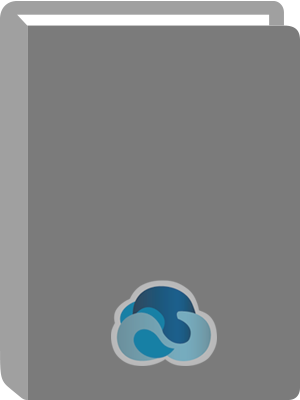
Practical Residual Stress Measurement Methods.
Title:
Practical Residual Stress Measurement Methods.
Author:
Schajer, Gary S.
ISBN:
9781118402825
Personal Author:
Edition:
1st ed.
Physical Description:
1 online resource (379 pages)
Contents:
Cover -- Title Page -- Copyright -- Contents -- List of Contributors -- Preface -- Chapter 1 Overview of Residual Stresses and Their Measurement -- 1.1 Introduction -- 1.1.1 Character and Origin of Residual Stresses -- 1.1.2 Effects of Residual Stresses -- 1.1.3 Residual Stress Gradients -- 1.1.4 Deformation Effects of Residual Stresses -- 1.1.5 Challenges of Measuring Residual Stresses -- 1.1.6 Contribution of Modern Measurement Technologies -- 1.2 Relaxation Measurement Methods -- 1.2.1 Operating Principle -- 1.3 Diffraction Methods -- 1.3.1 Measurement Concept -- 1.3.2 X-ray Diffraction -- 1.3.3 Synchrotron X-ray -- 1.3.4 Neutron Diffraction -- 1.4 Other Methods -- 1.4.1 Magnetic -- 1.4.2 Ultrasonic -- 1.4.3 Thermoelastic -- 1.4.4 Photoelastic -- 1.4.5 Indentation -- 1.5 Performance and Limitations of Methods -- 1.5.1 General Considerations -- 1.5.2 Performance and Limitations of Methods -- 1.6 Strategies for Measurement Method Choice -- 1.6.1 Factors to be Considered -- 1.6.2 Characteristics of Methods -- References -- Chapter 2 Hole Drilling and Ring Coring -- 2.1 Introduction -- 2.1.1 Introduction and Context -- 2.1.2 History -- 2.1.3 Deep Hole Drilling -- 2.2 Data Acquisition Methods -- 2.2.1 Strain Gages -- 2.2.2 Optical Measurement Techniques -- 2.3 Specimen Preparation -- 2.3.1 Specimen Geometry and Strain Gage Selection -- 2.3.2 Surface Preparation -- 2.3.3 Strain Gage Installation -- 2.3.4 Strain Gage Wiring -- 2.3.5 Instrumentation and Data Acquisition -- 2.4 Hole Drilling Procedure -- 2.4.1 Drilling Cutter Selection -- 2.4.2 Drilling Machines -- 2.4.3 Orbital Drilling -- 2.4.4 Incremental Measurements -- 2.4.5 Post-drilling Examination of Hole and Cutter -- 2.5 Computation of Uniform Stresses -- 2.5.1 Mathematical Background -- 2.5.2 Data Averaging -- 2.5.3 Plasticity Effects.
2.5.4 Ring Core Measurements -- 2.5.5 Optical Measurements -- 2.5.6 Orthotropic Materials -- 2.6 Computation of Profile Stresses -- 2.6.1 Mathematical Background -- 2.7 Example Applications -- 2.7.1 Shot-peened Alloy Steel Plate-Application of the Integral Method -- 2.7.2 Nickel Alloy Disc-Fine Increment Drilling -- 2.7.3 Titanium Test-pieces-Surface Processes -- 2.7.4 Coated Cylinder Bore-Adaptation of the Integral Method -- 2.8 Performance and Limitations of Methods -- 2.8.1 Practical Considerations -- 2.8.2 Common Uncertainty Sources -- 2.8.3 Typical Measurement Uncertainties -- References -- Chapter 3 Deep Hole Drilling -- 3.1 Introduction and Background -- 3.2 Basic Principles -- 3.2.1 Elastic Analysis -- 3.2.2 Effects of Plasticity -- 3.3 Experimental Technique -- 3.4 Validation of DHD Methods -- 3.4.1 Tensile Loading -- 3.4.2 Shrink Fitted Assembly -- 3.4.3 Prior Elastic-plastic Bending -- 3.4.4 Quenched Solid Cylinder -- 3.5 Case Studies -- 3.5.1 Welded Nuclear Components -- 3.5.2 Components for the Steel Rolling Industry -- 3.5.3 Fibre Composites -- 3.6 Summary and Future Developments -- Acknowledgments -- References -- Chapter 4 The Slitting Method -- 4.1 Measurement Principle -- 4.2 Residual Stress Profile Calculation -- 4.3 Stress Intensity Factor Determination -- 4.4 Practical Measurement Procedures -- 4.5 Example Applications -- 4.6 Performance and Limitations of Method -- 4.7 Summary -- References -- Chapter 5 The Contour Method -- 5.1 Introduction -- 5.1.1 Contour Method Overview -- 5.1.2 Bueckner's Principle -- 5.2 Measurement Principle -- 5.2.1 Ideal Theoretical Implementation -- 5.2.2 Practical Implementation -- 5.2.3 Assumptions and Approximations -- 5.2.3.1 Elastic Stress Release and Stress Free Cutting Process -- 5.2.3.2 Starting with Flat Surface in Analysis.
5.2.3.3 Part is Symmetric About Cut Plane -- 5.2.3.4 Anti-symmetric Cutting Errors Average Away -- 5.2.3.5 Symmetric Errors: Cutting Irregularities -- 5.2.3.6 Bulge Error -- 5.2.3.7 No Assumptions of Isotropic or Homogeneous Elasticity Required -- 5.3 Practical Measurement Procedures -- 5.3.1 Planning the Measurement -- 5.3.2 Fixturing -- 5.3.3 Cutting the Part -- 5.3.4 Measuring the Surfaces -- 5.4 Residual Stress Evaluation -- 5.4.1 Basic Data Processing -- 5.4.1.1 Align the Coordinate Frames -- 5.4.1.2 Construction of FE Model -- 5.4.1.3 Average the Two Sides -- 5.4.1.4 Filter the Noise -- 5.4.1.5 Transfer to FEM -- 5.4.1.6 Reporting Results -- 5.4.2 Additional Issues -- 5.4.2.1 Order of Data Processing Steps -- 5.4.2.2 Extrapolation -- 5.4.2.3 No Filtering -- 5.4.2.4 Stress-free Test Cut -- 5.5 Example Applications -- 5.5.1 Experimental Validation and Verification -- 5.5.1.1 Indented Stainless Steel Disk Compared With Neutron Diffraction -- 5.5.1.2 Linear Friction Weld Compared With Neutron Diffraction -- 5.5.1.3 Laser Peened Plate Compared with Slitting and X-ray Diffraction with Layer Removal -- 5.5.2 Unique Measurements -- 5.5.2.1 Large Dissimilar Metal Weld From a Nuclear Power Plant -- 5.5.2.2 Railroad Rail -- 5.6 Performance and Limitations of Methods -- 5.6.1 Near Surface (Edge) Uncertainties -- 5.6.2 Size Dependence -- 5.6.3 Systematic Errors -- 5.6.3.1 Bulge -- 5.6.3.2 Plasticity -- 5.7 Further Reading On Advanced Contour Method Topics -- 5.7.1 Superposition For Additional Stresses -- 5.7.2 Cylindrical Parts -- 5.7.3 Miscellaneous -- 5.7.4 Patent -- Acknowledgments -- References -- Chapter 6 Applied and Residual Stress Determination Using X-ray Diffraction -- 6.1 Introduction -- 6.2 Measurement of Lattice Strain -- 6.3 Analysis of Regular dφψ vs. sin2ψ Data -- 6.3.1 Dölle-Hauk Method.
6.3.2 Winholtz-Cohen Least-squares Analysis -- 6.4 Calculation of Stresses -- 6.5 Effect of Sample Microstructure -- 6.6 X-ray Elastic Constants (XEC) -- 6.6.1 Constitutive Equation -- 6.6.2 Grain Interaction -- 6.7 Examples -- 6.7.1 Isotropic, Biaxial Stress -- 6.7.2 Triaxial Stress -- 6.7.3 Single-crystal Strain -- 6.8 Experimental Considerations -- 6.8.1 Instrumental Errors -- 6.8.2 Errors Due to Counting Statistics and Peak-fitting -- 6.8.3 Errors Due to Sampling Statistics -- 6.9 Summary -- Acknowledgments -- References -- Chapter 7 Synchrotron X-ray Diffraction -- 7.1 Basic Concepts and Considerations -- 7.1.1 Introduction -- 7.1.2 Production of X-rays -- Undulators, Wigglers, and Bending Magnets -- 7.1.3 The Historical Development of Synchrotron Sources -- 7.1.4 Penetrating Capability of Synchrotron X-rays -- 7.2 Practical Measurement Procedures and Considerations -- 7.2.1 Defining the Strain Measurement Volume and Measurement Spacing -- 7.2.2 From Diffraction Peak to Lattice Spacing -- 7.2.3 From Lattice Spacing to Elastic Strain -- 7.2.4 From Elastic Strain to Stress -- 7.2.5 The Precision of Diffraction Peak Measurement -- 7.2.6 Reliability, Systematic Errors and Standardization -- 7.3 Angle-dispersive Diffraction -- 7.3.1 Experimental Set-up, Detectors, and Data Analysis -- 7.3.2 Exemplar: Mapping Stresses Around Foreign Object Damage -- 7.3.3 Exemplar: Fast Strain Measurements -- 7.4 Energy-dispersive Diffraction -- 7.4.1 Experimental Set-up, Detectors, and Data Analysis -- 7.4.2 Exemplar: Crack Tip Strain Mapping at High Spatial Resolution -- 7.4.3 Exemplar: Mapping Stresses in Thin Coatings and Surface Layers -- 7.5 New Directions -- 7.6 Concluding Remarks -- References -- Chapter 8 Neutron Diffraction -- 8.1 Introduction -- 8.1.1 Measurement Concept -- 8.1.2 Neutron Technique -- 8.1.3 Neutron Diffraction.
8.1.4 3-Dimensional Stresses -- 8.1.5 Neutron Path Length -- 8.2 Formulation -- 8.2.1 Determination of the Elastic Strains from the Lattice Spacings -- 8.2.2 Relationship between the Measured Macroscopic Strain in a given Direction and the Elements of the Strain Tensor -- 8.2.3 Relationship between the Stress σi,j and Strain εi,j Tensors -- 8.3 Neutron Diffraction -- 8.3.1 Properties of the Neutron -- 8.3.2 The Strength of the Diffracted Intensity -- 8.3.3 Cross Sections for the Elements -- 8.3.4 Alloys -- 8.3.5 Differences with Respect to X-rays -- 8.3.6 Calculation of Transmission -- 8.4 Neutron Diffractometers -- 8.4.1 Elements of an Engineering Diffractometer -- 8.4.2 Monochromatic Beam Diffraction -- 8.4.3 Time-of-flight Diffractometers -- 8.5 Setting up an Experiment -- 8.5.1 Choosing the Beam-defining Slits or Radial Collimators -- 8.5.2 Calibration of the Wavelength and Effective Zero of the Angle Scale, 2θ0 -- 8.5.3 Calibration of a Time-of-flight Diffractometer -- 8.5.4 Positioning the Sample on the Table -- 8.5.5 Measuring Reference Samples -- 8.6 Analysis of Data -- 8.6.1 Monochromatic Beam Diffraction -- 8.6.2 Analysis of Time-of-flight Diffraction -- 8.6.3 Precision of the Measurements -- 8.7 Systematic Errors in Strain Measurements -- 8.7.1 Partly Filled Gage Volumes -- 8.7.2 Large Grain Effects -- 8.7.3 Incorrect Use of Slits -- 8.7.4 Intergranular Effects -- 8.8 Test Cases -- 8.8.1 Stresses in Indented Discs -- Neutrons, Contour Method and Finite Element Modeling -- 8.8.2 Residual Stress in a Three-pass Bead-in-slot Weld -- Acknowledgments -- References -- Chapter 9 Magnetic Methods -- 9.1 Principles -- 9.1.1 Introduction -- 9.1.2 Ferromagnetism -- 9.1.3 Magnetostriction -- 9.1.4 Magnetostatic and Magneto-elastic Energy -- 9.1.5 The Hysteresis Loop.
9.1.6 An Introduction to Magnetic Measurement Methods.
Abstract:
An introductory and intermediate level handbook written in pragmatic style to explain residual stresses and to provide straightforward guidance about practical measurement methods. Residual stresses play major roles in engineering structures, with highly beneficial effects when designed well, and catastrophic effects when ignored. With ever-increasing concern for product performance and reliability, there is an urgent need for a renewed assessment of traditional and modern measurement techniques. Success critically depends on being able to make the most practical and effective choice of measurement method for a given application. Practical Residual Stress Measurement Methods provides the reader with the information needed to understand key residual stress concepts and to make informed technical decisions about optimal choice of measurement technique. Each chapter, written by invited specialists, follows a focused and pragmatic format, with subsections describing the measurement principle, residual stress evaluation, practical measurement procedures, example applications, references and further reading. The chapter authors represent both international academia and industry. Each of them brings to their writing substantial hands-on experience and expertise in their chosen field. Fully illustrated throughout, the book provides a much-needed practical approach to residual stress measurements. The material presented is essential reading for industrial practitioners, academic researchers and interested students. Key features: Presents an overview of the principal residual stress measurement methods, both destructive and non-destructive, with coverage of new techniques and modern enhancements of established techniques Includes stand-alone chapters, each with its own figures, tables and list of references, and written by an invited team of
international specialists.
Local Note:
Electronic reproduction. Ann Arbor, Michigan : ProQuest Ebook Central, 2017. Available via World Wide Web. Access may be limited to ProQuest Ebook Central affiliated libraries.
Subject Term:
Genre:
Electronic Access:
Click to View