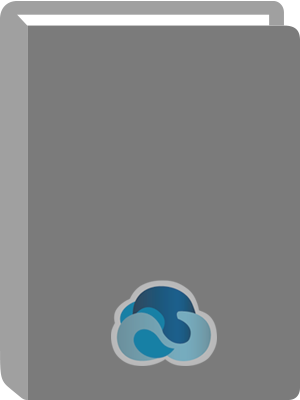
Maximizing Machinery Uptime.
Title:
Maximizing Machinery Uptime.
Author:
Bloch, Heinz P.
ISBN:
9780080465807
Personal Author:
Edition:
1st ed.
Physical Description:
1 online resource (673 pages)
Series:
Practical Machinery Management for Process Plants ; v.5
Practical Machinery Management for Process Plants
Contents:
Cover -- Frontmatter -- Half Title Page -- Title Page -- Copyright -- Contents -- Acknowledgments -- Preface -- 1. Introduction -- Grooming Talent and Skills -- Sound Organizational Setup Explained -- PdM, TPM, TPR, and ODR/DSS Explained -- Reliability-Focused Plants and Operator Involvement -- Awareness of Availability Needs and Outage and Turnaround Planning -- Insurance and Spare Parts Philosophies -- Reliability-Focus versus Repair-Focus -- Mentoring, Resources, and Networking -- More Keys to a Productive Reliability Workforce -- "CARE" - Deming's Method Streamlined and Adapted to Our Time -- References -- Bibliography -- 2. The meaning of reliability -- System and Mission -- Assembly and Part -- Assembly Hierarchy -- Failure -- Failure Mode -- Service Life -- Reliability -- Maintainability -- Surveillability -- Availability -- References -- 3. Uptime as probability of success -- References -- 4. Estimating machinery uptime -- Estimation of Failure Distributions for Machinery Components -- Application of Failure Distributions -- Obtaining the Weibull Function -- Construction of the Replacement Model -- Data Sources -- Analysis of Run-Time Data -- Analysis of Pumps -- Analysis of Motors -- Analysis of Rebuild Data -- Life Comparison With Other Industrial Experience -- Conclusion -- References -- 5. Is there a universal approach to predicting machinery uptime? -- Reliability of Parts In Series -- Two Components In Parallel -- Three Identical Components In Parallel -- Prediction Procedures -- Failure Rate Data -- The Procedure -- Current Methods of Predicting Reliability -- Development of the Handbook -- Example Design Evaluation Procedure -- Validation of Reliability Prediction Equations -- Summary -- References -- 6. Predicting uptime of turbomachinery -- Interpretation of Reliability Factors (RF) -- Factors Influencing Reliability -- Examples.
Application Issues for Centrifugal Pumps -- Pump Selection Reliability Factors -- Comparison with Field Experience -- Summary -- Bibliography -- 7. Failure mode and effect analysis -- The Process -- Design FMEA -- Definitions and FMEA Forms -- Procedure -- Examples -- The FMEA Form -- Evaluation -- Examples -- References -- 8. Fault tree analysis -- Procedure -- Examples -- Assessment and Evaluation -- Review -- References -- 9. Machinery risk and hazard assessment -- Assessing Risk -- Assessing Hazards -- Preliminary Hazard Analysis (PHA) -- Hazard and Operability (HAZOP) Study -- References -- 10. Machinery system availability analysis -- The Prediction Approach -- Machinery System Unavailability -- Priorities -- The Operations Management Approach -- 11. Practical field uptime assessment -- The Reliability Index Number -- Determining the Reliability Index Number -- Equipment Replacement and Rebuilding -- The Machinery Complexity Number -- 12. Life-cycle cost analysis -- Asset Management -- Examples -- Repairing Pumps -- Life-Cycle Costing of Pumps -- Piping -- LCC is a Total -- Benchmarking -- From Theory to Practice -- Gearbox LLC Evaluation -- Making LCC Policy -- References -- Bibliography -- 13. Starting with good specifications -- Apply Mechanical Reliability Principles to Turbomachinery Design: Use these Guidelines to Improve Availability -- Origins of Turbomachinery -- Machinery Reliability by Design -- Mechanical Reliability Design Principles -- Designing Out a Failure Mode -- Applying the Integral Design Principle -- Building Reliability into Your Reciprocating Compressor Specifications -- Improving Mechanical Design Reliability -- Mechanical Design Specifications -- Future Design Improvements to reduce this Failure Mode (These are not Presently Available): -- Monitoring -- Concluding Comments -- References -- Other Sources.
14. Owner-contractor interfaces and equipment availability -- Introduction -- Operating Standards are Needed to Define Availability Goals -- Some Interface Problems and their Solutions -- Flow Sheets and Specification -- Field Installation and Equipment Turnover -- Evaluation -- Conclusion -- Quality Machinery Installation does not have to Cost More -- References -- Bibliography -- 15. The operational environment -- Process Safety Management (PSM): An Important Component of Machinery Uptime -- A Reliability Policy - Do You Have One? - Why Not? -- What We Can Learn from Others -- What are Best Machinery Practices? -- Operator Training will Contribute to Uptime -- Effective Machinery Monitoring: Getting the Most for Your Investment -- A Spare Equipment Policy is Needed -- References -- 16. The maintenance environment -- Introduction -- Asset Management: The Essential Foundation for Plant Optimization -- Definition -- Process Overview -- Overall Strategy -- About Maintenance Strategies -- Why Training of Machinery Maintenance Forces is Important or No News is Good News -- Machinery Maintenance Effectiveness Assessment: An Example -- Machinery Uptime and Computerized Maintenance Management Systems -- Maintenance Effectiveness Audits -- References -- 17. Continuous improvement -- Predict Future Failures From Your Maintenance Records -- Examples -- Laying Hands On -- References -- 18. Review of mechanical structures and piping for machinery -- Overview, Design, and Case Studies: Introduction -- Design Criteria -- Design Loads -- Classification of Computed Stresses -- Evaluation of Computed Stresses -- Selection of Materials -- Layout Considerations -- Support Configuration -- Types of Support -- ASME Code Calculation for Shells Under Internal Pressure -- ASME Code Calculation for Shells Under External Pressure.
Piping Code Calculation for Pipe Under Internal Pressure -- Branch Connection Reinforcement -- Stress Analysis/Flexibility Analysis -- Piping Flexibility Analysis -- Flexibility Characteristics -- Centrifugal Pump Piping Systems -- Steam Turbines -- Centrifugal Compressor Piping -- Air-Cooled Heat Exchanger Piping -- Fired Heater Piping -- Tank Piping -- Pitfalls and Misunderstandings -- Allowable Load Revisited -- Excessive Flexibility is not Desirable -- How Theoretical Restraints Often Differ from Actual Ones -- Special Concern: Expansion Joints -- Other Practical Considerations -- What is it Worth to do it Right? -- Bibliography -- Appendix A: The coin toss case -- Appendix B: Safety design checklist for equipment reliability professionals -- Appendix C: Machinery system completeness and reliability appraisal forms -- Centrifugal Pumps -- General Purpose Steam Turbines -- General Purpose Steam Turbines -- Special Purpose Centrifugal Fans -- Small Bore Pipe and Tubing -- Glossary -- Index.
Abstract:
The authors use their decades of experience and draw upon real-world examples to demonstrate that the application of their techniques provides a basis for equipment management, uptime maximization, and reduced maintenance costs. The text explores reliability assessment techniques such as Failure Mode, Effect Analysis, and Fault Tree Analysis of commonly encountered rotating machinery. These are all highly effective techniques that the engineer can apply to maximize uptime and thereby maximize production and profitability. *Provides the tools to drastically improve machinery productivity and performance *Bridges the gap between the theory of "reliability engineering" and the practical day-to-day measures that lead to machinery uptime *Authoritative reference for maximizing the uptime of process equipment.
Local Note:
Electronic reproduction. Ann Arbor, Michigan : ProQuest Ebook Central, 2017. Available via World Wide Web. Access may be limited to ProQuest Ebook Central affiliated libraries.
Genre:
Added Author:
Electronic Access:
Click to View