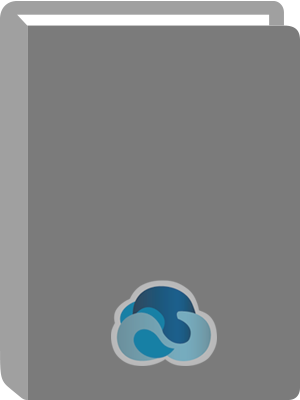
Analysis of adhesively bonded composite aerospace structures developed by laser surface treatment
Title:
Analysis of adhesively bonded composite aerospace structures developed by laser surface treatment
Author:
Nuhoğlu, Kaan, author.
Personal Author:
Physical Description:
xiv, 99 leaves: charts;+ 1 computer laser optical disc
Abstract:
Among the various joining techniques, adhesive bonding is a feasible alternative to mechanical fasteners to prevent incisions and discontinuity on aerospace structures. The performance of the bonded structures highly depends on the adhesion strength, which is directly related to the condition of the bonding surface. It is for this that laser surface treatment, a recently developing technique to improve bonding performance, has become suited for CFRP structures. Yet, predicting the failure strength and mechanism is vital for designing primary aircraft structures involving adhesively bonded composite structures. The scope of this paper consists of the validation and evaluation of adhesive bonding behavior in the case of joining between laser surface-treated CFRP structures, in particular, components of an aircraft wing box. To this end, both the experiment and numerical investigations of the secondary bonded coupons were examined. This study, in other words, includes experimentally revealing the bonding behavior through coupon and element-level mechanical test setups, as well as the simulation of those structures in the computer environment by performing FEA to predict the failure load and damage growth. In this regard, besides observing the effects of the laser surface treatment on the pure and mix-mode behaviors by means of the DCB, ENF, SLJ, and SSJ tests, identical specimens were numerically analyzed by utilizing macro-scale 2D and 3D models, employing the CZM technique. Meanwhile, a novel characterization study and the resulting TSL parameter identification method were achieved for an accurate numerical analysis. Eventually, in addition to the application methodology, the capabilities and appropriateness of the presented FEA method were discussed, comparing experimental and numerical results.
Added Author:
Added Corporate Author:
Added Uniform Title:
Thesis (Master)--İzmir Institute of Technology: Mechanical Engineering.
İzmir Institute of Technology: Mechanical Engineering--Thesis (Master).
Electronic Access:
Access to Electronic Versiyon.