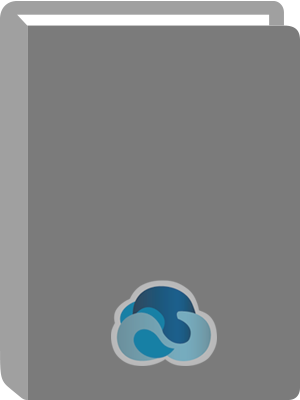
Wear of Advanced Materials.
Title:
Wear of Advanced Materials.
Author:
Davim, J. Paulo.
ISBN:
9781118565865
Personal Author:
Edition:
1st ed.
Physical Description:
1 online resource (141 pages)
Series:
Iste
Contents:
Cover -- Title Page -- Copyright Page -- Table of Contents -- Preface -- Chapter 1. Carbon Fabric-reinforced Polymer Composites and Parameters Controlling Tribological Performance -- 1.1. Introduction to polymeric tribo-composites -- 1.2. Carbon fibers as reinforcement -- 1.2.1. Classification of carbon fibers -- 1.2.2. Classification of fabric weaves -- 1.3. Carbon fabric-reinforced composites -- 1.3.1. Manufacturing methods to create CFRCs -- 1.3.2. Performance evaluation of composites -- 1.3.3. Tribological properties -- 1.4. Tribo-performance of CFRCs: influential parameters -- 1.4.1. Influence of the processing technique -- 1.4.2. Influence of fabric contents -- 1.4.3. Fabric orientation effect -- 1.4.4. Effect of fabric weave on performance properties -- 1.4.5. Influence of strengthening the fiber matrix interface -- 1.4.6. Influence of the type of polymer used -- 1.4.7. Influence of the molecular weight of a polymer -- 1.5. Concluding remarks -- 1.6. Bibliography -- A1.1. Appendix I: Various techniques for developing CFRCs by compression molding -- A1.1.1. Hand lay-up technique -- A1.1.2. Impregnation technique -- A1.1.3. Polymer film technique -- A1.1.4. Powder prepreg technique -- A2. Appendix II: Characterization methods for CFRCs -- A2.1. Physical characterization -- A2.2. Mechanical properties -- Chapter 2. Adhesive Wear Characteristics of Natural Fiber-reinforced Composites -- 2.1. Introduction -- 2.1.1. Why natural fibers? -- 2.1.2. Tribology of polymeric composites based on natural fibers -- 2.2. Preparation of polyester composites -- 2.2.1. Preparation of FRPC -- 2.2.2. Preparation of palm oil fibers and PORP composites -- 2.2.3. NaOH treatment -- 2.2.4. Preparation of PORP composites -- 2.3. Specifications of the fibers and composites -- 2.3.1. Interfacial adhesion of palm oil fibers.
2.3.2. Mechanical properties of the composites -- 2.4. Tribo-experimental details -- 2.4.1. Experimental procedure -- 2.4.2. Examination of worn surfaces -- 2.4.3. Parameters measured -- 2.4.4. Results and discussion -- 2.4.5. Effect of operating parameters -- 2.4.6. Effect of 6% NaOH treatment -- 2.4.7. Effect of wet and dry contact conditions -- 2.5. Summary -- 2.6. Bibliography -- Chapter 3. Resistance to Cavitation Erosion: Material Selection -- 3.1. Cavitation erosion of materials - a brief review -- 3.2. Measuring the wear resistance of a material to cavitation erosion by using a vibratory cavitation erosion apparatus -- 3.2.1. General view of an ultrasonic vibratory apparatus -- 3.2.2. Determination of the wear resistance of a material to cavitation erosion -- 3.2.3. Experimental details -- 3.3. Material selection -- 3.3.1. Metal and alloys -- 3.3.2. Advanced ceramic -- 3.3.3. Polymer -- 3.3.4. Comparison -- 3.4. Conclusion -- 3.5. Acknowledgement -- 3.6. Bibliography -- Chapter 4. Cavitation of Biofuel Applied in the Injection Nozzles of Diesel Engines -- 4.1. Introduction -- 4.2. General understanding of cavitation erosion -- 4.2.1. Mechanism of cavitation erosion -- 4.2.2. Synergistic effect of cavitation erosion and corrosion -- 4.3. Hydraulic characteristics of cavitation flow -- 4.3.1. Numerical models and validation -- 4.3.2. Effect of boundary pressure on cavitation -- 4.3.3. Effect of nozzle geometry on cavitation -- 4.4. Influence of fuel property on cavitation. -- 4.4.1. Cavitating flow characteristics -- 4.4.2. Variation in the characteristics of dimensionless parameters -- 4.4.3. Effect of fuel properties on cavitation inception -- 4.5. Cavitation erosion of biofuel in the diesel injection nozzle -- 4.5.1. Effect of cavitation erosion on a nozzle -- 4.5.2. Location of cavitation erosion in a nozzle.
4.5.3. Factors that influence cavitation erosion in nozzles -- 4.5.4. Effect of biofuel on the erosion of nozzles -- 4.6. Conclusion -- 4.7. Acknowledgments -- 4.8. Bibliography -- Chapter 5. Wear and Corrosion Damage of Medical-grade Metals and Alloys -- 5.1. Introduction -- 5.1.1. Total joint replacements -- 5.1.2. Metal alloys -- 5.2. Clinical studies and mechanistic investigation into implant failure -- 5.2.1. Wear mechanisms -- 5.2.2. Physiological corrosion of metals -- 5.2.3. Bio-tribo-corrosion at the modular interface -- 5.2.4. Adverse effects due to the creation of wear particles -- 5.3. Residual stress development by rough surface contact -- 5.3.1. Surface properties of bio-implants -- 5.3.2. Stress-assisted electrochemical dissolution and local corrosion damage -- 5.4. Conclusion -- 5.5. Bibliography -- List of Authors -- Index.
Abstract:
Recent advances into the wear of advanced materials In general, wear is currently defined as "the progressive loss of material from the operating surface of a body occurring as a result of relative motion at the surface". It is related to surface interactions and more specifically to the form of contact due to relative motion. Wear is rarely catastrophic but does reduce the operating efficiency of machine components and structures. At this time of economic crisis, this is a very important field of study because of the huge impact the wear of materials has on the economy. The purpose of this book is to present a collection of examples illustrating the state of the art and research developments into the wear of advanced materials in several applications. It can be used as a research book for a final undergraduate engineering course (for example into materials, mechanics, etc.) or as the focus of the effect of wear on advanced materials at a postgraduate level. It can also serve as a useful reference for academics, biomaterials researchers, mechanical and materials engineers, and professionals in related spheres working with tribology and advanced materials.
Local Note:
Electronic reproduction. Ann Arbor, Michigan : ProQuest Ebook Central, 2017. Available via World Wide Web. Access may be limited to ProQuest Ebook Central affiliated libraries.
Genre:
Electronic Access:
Click to View