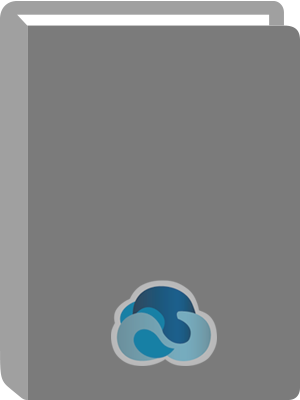
Design for Manufacturing : A Structured Approach.
Title:
Design for Manufacturing : A Structured Approach.
Author:
Poli, Corrado.
ISBN:
9780080503943
Personal Author:
Physical Description:
1 online resource (409 pages)
Contents:
Front Cover -- Design for Manufacturing: A Structured Approach -- Copyright Page -- Contents -- List of Figures -- List of Tables -- Preface -- Acknowledgments -- Responsibilities of Users -- Chapter 1. Introduction -- 1.1 Manufacturing, Design, and Design for Manufacturing -- 1.2 Functional Designed Objects -- 1.3 The Product Realization Process -- 1.4 Industrial (or Product) Design -- 1.5 Engineering Design -- 1.6 Production Design -- 1.7 Scope of the Book -- 1.8 Summary -- References -- Questions and Problems -- Chapter 2. Tolerances, Mechanical Properties, Physical Properties-A Review -- 2.1 Interchangeability of Parts -- 2.2 Tolerances -- 2.3 Mechanical and Physical Properties -- 2.4 Physical Properties of Materials -- 2.5 Summary -- References -- Questions and Problems -- Chapter 3. Polymer Processing -- 3.1 The Processes -- 3.2 Materials Used in Polymer Processing -- 3.3 Injection Molding -- 3.4 Compression Molding -- 3.5 Transfer Molding -- 3.6 Extrusion -- 3.7 Extrusion Blow Molding -- 3.8 Other Polymer Processes -- 3.9 Qualitative DFM Guidelines for Injection Molding, Compression Molding, and Transfer Molding -- 3.10 Summary -- References -- Questions and Problems -- Chapter 4. Injection Molding: Relative Tooling Cost -- 4.1 Introduction -- 4.2 Estimating Relative Tooling Costs for Injection-Molded Parts -- 4.3 Determining Relative Tooling Construction Costs Due to Basic Part Complexity (Cb) -- 4.4 Determining Cs -- 4.5 Determining Ct -- 4.6 Using the Part Coding System to Determine Cb, Cs, and Ct -- 4.7 Total Relative Tooling Construction Cost -- 4.8 Relative Mold Material Cost -- 4.9 Multiple Cavity Molds -- 4.10 Example 1-Relative Tooling Cost for a Simple Part -- 4.11 Example 2-Relative Tooling Cost for a Complex Part -- 4.12 Worksheet for Relative Tooling Cost -- 4.13 Summary -- References -- Questions and Problems.
Appendix 4.A Notes for Figures 4.1 and 4.19, and Tables 4.1 and 4.2 -- Appendix 4.B Worksheet for Relative Tooling Costs- Injection Molding -- Chapter 5. Injection Molding: Total Relative Part Cost -- 5.1 Injection Molded Part Costs -- 5.2 Determining Total Relative Cycle Time (tr) for Injection-Molded Parts-Overview -- 5.3 Determining the Basic Part Type: The First Digit -- 5.4 Partitioning Partitionable Parts -- 5.5 Non-Partitionable Parts -- 5.6 Other Features Needed to Determine the First Digit -- 5.7 Wall Thickness-The Second Digit -- 5.8 Inserts and Internal Threadsn-The Third Digit -- 5.9 Surface Requirements and TolerancesmThe Fourth and Fifth Digits -- 5.10 Using the Coding System--Overview -- 5.11 Effect of Materials on Relative Cycle Time -- 5.12 Example 5.1-Determination of Relative Cycle Time for a Partitionable Part -- 5.13 Example 5.2-Determination of Relative Cycle Time for a Partitionable Part -- 5.14 Example 5.3-Determination of Relative Cycle Time for a Non-Partitionable Part -- 5.15 Relative Processing Cost -- 5.16 Relative Material Cost -- 5.17 Total Relative Part Cost -- 5.18 Example 5.4--Determination of the Total Relative Part Cost -- 5.19 Worksheet for Relative Processing Cost and Total Relative Part Cost -- 5.20 Summary -- References -- Questions and Problems -- Appendix 5.A Notes for Figure 5.2 and Tables 5.3 and 5.4 -- Appendix 5.B Worksheet for Relative Processing Cost and Total Relative Cost -- Chapter 6. Metal Casting Processes -- 6.1 Introduction -- 6.2 Sand Casting -- 6.3 Investment Casting -- 6.4 Die Casting -- 6.5 Other Casting Processes -- 6.6 Qualitative DFM Guidelines for Casting -- 6.7 Summary -- References -- Questions and Problems -- Chapter 7. Die Casting: Total Relative Part Cost -- 7.1 Die Cast Part Costs-Overview -- 7.2 Relative Tooling Cost -- 7.3 Example 7.1-Relative Tooling Cost for a Die-Cast Part.
7.4 Worksheet for Relative Tooling Cost -- 7.5 Processing Costs-Overview -- 7.6 Production Yield and Effective Cycle Time -- 7.7 Surface Finish -- 7.8 Part Tolerances -- 7.9 Example 7.2-Determination of Relative Cycle Time for a Partitionable Part -- 7.10 Total Relative Part Cost -- 7.11 Example 7.3-Determination of the Total Relative Part Cost -- 7.12 Worksheet for Relative Processing Cost and Total Relative Part Cost -- 7.13 Summary -- References -- Questions and Problems -- Chapter 8. Sheet-Metal Forming -- 8.1 Introduction -- 8.2 The Stamping Process -- 8.3 Stretch Forming -- 8.4 Spinning -- 8.5 Stamping Dies -- 8.6 Stamping Presses -- 8.7 Process Planning -- 8.8 Design for Manufacturing Guidelines for Stamped Parts -- 8.9 Summary -- References -- Questions and Problems -- Chapter 9. Stamping: Relative Tooling Cost -- 9.1 Introduction -- 9.2 Estimating the Relative Cost of Stamped Parts -- 9.3 Die Construction Costs -- 9.4 Determination of the Number of Active Stations for Shearing and Local Features -- 9.5 Example l-Number of Active Stations for a Flat Part -- 9.6 Determination of the Number of Active Stations for Wipe Forming and Side-Action Features -- 9.7 The Number of Bend Stages -- 9.8 Example 2-Number of Active Stations for A Bent Part -- 9.9 Relative Die Construction Costs -- 9.10 Example 3-Relative Die Construction Cost for a Flat Part -- 9.11 Example 4-Relative Die Construction Cost for a Bent Part -- 9.12 Effects of Part Material and Sheet Thickness on Die Construction Costs -- 9.13 Relative Die Material Cost for Progressive Dies -- 9.14 Example 5-Relative Tooling Cost -- 9.15 Example 6-Relative Tooling Cost -- 9.16 Worksheet for Relative Tooling Cost-Stamping -- 9.17 Summary -- References -- Questions and Problems -- Chapter 10. Stamping: Total Relative Part Cost -- 10.1 Introduction -- 10.2 Relative Processing Cost, CE.
10.3 Determining Press Tonnage, Fp -- 10.4 Press Selection -- 10.5 Determining the Relative Cycle Time -- 10.6 Example l-Relative Processing Cost for a Part -- 10.7 Example 2-Relative Processing Cost for a Part -- 10.8 Relative Material Cost -- 10.9 Total Relative Part Cost -- 10.10 Example 3-Total Relative Part Cost for a Part -- 10.11 Worksheet for Relative Processing Costm-Stamping -- 10.12 Summary -- References -- Questions and Problems -- Chapter 11. Other Metal Shaping Processes -- 11.1 Introduction -- 11.2 Metals and Processes -- 11.3 Forging -- 11.4 Aluminum Extrusion -- 11.5 Machining -- 11.6 Summary -- References -- Questions and Problems -- Chapter 12. Assembly -- 12.1 Assembly Processes -- 12.2 Qualitative Guidelines on Design for Assembly (DFA) -- 12.3 Total Assembly Cost -- 12.4 Summary of DFA Guidelines -- 12.5 Reducing Part Count by Combining Several Parts into One -- 12.6 Summary -- References -- Questions and Problems -- Chapter 13. Selecting Materials and Processes for Special Purpose Parts -- 13.1 Introduction -- 13.2 Two Approaches-A Brief Overview -- 13.3 A Hierarchical Organization of Material Alternatives Tables 13.1 to 13.4 -- 13.4 Application Issues in Selecting Materials -- 13.5 Cost -- 13.6 Part Information in Selecting Processes-Tables 13.5 to 13.7 -- 13.7 Examples -- 13.8 Injection Molding versus Die Casting -- 13.9 Injection Molding versus Stamping -- 13.10 Summary -- References -- Questions and Problems -- Appendix 13.A Some Properties of Selected Materials -- Chapter 14. Communications -- 14.1 Introduction -- 14.2 Written Communications -- 14.3 Research Reports -- 14.4 Business Technical Reports -- 14.5 Hybrid Technical Reports -- 14.6 Oral Reports -- 14.7 Graphical Communications -- 14.8 Summary -- References -- Questions and Problems -- Nomenclature -- Index -- About the CD-ROM.
Abstract:
Design for Manufacturing assists anyone not familiar with various manufacturing processes in better visualizing and understanding the relationship between part design and the ease or difficulty of producing the part. Decisions made during the early conceptual stages of design have a great effect on subsequent stages. In fact, quite often more than 70% of the manufacturing cost of a product is determined at this conceptual stage, yet manufacturing is not involved. Through this book, designers will gain insight that will allow them to assess the impact of their proposed design on manufacturing difficulty. The vast majority of components found in commercial batch-manufactured products, such as appliances, computers and office automation equipment are either injection molded, stamped, die cast, or (occasionally) forged. This book emphasizes these particular, most commonly implemented processes. In addition to chapters on these processes, the book touches upon material process selection, general guidelines for determining whether several components should be combined into a single component or not, communications, the physical and mechanical properties of materials, tolerances, and inspection and quality control. In developing the DFM methods presented in this book, he has worked with over 30 firms specializing in injection molding, die-casting, forging and stamping. A set of Power Point slides, containing animations of the various processes, drawings, and photographs of various parts are included. There is also a specially developed website, featuring specific tutorials on each process and its practical applications. Implements a philosophy which allows for easier and more economic production of designs Educates designers about manufacturing Emphasizes the four major manufacturing processes.
Local Note:
Electronic reproduction. Ann Arbor, Michigan : ProQuest Ebook Central, 2017. Available via World Wide Web. Access may be limited to ProQuest Ebook Central affiliated libraries.
Genre:
Electronic Access:
Click to View