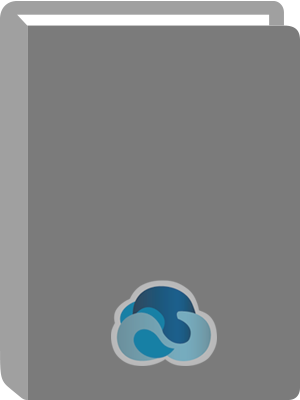
COST ANALYSIS OF ELECTRONIC SYSTEMS.
Title:
COST ANALYSIS OF ELECTRONIC SYSTEMS.
Author:
Sandborn, Peter.
ISBN:
9789814383356
Personal Author:
Physical Description:
1 online resource (440 pages)
Series:
WSPC SERIES IN ADVANCED INTEGRATION AND PACKAGING ; v.1
WSPC SERIES IN ADVANCED INTEGRATION AND PACKAGING
Contents:
CONTENTS -- Preface -- Chapter 1 Introduction -- 1.1 Cost Modeling -- 1.2 The Product Life Cycle -- 1.3 Life-Cycle Cost Scope -- 1.4 Cost Modeling Definitions -- 1.5 Cost Modeling for Electronic Systems -- 1.6 The Organization of this Book -- References -- Part I Manufacturing Cost Modeling -- I.1 Classification of Products Based on Manufacturing Cost -- I.2 Technical Cost Modeling (TCM) -- References -- Chapter 2 Process-Flow Analysis -- 2.1 Process Steps and Process Flows -- 2.1.1 Process-step sequence -- 2.1.2 Process-step inputs and outputs -- 2.2 Process-Step Calculations -- 2.2.1 Labor costs -- 2.2.2 Materials costs -- 2.2.3 Tooling costs -- 2.2.4 Equipment/Capital costs -- 2.2.5 Total cost -- 2.2.6 Capacity -- 2.3 Process-Flow Examples -- 2.3.1 Simple pick & place and reflow process -- 2.3.2 Multi-step process-flow example -- 2.4 Comments -- References -- Problems -- Chapter 3 Yield -- 3.1 Defects -- 3.2 Yield Prediction -- 3.2.1 The Poisson approximation to the binomial distribution -- 3.2.2 The Poisson yieldmodel -- 3.2.3 The Murphy yield model -- 3.2.4 Other yield models -- 3.3 Accumulated Yield -- 3.3.1 Multi-step process-flow example -- 3.3.2 The known good die (KGD) problem -- 3.4 Yielded Cost -- 3.5 The Relationship between Yield and Producibility -- References -- Bibliography -- Problems -- Chapter 4 Equipment/Facilities Cost of Ownership (COO) -- 4.1 The Cost of Ownership Algorithm -- 4.2 Cost of Ownership Modeling -- 4.2.1 Capital costs -- 4.2.2 Sustainment costs -- 4.2.3 Performance costs -- 4.3 Using COO to Compare Two Machines -- 4.4 Estimating Product Costs -- References -- Bibliography -- Problems -- Chapter 5 Activity-Based Costing (ABC) -- 5.1 The Activity-Based Cost Modeling Concept -- 5.1.1 Applicability of ABC to cost modeling -- 5.2 Formulation of Activity-Based Cost Models -- 5.2.1 Traditional cost accounting (TCA).
5.2.2 Activity-based costing -- 5.3 Activity-Based Cost Model Example -- 5.4 Summary and Discussion -- References -- Bibliography -- Problems -- Chapter 6 Parametric Cost Modeling -- 6.1 Cost Estimating Relationships (CERs) -- 6.1.1 Developing CERs -- 6.2 A Simple Parametric Cost Modeling Example -- 6.3 Limitations of CERs -- 6.3.1 Bounds of the data -- 6.3.2 Scope of the data -- 6.3.3 Overfitting -- 6.3.4 Don't force a correlation when one does not exist -- 6.3.5 Historical data -- 6.4 Other Parametric Cost Modeling/Estimation Approaches -- 6.4.1 Feature-based costing (FBC) -- 6.4.2 Neural network based cost estimation -- 6.4.3 Costing by analogy -- 6.5 Summary and Discussion -- References -- Bibliography -- Problems -- Chapter 7 Test Economics -- 7.1 Defects and Faults -- 7.1.1 Relating defects to faults -- 7.2 Defect and Fault Coverage -- 7.3 Relating Fault Coverage to Yield -- 7.3.1 A tempting (but incorrect) derivation of outgoing yield -- 7.3.2 A correct interpretation of fault coverage -- 7.3.3 A derivation of outgoing yield (Yout ) -- 7.3.4 An alternative outgoing yield formulation -- 7.4 A Test Step Process Model -- 7.4.1 Test escapes -- 7.4.2 Defects introduced by test steps -- 7.5 False Positives -- 7.5.1 A test step with false positives -- 7.5.2 Yield of the bonepile -- 7.6 Multiple Test Steps -- 7.6.1 Cascading test steps -- 7.6.2 Parallel test steps -- 7.7 Financial Models of Testing -- 7.8 Other Test-Related Economic Topics -- 7.8.1 Wafer probe (wafer sort) -- 7.8.2 Test throughput -- 7.8.3 Design for test (DFT) -- 7.8.4 Automated test equipment costs -- References -- Bibliography -- Problems -- Chapter 8 Diagnosis and Rework -- 8.1 Diagnosis -- 8.2 Rework -- 8.3 Test/Diagnosis/Rework Modeling -- 8.3.1 Single-pass rework example -- 8.3.2 A general multi-pass rework model -- 8.3.3 Variable rework cost and yield models.
8.3.4 Example test/diagnosis/rework analysis -- 8.4 Rework Cost (Crework fixed) -- References -- Problems -- Chapter 9 Uncertainty Modeling - Monte Carlo Analysis -- Uncertainty Modeling -- 9.1 Representing the Uncertainty in Parameters -- 9.2 Monte Carlo Analysis -- 9.2.1 How does Monte Carlo work? -- 9.2.2 Random sampling values from known distributions -- 9.2.3 Triangular distribution derivation -- 9.2.4 Random sampling from a data set -- 9.2.5 Implementation challenges with Monte Carlo analysis -- 9.3 Sample Size -- 9.4 Example Monte Carlo Analysis -- 9.5 Stratified Sampling (Latin Hypercube) -- 9.5.1 Building a latin hypercube sample (LHS) -- 9.5.2 Comments on LHS -- 9.6 Discussion -- References -- Bibliography -- Problems -- Chapter 10 Learning Curves -- 10.1 Mathematical Models for Learning Curves -- 10.2 Unit Learning Curve Model -- 10.3 Cumulative Average Learning Curve Model -- 10.4 Marginal Learning Curve Model -- 10.5 Learning Curve Mathematics -- 10.5.1 Unit learning data from cumulative average learning curves -- 10.5.2 The slide property of learning curves -- 10.5.3 The relationship between the learning index and the learning rate -- 10.5.4 The midpoint formula -- 10.5.5 Comparing learning curves -- 10.6 Determining Learning Curves from Actual Data -- 10.6.1 Simple data -- 10.6.2 Block data -- 10.7 Learning Curves for Yield -- 10.7.1 Gruber's learning curve for yield -- 10.7.2 Hilberg's learning curve for yield -- 10.7.3 Defect density learning -- References -- Bibliography -- Problems -- Part II Life-Cycle Cost Modeling -- II.1 System Sustainment -- II.2 Cost Avoidance -- II.3 Logistics -- References -- Chapter 11 Reliability -- 11.1 Product Failure -- 11.2 Reliability Basics -- 11.2.1 Failure distributions -- 11.2.2 Exponential distribution -- 11.2.3 Weibull distribution -- 11.3 Qualification and Certification.
11.4 Cost of Reliability -- References -- Bibliography -- Problems -- Chapter 12 Sparing -- Challenges with Spares -- 12.1 Calculating the Number of Spares -- 12.1.1 Multi-unit spares for repairable items -- 12.1.2 Sparing for a kit of repairable items -- 12.1.3 Sparing for large k -- 12.2 The Cost of Spares -- 12.2.1 Spares cost example -- 12.2.2 Extensions of the cost model -- 12.3 Summary and Comments -- References -- Bibliography -- Problems -- Chapter 13 Warranty Cost Analysis -- How warranties impact cost -- 13.1 Types of Warranties -- 13.2 Renewal Functions -- 13.2.1 The renewal function for constant failure rate -- 13.2.2 Asymptotic approximation of M(t) -- 13.3 Simple Warranty Cost Models -- 13.3.1 Ordinary (non-renewing) free-replacement warranty cost model -- 13.3.2 Pro-rata warranty cost Model -- 13.3.3 Investment of the warranty reserve fund -- 13.3.4 Other warranty reserve fund estimation models -- 13.4 Two-Dimensional Warranties -- 13.5 Warranty Service Costs - Real Systems -- References -- Problems -- Chapter 14 Burn-In Cost Modeling -- The Cost Tradeoffs Associated with Burn-in -- 14.1 Burn-In Cost Model -- 14.1.1 Cost of performing the burn-in -- 14.1.2 The value of burn-in -- 14.2 Example Burn-In Cost Analysis -- 14.3 Effective Manufacturing Cost of Units That Survive Burn-In -- 14.4 Burn-In for Repairable Units -- 14.5 Discussion -- References -- Bibliography -- Problems -- Chapter 15 Availability -- 15.1 Availability Contracting -- 15.1.1 Product service systems (PSS) -- 15.2 Availability Measures -- 15.2.1 Time-interval-based availability measures -- 15.2.2 Downtime-based availability measures -- 15.2.3 Application-specific availability measures -- 15.3 Maintainability and Maintenance Time -- 15.4 Monte Carlo Availability Calculation Example -- 15.5 Relating Availability to Spares -- 15.5.1 Backorders and supply availability.
15.5.2 Erlang-B -- 15.6 Markov Availability Models -- 15.7 Readiness -- 15.8 Discussion -- References -- Problems -- Chapter 16 The Cost Ramifications of Obsolescence -- Electronic part obsolescence -- 16.1 Managing Electronic Part Obsolescence -- 16.2 Lifetime Buy Costs -- 16.2.1 The newsvendor problem -- 16.2.2 Application of the newsvendor optimization problem to electronic parts -- 16.3 Strategic Management of Obsolescence -- 16.3.1 Porter design refresh model -- 16.3.2 MOCA design refresh model -- 16.3.3 Material risk index (MRI) -- 16.4 Discussion -- 16.4.1 Budgeting/bidding support -- 16.4.2 Value of DMSMS management -- 16.4.3 Software obsolescence -- References -- Problems -- Chapter 17 Return on Investment (ROI) -- 17.1 Definition of ROI1 -- 17.2 Cost Savings ROIs -- 17.2.1 ROI of a manufacturing equipment replacement -- 17.2.2 Technology adoption ROI -- 17.3 Cost Avoidance ROI -- 17.4 Stochastic ROI Calculations -- 17.5 Summary -- References -- Problems -- Chapter 18 The Cost of Service X. X. Huang, M. Kreye, G. Parry, Y. M. Goh and L. B. Newnes -- 18.1 Why Estimate the Cost of a Service? -- 18.2 An Engineering Service Example -- 18.3 How to Estimate the Cost of an Engineering Service -- 18.4 Application of the Service Costing Approach within an Industrial Company -- 18.5 Bidding for the Service Contract -- References -- Problems -- Chapter 19 Software Development and Support Costs -- Definitions -- 19.1 Software Development Costs -- 19.1.1 The COCOMO model -- 19.1.2 Function-point analysis -- 19.1.3 Object-point analysis -- 19.2 Software Support Costs -- 19.3 Discussion -- References -- Bibliography -- Problems -- Chapter 20 Total Cost of Ownership Examples -- 20.1 The Total Cost of Ownership of Color Printers -- 20.2 Total Cost of Ownership for Electronic Parts -- 20.2.1 Part total cost of ownership model -- 20.2.2 Example analyses.
References.
Abstract:
Understanding the cost ramifications of design, manufacturing and life-cycle management decisions is of central importance to businesses associated with all types of electronic systems. Cost Analysis of Electronic Systems contains carefully developed models and theory that practicing engineers can directly apply to the modeling of costs for real products and systems. In addition, this book brings to light and models many contributions to life-cycle costs that practitioners are aware of but never had the tools or techniques to address quantitatively in the past.Cost Analysis of Electronic Systems melds elements of traditional engineering economics with manufacturing process and life-cycle cost management concepts to form a practical foundation for predicting the cost of electronic products and systems. Various manufacturing cost analysis methods are addressed including: process-flow, parametric, cost of ownership, and activity-based costing. The effects of learning curves, data uncertainty, test and rework processes, and defects are considered. Aspects of system sustainment and life-cycle cost modeling including reliability (warranty, burn-in), maintenance (sparing and availability), and obsolescence are treated. Finally, total cost of ownership of systems and return on investment are addressed.Real life design scenarios from integrated circuit fabrication, electronic systems assembly, substrate fabrication, and electronic systems managementare used as examples of the application of the cost estimation methods developed within the book.
Local Note:
Electronic reproduction. Ann Arbor, Michigan : ProQuest Ebook Central, 2017. Available via World Wide Web. Access may be limited to ProQuest Ebook Central affiliated libraries.
Genre:
Electronic Access:
Click to View