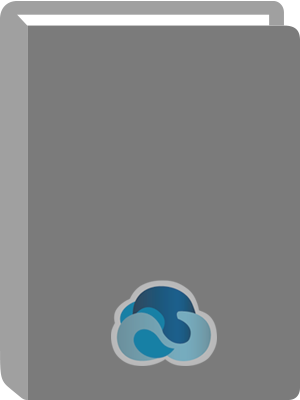
Automotive Body Manufacturing Systems and Processes.
Title:
Automotive Body Manufacturing Systems and Processes.
Author:
Omar, Mohammed A.
ISBN:
9780470978474
Personal Author:
Edition:
1st ed.
Physical Description:
1 online resource (394 pages)
Contents:
THE AUTOMOTIVE BODY MANUFACTURING SYSTEMS AND PROCESSES -- Contents -- Preface -- Foreword -- Acknowledgments -- Abbreviations -- 1: Introduction -- 1.1 Anatomy of a Vehicle, Vehicle Functionality and Components -- 1.2 Vehicle Manufacturing: An Overview -- 1.2.1 Basics of the Assembly Processes -- 1.2.2 Basics of the Power-train Processes -- 1.3 Conclusion -- Exercises -- 2: Stamping and Metal Forming Processes -- 2.1 Formability Science of Automotive Sheet Panels: An Overview -- 2.1.1 Stamping Modes and Metal Flow -- 2.1.2 Material Properties and their Formability -- 2.1.3 Formability Measures -- 2.1.4 Circle Grid Analysis (CGA) and the Forming Limit Diagram (FLD) -- 2.2 Automotive Materials -- 2.2.1 Automotive Steel Grades -- Traditional Steel Grades -- 2.2.2 Automotive Steel Grades: High Strength and Advanced (Ultra) -- 2.2.3 Stamping Aluminum Sheet Panels -- 2.3 Automotive Stamping Presses and Dies -- 2.3.1 Automotive Dies -- 2.3.2 Die Operation and Tooling -- 2.3.2.1 The Blank Holder -- 2.3.2.2 Draw Beads -- 2.3.2.3 Blanking and Shearing Dies -- 2.3.2.4 Bending -- 2.3.2.5 Deep Drawing -- 2.3.2.6 Coatings and Lubrications -- 2.4 Tailor Welded Blanks and their Stamping -- 2.5 Advances in Metal Forming -- 2.5.1 Hydro-forming and Extrusions -- 2.5.2 Industrial Origami: Metal Folding-Based Forming -- 2.5.3 Super-plastic Forming -- 2.5.4 Flexible Stamping Procedures -- 2.6 Stampings Dimensional Approval Process -- 2.7 Stamping Process Costing -- 2.7.1 Case I: The Stamping Process -- 2.7.1.1 Detailed Cost Analysis -- 2.7.2 Case II : Tailor-Welded Door Inner Cost -- Exercises -- 3: Automotive Joining -- 3.1 Introduction -- 3.2 Fusion Welding Operations -- 3.2.1 Basics of Arc Fusion Welding and its Types -- 3.2.2 Metal Inert Gas MIG Welding Processes -- 3.2.3 Automotive TIG Welding Processes -- 3.2.4 Automotive Resistance Welding Processes.
3.2.4.1 Surface Conditions and Their Effect on Resistance Welding -- 3.2.4.2 Basics of Spot Welding, Lobes and Resistance Curves -- 3.3 Robotic Fusion-Welding Operations -- 3.3.1 Robotic Spot Welders -- 3.4 Adhesive Bonding -- 3.4.1 Basics of Adhesive Material Selection -- 3.4.2 Basics of the Adhesion Theory and Adhesives Testing -- 3.5 Welding and Dimensional Conformance -- 3.6 Advances in Automotive Welding -- 3.6.1 Friction Stir Welding (FSW) -- 3.6.2 Laser Welding -- 3.6.3 Weld Bonding -- 3.7 The Automotive Joining Costing -- 3.7.1 Joining an Automotive Frame -- 3.7.2 Sub-assembling Automotive Doors -- Exercises -- 4: Automotive Painting -- 4.1 Introduction -- 4.2 Immersion Coating Processes -- 4.2.1 Cleaning -- 4.2.2 Rinsing -- 4.2.3 Conversion and Phosphate Baths -- 4.2.3.1 Phosphating Aluminum -- 4.2.4 E-Coating Baths and their Operations -- 4.3 Paint Curing Processes, and Balancing -- 4.4 Under-Body Sealant, PVC and Wax Applications -- 4.5 Painting Spray Booths Operations -- 4.5.1 Spray Paint Applicators -- 4.5.2 Painting Booth Conditioning, Waterborne, Solvent-borne and Powder-coating Systems -- 4.5.2.1 Waterborne Paint -- 4.5.2.2 Powder Coating -- 4.5.3 Paint Calculations -- 4.6 Material Handling Systems Inside the Painting Area -- 4.7 Painting Robotics -- 4.8 Paint Quality Measurements -- 4.8.1 Paint Defects and Theory -- 4.8.1.1 Theoretical Background -- Exercises -- 5: Final Assembly -- 5.1 Basics of Final Assembly Operations -- 5.1.1 Installation of the Trim Assembly -- 5.1.2 Installation of the Chassis -- 5.1.3 Final Assembly and Testing Area -- 5.2 Ergonomics of the Final Assembly Area -- 5.3 Mechanical Fastening and Bolting -- Exercises -- 6: Ecology of Automotive Manufacturing -- 6.1 Introduction of Automotive Manufacturing Ecology -- 6.2 Energy Consumption and Accounting -- 6.2.1 The EPA Energy Model.
6.2.2 Specific Energy Requirements from the EPI Model -- 6.2.3 Panel-Forming Energy -- 6.2.4 Hybridized Structures Selection and Energy Implications -- 6.2.5 Proposed Approach versus Previous Models -- 6.2.6 Conclusion and Comments on Specific Energy Modeling -- 6.3 The Automotive Materials' Ecological Impact -- 6.4 The Painting Process Ecology -- 6.5 Ecology of the Automobile -- 7: Static Aspects of the Automotive Manufacturing Processes -- 7.1 Introduction -- 7.2 Layout Strategies -- 7.3 Process-oriented Layout -- 7.4 Cell-based Layout Design -- 7.5 Product-based Layout -- 7.6 Lean Manufacturing Tools for Layout Design and Optimization -- 7.7 Locational Strategies -- 7.7.1 Locational Strategies Tools -- Exercises -- 8: Operational Aspects of the Automotive Manufacturing Processes -- 8.1 Introduction -- 8.2 Aggregate Production Planning -- 8.3 Master Production Scheduling (MPS) -- 8.4 Material Requirement Planning (MRP) -- 8.5 Production Line Control and Management Style -- 8.5.1 Lean Manufacturing Management of Workers -- 8.6 Selection and Management of Suppliers -- 8.6.1 Selection and Management Process -- 8.7 An Overview of the Automotive Quality Tools -- 8.7.1 The Production Part Approval Process (PPAP) -- 8.7.2 The Advanced Product Quality Planning (APQP) -- 8.7.3 The Failure Mode and Effect Analysis (FMEA) -- Exercises -- References -- INDEX.
Abstract:
The Automotive Body Manufacturing Systems and Processes Mohammed A. Omar, Clemson University International Centre for Automotive Research CU-ICAR, USA A comprehensive and dedicated guide to automotive production lines, The Automotive Body Manufacturing Systems and Processes addresses automotive body processes from the stamping operations through the final assembly activities. To begin, it discusses current metal forming practices, including stamping engineering, die development, and dimensional validation, and new innovations in metal forming, such as folding based forming, super-plastic, and hydro forming technologies. The first section also explains details of automotive spot welding (welding lobes), arc welding, and adhesive bonding, in addition to flexible fixturing systems and welding robotic cells. Guiding readers through each stage in the process of automotive painting, including the calculations needed to compute the number of applicators and paint consumption based on vehicle dimensions and demand, along with the final assembly and automotive mechanical fastening strategies, the book's systematic coverage is unique. The second module of the book focuses on the layout strategies of the automotive production line. A discussion of automotive aggregate planning and master production scheduling ensures that the reader is familiar with operational aspects. The book also reviews the energy emissions and expenditures of automotive production processes and proposes new technical solutions to reduce environmental impact. Provides extensive technical coverage of automotive production processes, discussing flexible stamping, welding and painting lines Gives complete information on automotive production costing as well as the supplier selection process Covers systems from the operational perspective, describing the aggregate and master
production planning Details technical aspects of flexible automotive manufacturing lines Methodically discusses the layout and location strategies of automotive manufacturing systems to encompass the structural elements Features topic-related questions with answers on a companion website.
Local Note:
Electronic reproduction. Ann Arbor, Michigan : ProQuest Ebook Central, 2017. Available via World Wide Web. Access may be limited to ProQuest Ebook Central affiliated libraries.
Genre:
Electronic Access:
Click to View