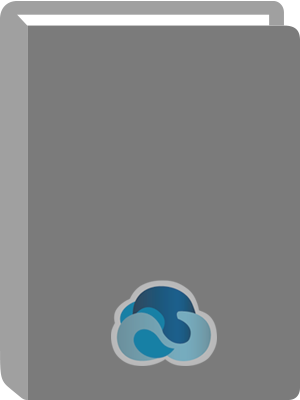
Process Intensification Technologies for Green Chemistry : Engineering Solutions for Sustainable Chemical Processing.
Title:
Process Intensification Technologies for Green Chemistry : Engineering Solutions for Sustainable Chemical Processing.
Author:
Boodhoo, Kamelia.
ISBN:
9781118498538
Personal Author:
Edition:
1st ed.
Physical Description:
1 online resource (478 pages)
Contents:
Process Intensification For Green Chemistry: Engineering Solutions for Sustainable Chemical Processing -- Contents -- List of Contributors -- Preface -- 1 Process Intensification: An Overview of Principles and Practice -- 1.1 Introduction -- 1.2 Process Intensification: Definition and Concept -- 1.3 Fundamentals of Chemical Engineering Operations -- 1.3.1 Reaction Engineering -- 1.3.2 Mixing Principles -- 1.3.3 Transport Processes -- 1.4 Intensification Techniques -- 1.4.1 Enhanced Transport Processes -- 1.4.2 Integrating Process Steps -- 1.4.3 Moving from Batch to Continuous Processing -- 1.5 Merits of PI Technologies -- 1.5.1 Business -- 1.5.2 Process -- 1.5.3 Environment -- 1.6 Challenges to Implementation of PI -- 1.7 Conclusion -- Nomenclature -- Greek Letters -- References -- 2 Green Chemistry Principles -- 2.1 Introduction -- 2.1.1 Sustainable Development and Green Chemistry -- 2.2 The Twelve Principles of Green Chemistry -- 2.2.1 Ideals of Green Chemistry -- 2.3 Metrics for Chemistry -- 2.3.1 Effective Mass Yield -- 2.3.2 Carbon Efficiency -- 2.3.3 Atom Economy -- 2.3.4 Reaction Mass Efficiency -- 2.3.5 Environmental (E) Factor -- 2.3.6 Comparison of Metrics -- 2.4 Catalysis and Green Chemistry -- 2.4.1 Case Study: Silica as a Catalyst for Amide Formation -- 2.4.2 Case Study: Mesoporous Carbonaceous Material as a Catalyst Support -- 2.5 Renewable Feedstocks and Biocatalysis -- 2.5.1 Case Study: Wheat Straw Biorefinery -- 2.6 An Overview of Green Chemical Processing Technologies -- 2.6.1 Alternative Reaction Solvents for Green Processing -- 2.6.2 Alternative Energy Reactors for Green Chemistry -- 2.7 Conclusion -- References -- 3 Spinning Disc Reactor for Green Processing and Synthesis -- 3.1 Introduction -- 3.2 Design and Operating Features of SDRs -- 3.2.1 Hydrodynamics -- 3.2.2 SDR Scale-up Strategies -- 3.3 Characteristics of SDRs.
3.3.1 Thin-film Flow and Surface Waves -- 3.3.2 Heat and Mass Transfer -- 3.3.3 Mixing Characteristics -- 3.3.4 Residence Time and Residence Time Distribution -- 3.3.5 SDR Applications -- 3.4 Case Studies: SDR Application for Green Chemical Processing and Synthesis -- 3.4.1 Cationic Polymerization using Heterogeneous Lewis Acid Catalysts -- 3.4.2 Solvent-free Photopolymerization Processing -- 3.4.3 Heterogeneous Catalytic Organic Reaction in the SDR: An Example of Application to the Pharmaceutical/Fine Chemicals Industry -- 3.4.4 Green Synthesis of Nanoparticles -- 3.5 Hurdles to Industry Implementation -- 3.5.1 Control, Monitoring and Modelling of SDR Processes -- 3.5.2 Limited Process Throughputs -- 3.5.3 Cost and Availability of Equipment -- 3.5.4 Lack of Awareness of SDR Technology -- 3.6 Conclusion -- Nomenclature -- Greek Letters -- Subscripts -- References -- 4 Micro Process Technology and Novel Process Windows - Three Intensification Fields -- 4.1 Introduction -- 4.2 Transport Intensification -- 4.2.1 Fundamentals -- 4.2.2 Mixing Principles -- 4.2.3 Micromixers -- 4.2.4 Micro Heat Exchangers -- 4.2.5 Exothermic Reactions as Major Application Examples -- 4.3 Chemical Intensification -- 4.3.1 Fundamentals -- 4.3.2 New Chemical Transformations -- 4.3.3 High Temperature -- 4.3.4 High Pressure -- 4.3.5 Alternative Reaction Media -- 4.4 Process Design Intensification -- 4.4.1 Fundamentals -- 4.4.2 Large-scale Manufacture of Adipic Acid - A Full Process Design Vision in Flow -- 4.4.3 Process Integration - From Single Operation towards Full Process Design -- 4.4.4 Process Simplification -- 4.5 Industrial Microreactor Process Development -- 4.5.1 Industrial Demonstration of Specialty/Pharma Chemistry Flow Processing -- 4.5.2 Industrial Demonstration of Fine Chemistry Flow Processing -- 4.5.3 Industrial Demonstration of Bulk Chemistry Flow Processing.
4.6 Conclusion -- Acknowledgement -- References -- 5 Green Chemistry in Oscillatory Baffled Reactors -- 5.1 Introduction -- 5.1.1 Continuous versus Batch Operation -- 5.1.2 The Oscillatory Baffled Reactor's 'Niche' -- 5.2 Case Studies: OBR Green Chemistry -- 5.2.1 A Saponification Reaction -- 5.2.2 A Three-phase Reaction with Photoactivation for Oxidation of Waste Water Contaminants -- 5.2.3 'Mesoscale' OBRs -- 5.3 Conclusion -- References -- 6 Monolith Reactors for Intensified Processing in Green Chemistry -- 6.1 Introduction -- 6.2 Design of Monolith Reactors -- 6.2.1 Monolith and Washcoat Design -- 6.2.2 Reactor and Distributor Design -- 6.3 Hydrodynamics of Monolith Reactors -- 6.3.1 Flow Regimes -- 6.3.2 Mixing and Mass Transfer -- 6.4 Advantages of Monolith Reactors -- 6.4.1 Scale-out, Not Scale-up? -- 6.4.2 PI for Green Chemistry -- 6.5 Applications in Green Chemistry -- 6.5.1 Chemical and Fine Chemical Industry -- 6.5.2 Cleaner Production of Fuels -- 6.5.3 Removal of Toxic Emissions -- 6.6 Conclusion -- Acknowledgement -- Nomenclature -- Greek Letters -- Subscripts and Superscripts -- References -- 7 Process Intensification and Green Processing Using Cavitational Reactors -- 7.1 Introduction -- 7.2 Mechanism of Cavitation-based PI of Chemical Processing -- 7.3 Reactor Configurations -- 7.3.1 Sonochemical Reactors -- 7.3.2 Hydrodynamic Cavitation Reactors -- 7.4 Mathematical Modelling -- 7.5 Optimization of Operating Parameters in Cavitational Reactors -- 7.5.1 Sonochemical Reactors -- 7.5.2 Hydrodynamic Cavitation Reactors -- 7.6 Intensification of Cavitational Activity -- 7.6.1 Use of PI Parameters -- 7.6.2 Use of a Combination of Cavitation and Other Processes -- 7.7 Case Studies: Intensification of Chemical Synthesis using Cavitation -- 7.7.1 Transesterification of Vegetable Oils Using Alcohol.
7.7.2 Selective Synthesis of Sulfoxides from Sulfides Using Sonochemical Reactors -- 7.8 Overview of Intensification and Green Processing Using Cavitational Reactors -- 7.9 The Future -- 7.10 Conclusion -- References -- 8 Membrane Bioreactors for Green Processing in a Sustainable Production System -- 8.1 Introduction -- 8.2 Membrane Bioreactors -- 8.2.1 Membrane Bioreactors with Biocatalyst Recycled in the Retentate Stream -- 8.2.2 Membrane Bioreactors with Biocatalyst Segregated in the Membrane Module Space -- 8.3 Biocatalytic Membrane Reactors -- 8.3.1 Entrapment -- 8.3.2 Gelification -- 8.3.3 Chemical Attachment -- 8.4 Case Studies: Membrane Bioreactors -- 8.4.1 Biofuel Production Using Enzymatic Transesterification -- 8.4.2 Waste Water Treatment and Reuse -- 8.4.3 Waste Valorization to Produce High-added-value Compounds -- 8.5 Green Processing Impact of Membrane Bioreactors -- 8.6 Conclusion -- References -- 9 Reactive Distillation Technology -- 9.1 Introduction -- 9.2 Principles of RD -- 9.3 Design, Control and Applications -- 9.4 Modelling RD -- 9.5 Feasibility and Technical Evaluation -- 9.5.1 Feasibility Evaluation -- 9.5.2 Technical Evaluation -- 9.6 Case Studies: RD -- 9.6.1 Biodiesel Production by Heat-Integrated RD -- 9.6.2 Fatty Esters Synthesis by Dual RD -- 9.7 Green Processing Impact of RD -- 9.8 Conclusion -- References -- 10 Reactive Extraction Technology -- 10.1 Introduction -- 10.1.1 Definition and Description -- 10.1.2 Literature Review -- 10.2 Case Studies: Reactive Extraction Technology -- 10.2.1 Reactive Extraction for the Synthesis of FAME from Jatropha curcas L. Seeds -- 10.2.2 Supercritical Reactive Extraction for FAME Synthesis from Jatropha curcas L. Seeds -- 10.3 Impact on Green Processing and Process Intensification -- 10.4 Conclusion -- Acknowledgement -- References -- 11 Reactive Absorption Technology.
11.1 Introduction -- 11.2 Theory and Models -- 11.2.1 Equilibrium Stage Model -- 11.2.2 HTU/NTU Concepts and Enhancement Factors -- 11.2.3 Rate-based Stage Model -- 11.3 Equipment, Operation and Control -- 11.4 Applications in Gas Purification -- 11.4.1 Carbon Dioxide Capture -- 11.4.2 Sour Gas Treatment -- 11.4.3 Removal of Nitrogen Oxides -- 11.4.4 Desulfurization -- 11.5 Applications to the Production of Chemicals -- 11.5.1 Sulfuric Acid Production -- 11.5.2 Nitric Acid Production -- 11.5.3 Biodiesel and Fatty Esters Synthesis -- 11.6 Green Processing Impact of RA -- 11.7 Challenges and Future Prospects -- References -- 12 Membrane Separations for Green Chemistry -- 12.1 Introduction -- 12.2 Membranes and Membrane Processes -- 12.3 Case Studies: Membrane Operations in Green Processes -- 12.3.1 Membrane Technology in Metal Ion Removal from Waste Water -- 12.3.2 Membrane Operations in Acid Separation from Waste Water -- 12.3.3 Membrane Operation for Hydrocarbon Separation from Waste Water -- 12.3.4 Membrane Operations for the Production of Optically Pure Enantiomers -- 12.4 Integrated Membrane Processes -- 12.4.1 Integrated Membrane Processes for Water Desalination -- 12.4.2 Integrated Membrane Processes for the Fruit Juice Industry -- 12.5 Green Processing Impact of Membrane Processes -- 12.6 Conclusion -- References -- 13 Process Intensification in a Business Context: General Considerations -- 13.1 Introduction -- 13.2 The Industrial Setting -- 13.3 Process Case Study -- 13.3.1 Essential Lessons -- 13.4 Business Risk and Ideas -- 13.5 Conclusion -- References -- 14 Process Economics and Environmental Impacts of Process Intensification in the Petrochemicals, Fine Chemicals and Pharmaceuticals Industries -- 14.1 Introduction -- 14.2 Petrochemicals Industry -- 14.2.1 Drivers for Innovation -- 14.2.2 Conventional Technologies Used.
14.2.3 Commercially Applied PI Technologies.
Abstract:
The successful implementation of greener chemical processes relies not only on the development of more efficient catalysts for synthetic chemistry but also, and as importantly, on the development of reactor and separation technologies which can deliver enhanced processing performance in a safe, cost-effective and energy efficient manner. Process intensification has emerged as a promising field which can effectively tackle the challenges of significant process enhancement, whilst also offering the potential to diminish the environmental impact presented by the chemical industry. Following an introduction to process intensification and the principles of green chemistry, this book presents a number of intensified technologies which have been researched and developed, including case studies to illustrate their application to green chemical processes. Topics covered include: Intensified reactor technologies: spinning disc reactors, microreactors, monolith reactors, oscillatory flow reactors, cavitational reactors Combined reactor/separator systems: membrane reactors, reactive distillation, reactive extraction, reactive absorption Membrane separations for green chemistry Industry relevance of process intensification, including economics and environmental impact, opportunities for energy saving, and practical considerations for industrial implementation. Process Intensification for Green Chemistry is a valuable resource for practising engineers and chemists alike who are interested in applying intensified reactor and/or separator systems in a range of industries to achieve green chemistry principles.
Local Note:
Electronic reproduction. Ann Arbor, Michigan : ProQuest Ebook Central, 2017. Available via World Wide Web. Access may be limited to ProQuest Ebook Central affiliated libraries.
Genre:
Added Author:
Electronic Access:
Click to View