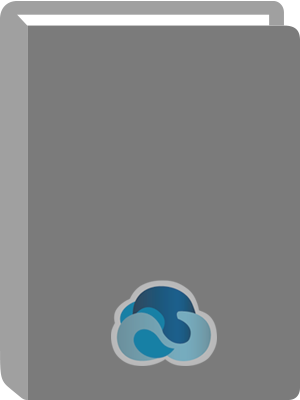
Tank Linings for Chemical Process Industries.
Title:
Tank Linings for Chemical Process Industries.
Author:
Chandrasekaran, Chellappa.
ISBN:
9781847351074
Personal Author:
Edition:
1st ed.
Physical Description:
1 online resource (176 pages)
Contents:
Cover -- Table of Contents -- Preface -- 1 Introduction -- 2 Rubber - An Overview -- 2.1 The Origins of Polymer Science -- 2.2 The Polymerisation Process -- 2.3 Developments in Synthetic Rubber -- 2.4 Vulcanisation -- 2.5 Range of Rubbers -- References -- 3 Rubber Lining for Corrosion Protection in the Chemical Industry -- 3.1 Types of Corrosion -- 3.1.1 Uniform Attack -- 3.1.2 Galvanic Corrosion -- 3.1.3 Crevice Corrosion -- 3.1.4 Pitting -- 3.1.5 Intergranular Corrosion -- 3.1.6 Selective Leaching -- 3.1.7 Erosion Corrosion -- 3.1.8 Stress Corrosion -- 3.2 The Fertiliser Industry -- 3.3 Power Plants -- 3.4 Treatment of Ores -- 3.5 The Chlor-Alkali Industry -- 3.6 Mercury Cells in the Caustic Soda Industry -- 3.6.1 Flexible Cell Covers in the Caustic Soda Industry -- 3.7 The Steel Industry -- 3.8 The Transport Industry -- 3.9 The Electroplating Industry -- 3.10 The Fluorine Industry -- 3.11 The Explosives Industry -- 3.12 The Pulp and Paper Industries -- 3.13 The Ore and Mining Industries -- References -- 4 Choice of Rubber Compounds for the Ore and Mining Industries -- 4.1 Conveyor Systems -- 4.2 Slurry Transportation -- 4.3 The Future of Hydraulic Transportation of Solids -- 4.4 Abrasion Resistance -- 4.4.1 Feed Launders for Hindustan Dorr-Oliver Ltd -- 4.4.2 Acid Handling Bins for Ceylon Mineral Sands Corporation, Sri Lanka -- 4.4.3 Regrinding Ball Mill in the Copper Project at Khetri in Rajasthan, India -- 4.4.4 Pipes, Launders and Chutes in an Iron Ore Mining Project -- 4.4.5 Rotary Vacuum Drum Filters -- 4.5 Spherical Digesters in a Chlor-alkali Plant -- 4.6 Dry Abrasive Conditions -- 4.7 Wet Abrasive Conditions -- References -- 5 Raw Materials for Rubber Lining -- 5.1 Natural Rubber -- 5.2 Synthetic Rubbers -- 5.2.1 Polyisoprene Rubber -- 5.2.2 Polybutadiene Rubber -- 5.2.3 Butyl Rubber -- 5.2.4 Ethylene Propylene Rubber.
5.2.5 Chloroprene Rubber -- 5.2.6 Chlorosulfonated Polyethylene Rubbers -- 5.2.7 Acrylonitrile Butadiene Rubbers -- 5.2.8 Styrene-Butadiene Rubbers -- 5.3 Vulcanising and Curing Agents -- 5.4 Materials for Reinforcement -- 5.4.1 Carbon Blacks -- 5.4.2 China Clay -- 5.4.3 Talc -- 5.4.4 Titanium Dioxide -- 5.4.5 Zinc Oxide -- 5.4.6 Lithopone -- 5.4.7 Litharge -- 5.4.8 Antimony Trioxide -- 5.4.9 Zinc Stearate -- 5.5 Plasticisers, Softeners and Extenders -- 5.5.1 Peptisers -- 5.5.2 Process Oils -- 5.5.3 Paraffin Wax -- 5.5.4 Resins -- 5.6 Antioxidants and Antiozonants -- 5.7 Adhesives and Bonding Agents -- 5.8 Solvents -- References -- 6 Elastomers Used in the Rubber Lining Industry -- 6.1 Neoprene Rubber -- 6.1.1 Compounding Neoprene for tank lining application -- 6.2 Hypalon Rubbers -- 6.2.1 Compounding Hypalon for tank lining -- 6.3 Butyl rubber -- 6.4 EPDM Rubber -- 6.5 Silicone Rubbers -- 6.6 Fluorocarbon Elastomers -- 6.7 Natural Rubber -- 6.8 Synthetic Ebonites -- Reference -- 7 Compounding Elastomers for Rubber Lining -- 7.1 Design of Compound formulations -- 7.1.1 Choice of Ingredients -- 7.1.2 Viscosity Control -- 7.1.3 Nerve Control -- 7.1.4 Sticking to Mill Rollers -- 7.1.5 Sheeting -- 7.1.6 Tack -- 7.1.7 Scorching -- 7.1.8 Hardness and Modulus -- 7.1.9 Elasticity -- 7.1.10 Strength -- 7.1.11 Resistance to Tear -- 7.1.12 Resistance to Flex-cracking and Fatigue -- 7.1.13 Resistance to Heat -- 7.1.14 Resistance to Flame -- 7.1.15 Resistance to Gas Permeation -- 7.1.16 Bonding -- 7.2 Processing Characteristics -- 7.2.1 Mastication -- 7.2.2 Mixing -- 7.2.3 Calendering -- 7.2.4 Prevulcanised Sheet Winding (PV Plant) -- 7.2.5 Extrusion -- 7.2.6 Moulding -- 7.3 Proportion -- 7.4 Silica and Carbon Filled Butyl Rubber Vulcanisates -- 7.5 Compounding Elastomers of Low Cure Functionality -- 7.6 Chemical Reaction of Polymers.
7.6.1 Resistance to Halogens -- 7.6.2 Resistance to Hydrogen Sulfide -- 7.6.3 Epoxidation by Hypochlorous acid -- 7.6.4 Hydrochlorination of Rubbers -- 7.6.5 Heat Evolution During Vulcanisation of Ebonites -- References -- 8 Manufacturing and Application Procedures -- 8.1 Rubber Lining -- 8.2 Role of Impurities -- 8.3 Working temperature -- 8.4 Lining Thickness -- 8.5 Design and Fabrication of Lining Supports -- 8.6 Adhesive Coating -- 8.7 Application of Calendered Sheet -- 8.8 Autoclave Vulcanisation -- 8.9 Inspection -- 8.10 Adhesive Manufacture -- 8.11 Rubber Lining of Large Storage Tanks -- 8.12 Sheet Dimensions -- 8.13 Sheet Laying and Rolling -- 8.14 Procedure of Tank Inspection before Undertaking the Lining Operation -- 8.15 Rubber Lining of Pipes -- 8.16 Storage of Rubber Lined Pipes -- 8.17 Surface Preparation for Rubber Lining -- 8.18 Methods of Surface Preparation -- References -- 9 Testing of Rubber Lining -- 9.1 Density of Solids -- 9.2 Hardness -- 9.3 Spark Testing -- 9.4 Description of Apparatus -- 9.5 Swelling Test -- 9.6 Specifications and Codes of Practice -- References -- 10 Specification and Codes of Practice for Rubber Lining -- References -- Useful Websites -- Abbreviations -- Appendix 1: Swelling of chloroprene rubber (CR) in various solvents -- Appendix 2: Greek alphabet used to denote engineering quantities of materials -- Appendix 3: Chemical resistant properties and hardness ranges of both natural and synthetic rubbers -- Appendix 4: Useful data for calculating dimension of a steel tank and weight of rubber lining -- Appendix 5: Area of circle -- Appendix 6: Circumference of circle -- Appendix 7: Conversion of square feet to square metres -- Appendix 8: Calculation of the area of different geometric shapes -- Index.
Abstract:
Rubber linings can be used as passive protection against the corrosion of plant and equipment in the chemical process industries. Rubbers act as sacrificial materials reacting or un-reacting with the corrosive media, diffusing the liquids or not diffusing, swelling by itself or not swelling, permeating or not permeating gases or fumes, abrading or wearing by the slurry particles, getting ozonised or oxidised; but still protecting the metal surface beneath it, during its considerable life cycle under those severe and stressed conditions. Rubbers age but their life cycle is good enough to protect the metals against corrosion and erosion. The raw material bases are natural or synthetic rubbers. Rubber is used for corrosion/abrasion proof linings, more than any other material because of its proven superiority in this service at a relatively low cost. Fertilizer, electroplating, ore-refining, petrochemicals, chlor-alkali and paper industries invariably turn to rubber linings, in preference to other types of linings for their high resistance to corrosion and abrasion. Moreover the variety of rubbers, both natural and man-made, available and its flexibility to serve under wide temperature and pressure ranges, made rubber linings as the world-wide accepted anti-corrosive and anti-abrasive media. This book describes exactly how to use rubber as a lining in tanks and how to overcome problems associated with this technique.
Local Note:
Electronic reproduction. Ann Arbor, Michigan : ProQuest Ebook Central, 2017. Available via World Wide Web. Access may be limited to ProQuest Ebook Central affiliated libraries.
Genre:
Electronic Access:
Click to View