normalized-Legendre-Polynomial Expansions of Working-Surface Deviations -- 4.4 Rotational-Harmonic Spectrum of Mean-Square Working-Surface Deviations.
Contributions from Mean and Tooth-to-Tooth Variations of Tooth-Working-Surface Deviations -- Comment on ''Aliasing'' -- Example Rotational-Harmonic Spectrum of Mean-Square Working-Surface Deviations -- 4.5 Tooth-Working-Surface Deviations Causing Specific Rotational-Harmonic Contributions -- Derivation of Working-Surface-Deviation Rotational-Harmonic Contributions -- 4.6 Discussion of Working-Surface Deviation Rotational-Harmonic Contributions -- Examples of Working-Surface Deviations Causing Specific Rotational-Harmonic Contributions -- Appendix 4.A. Formal Derivation of Equation (4.3) -- Appendix 4.B. Formulas for
Chapter 6 Diagnosing Manufacturing-Deviation Contributions to Transmission-Error Spectra -- 6.1 Main Features of Transmission-Error Spectra -- Effects of Transmission Path -- Harmonic Contributions from a Meshing-Gear-Pair -- Linear System Model of Mesh Attenuation -- Sources of Tooth-Meshing Harmonics -- Sources of Remaining Rotational Harmonics -- Effects of Torque and Speed Modulations -- 6.2 Approximate Formulation for Generic Manufacturing Deviations -- Mesh-Attenuation Functions -- Formulas for Contact Ratios -- Total Contact Ratio -- Spherical Bessel Functions -- Formulation for Sideband Amplitudes -- Fundamental Source of Sideband Amplitudes -- Effects of Mesh-Stiffness Fluctuations -- 6.3 Reduction of Results for Spur Gears -- Discussion of Spur Gear Results -- 6.4 Rotational-Harmonic Contributions from Accumulated Tooth-Spacing Errors -- Transmission-Error Contribution of a Slowly-Varying Accumulated Spacing Error -- Approximate Mesh-Attenuation Function for Tooth-Spacing Errors -- Low-Order Rotational Harmonic and ''Sideband'' Contributions from Tooth-Spacing Errors -- Role of Contact Ratios in Attenuating Tooth-Spacing-Error Low-Order Rotational and ''Sideband'' Harmonics -- 6.5 Rotational-Harmonic Contributions from Tooth-to-Tooth Variations Other Than Tooth-Spacing Errors -- Low-Order Rotational-Harmonic Contributions from Errors Other Than Tooth-Spacing Errors -- Working-Surface-Deviation Contributions to ''Sideband'' Rotational Harmonics -- Justification of the Term ''Mesh-Attenuation Function'' -- 6.6 Rotational-Harmonic Contributions from Undulation Errors -- Representation of Undulation Errors -- Mesh-Attenuation Function for Undulation Errors -- Requirement for Zero Attenuation of Undulation Errors -- Classic Manufacturing Source of ''Ghost Tones'' -- Unintended Contribution to Tooth-Meshing Harmonics.
Non-Integer Number of Undulation Cycles -- Diagnosing ''Ghost-Tone'' Manufacturing Sources -- Second ''Ghost Tone'' Example -- Understanding Rotational Harmonic Error-Pattern Generation, Equation (4.42) -- Contribution of ''Random'' Working-Surface Errors -- Third Ghost-Tone Example -- Comparison with Sound-Spectrum Measurement -- Independent Verification of Second Ghost-Tone Example -- 6.7 Explanation of Factors Enabling Successful Predictions -- How Small Is 0.1 μm (4 μin.)? -- Mathematical Model and Computational Accuracy -- Interpolation of Line-Scanning Tooth Measurements -- Effects of Consistent Linear-Axis Errors and Measurement-Probe Bias Errors -- Effects of Measurement Errors on Legendre Expansion Coefficients and on their DFTs Bkl(n) -- Effects of Surface Roughness and Statistical Averaging -- Appendix 6.A. Validation of Equation (6.46) -- References -- Chapter 7 Transmission-Error Decomposition and Fourier Series Representation -- 7.1 Decomposition of the Transmission Error into its Constituent Components -- Contact of Involute Helical Teeth -- Expression for Lineal Transmission Error -- 7.2 Transformation of Locations on Tooth Contact Lines to Working-Surface Coordinate System -- Location-Coordinate Transformation -- Line-Integral Transformation -- 7.3 Fourier-Series Representation of Working-Surface-Deviation Transmission-Error Contribution -- Expression for Fourier-Series Coefficients -- Introduction of Working-Surface-Deviation Generic Expansion Functions -- Evaluation of Generic Form of 'Mesh-Attenuation Functions'ˆφ'm(g) -- Application to Gear-Health Monitoring -- Results for ''Complete Set'' of Generic Expansion Functions on Rectangular Contact Regions -- Results Using Two-Dimensional Normalized Legendre Polynomials.
7.4 Fourier-Series Using Legendre Representation of Working-Surface-Deviations.
Abstract:
A mathematically rigorous explanation of how manufacturing deviations and damage on the working surfaces of gear teeth cause transmission-error contributions to vibration excitations Some gear-tooth working-surface manufacturing deviations of significant amplitude cause negligible vibration excitation and noise, yet others of minuscule amplitude are a source of significant vibration excitation and noise. Presently available computer-numerically-controlled dedicated gear metrology equipment can measure such error patterns on a gear in a few hours in sufficient detail to enable accurate computation and diagnosis of the resultant transmission-error vibration excitation. How to efficiently measure such working-surface deviations, compute from these measurements the resultant transmission-error vibration excitation, and diagnose the manufacturing source of the deviations, is the subject of this book. Use of the technology in this book will allow quality spot checks to be made on gears being manufactured in a production run, to avoid undesirable vibration or noise excitation by the manufactured gears. Furthermore, those working in academia and industry needing a full mathematical understanding of the relationships between tooth working-surface deviations and the vibration excitations caused by these deviations will find the book indispensable for applications pertaining to both gear-quality and gear-health monitoring. Key features: Provides a very efficient method for measuring parallel-axis helical or spur gears in sufficient detail to enable accurate computation of transmission-error contributions from working-surface deviations, and algorithms required to carry out these computations, including examples Provides algorithms for computing the working-surface deviations causing any user-identified tone, such as 'ghost tones,' or
'sidebands' of the tooth-meshing harmonics, enabling diagnosis of their manufacturing causes, including examples Provides explanations of all harmonics observed in gear-caused vibration and noise spectra. Enables generation of three-dimensional displays and detailed numerical descriptions of all measured and computed working-surface deviations, including examples.
Local Note:
Electronic reproduction. Ann Arbor, Michigan : ProQuest Ebook Central, 2017. Available via World Wide Web. Access may be limited to ProQuest Ebook Central affiliated libraries.
Genre:
Electronic Access:
Click to View