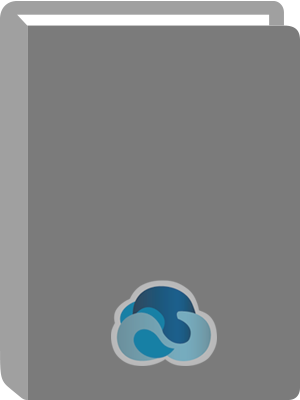
Critical Component Wear in Heavy Duty Engines.
Title:
Critical Component Wear in Heavy Duty Engines.
Author:
Lakshminarayanan, P. A.
ISBN:
9780470828830
Personal Author:
Edition:
1st ed.
Physical Description:
1 online resource (448 pages)
Contents:
CRITICAL COMPONENT WEAR IN HEAVY DUTY ENGINES -- Contents -- List of Contributors -- Preface -- Acknowledgements -- PART I: OVERTURE -- 1 Wear in the Heavy Duty Engine -- 1.1 Introduction -- 1.2 Engine Life -- 1.3 Wear in Engines -- 1.3.1 Natural Aging -- 1.4 General Wear Model -- 1.5 Wear of Engine Bearings -- 1.6 Wear of Piston Rings and Liners -- 1.7 Wear of Valves and Valve Guides -- 1.8 Reduction in Wear Life of Critical Parts Due to Contaminants in Oil -- 1.8.1 Oil Analysis -- 1.9 Oils for New Generation Engines with Longer Drain Intervals -- 1.9.1 Engine Oil Developments and Trends -- 1.9.2 Shift in Engine Oil Technology -- 1.10 Filters -- 1.10.1 Air Filter -- 1.10.2 Oil Filter -- 1.10.3 Water Filter -- 1.10.4 Fuel Filter -- 1.11 Types of Wear of Critical Parts in a Highly Loaded Diesel Engine -- 1.11.1 Adhesive Wear -- 1.11.2 Abrasive Wear -- 1.11.3 Fretting Wear -- 1.11.4 Corrosive Wear -- References -- 2 Engine Size and Life -- 2.1 Introduction -- 2.2 Engine Life -- 2.3 Factors on Which Life is Dependent -- 2.4 Friction Force and Power -- 2.4.1 Mechanical Efficiency -- 2.4.2 Friction -- 2.5 Similarity Studies -- 2.5.1 Characteristic Size of an Engine -- 2.5.2 Velocity -- 2.5.3 Oil Film Thickness -- 2.5.4 Velocity Gradient -- 2.5.5 Friction Force or Power -- 2.5.6 Indicated Power and Efficiency -- 2.6 Archard's Law of Wear -- 2.7 Wear Life of Engines -- 2.7.1 Wear Life -- 2.7.2 Nondimensional Wear Depth Achieved During Lifetime -- 2.8 Summary -- Appendix 2.A: Engine Parameters, Mechanical Efficiency and Life -- Appendix 2.B: Hardness and Fatigue Limits of Different Copper-Lead-Tin (Cu-Pb-Sn) Bearings -- Appendix 2.C: Hardness and Fatigue Limits of Different Aluminium-Tin (Al-Sn) Bearings -- References -- PART II VALVE TRAIN COMPONENTS -- 3 Inlet Valve Seat Wear in High bmep Diesel Engines -- 3.1 Introduction -- 3.2 Valve Seat Wear.
3.2.1 Design Aspects to Reduce Valve Seat Wear Life -- 3.3 Shear Strain and Wear due to Relative Displacement -- 3.4 Wear Model -- 3.4.1 Wear Rate -- 3.5 Finite Element Analysis -- 3.6 Experiments, Results and Discussions -- 3.6.1 Valve and Seat Insert of Existing Design -- 3.6.2 Improved Valve and Seat Insert -- 3.7 Summary -- 3.8 Design Rule for Inlet Valve Seat Wear in High bmep Engines -- References -- 4 Wear of the Cam Follower and Rocker Toe -- 4.1 Introduction -- 4.2 Wear of Cam Follower Surfaces -- 4.2.1 Wear Mechanism of the Cam Follower -- 4.3 Typical Modes of -- 4.4 Experiments on Cam Follower Wear -- 4.4.1 Follower Measurement -- 4.5 Dynamics of the Valve Train System of the Pushrod Type -- 4.5.1 Elastohydrodynamic and Transition of Boundary Lubrication -- 4.5.2 Cam and Follower Dynamics -- 4.6 Wear Model -- 4.6.1 Wear Coefficient -- 4.6.2 Valve Train Dynamics and Stress on the Follower -- 4.6.3 Wear Depth -- 4.7 Parametric Study -- 4.7.1 Engine Speed -- 4.7.2 Oil Film Thickness -- 4.8 Wear of the Cast Iron Rocker Toe -- 4.9 Summary -- References -- PART III LINER, PISTON AND PISTON RINGS -- 5 Liner Wear: Wear of Roughness Peaks in Sparse Contact -- 5.1 Introduction -- 5.2 Surface Texture of Liners and Rings -- 5.2.1 Surface Finish -- 5.2.2 Honing of Liners -- 5.2.3 Surface Finish Parameters -- 5.2.4 Bearing Area Curve -- 5.2.5 Representation of Bearing Area Curve of Normally Honed Surface or Surfaces with Peaked Roughness -- 5.3 Wear of Liner Surfaces -- 5.3.1 Asperities -- 5.3.2 Radius of the Asperity in the Transverse Direction -- 5.3.3 Radius in the Longitudinal Direction -- 5.3.4 Sparse Contact -- 5.3.5 Contact Pressures -- 5.3.6 Friction -- 5.3.7 Approach -- 5.3.8 Detachment of Asperities -- 5.4 Wear Model -- 5.4.1 Normally Honed Liner with Peaked Roughness -- 5.4.2 Normal Surface Roughness -- 5.4.3 Fatigue Loading of Asperities.
5.4.4 Wear Rate -- 5.4.5 Plateau Honed and Other Liners not Normally Honed -- 5.5 Liner Wear Model for Wear of Roughness Peaks in Sparse Contact -- 5.5.1 Parametric Studies -- 5.5.2 Comparison with Archard's Model -- 5.6 Discussions on Wear of Liner Roughness Peaks due to Sparse Contact -- 5.7 Summary -- Appendix 5.A Sample Calculation of the Wear of a Rough Plateau Honed Liner -- References -- 6 Generalized Boundary Conditions for Designing Diesel Pistons -- 6.1 Introduction -- 6.2 Temperature Distribution and Form of the Piston -- 6.2.1 Top Land -- 6.2.2 Skirt -- 6.3 Experimental Mapping of Temperature Field in the Piston -- 6.4 Heat Transfer in Pistons -- 6.4.1 Metal Slab -- 6.5 Calculation of Piston Shape -- 6.5.1 Popular Methods Used Before Finite Element Analysis -- 6.5.2 Calculation by Finite Element Method -- 6.5.3 Experimental Validation -- 6.6 Summary -- References -- 7 Bore Polishing Wear in Diesel Engine Cylinders -- 7.1 Introduction -- 7.2 Wear Phenomenon for Liner Surfaces -- 7.2.1 Bore Polishing -- 7.3 Bore Polishing Mechanism -- 7.3.1 Carbon Deposit Build Up on the Piston Top Land -- 7.3.2 Quality of Fuel and Oil -- 7.3.3 Piston Growth by Finite Element Method -- 7.3.4 Piston Secondary Movement -- 7.3.5 Simulation Program -- 7.4 Wear Model -- 7.4.1 Contact Pressures -- 7.4.2 Wear Rate -- 7.5 Calculation Methodology and Study of Bore Polishing Wear -- 7.5.1 Finite Element Analysis -- 7.5.2 Simulation -- 7.6 Case Study on Bore Polishing Wear in Diesel Engine Cylinders -- 7.6.1 Visual Observations -- 7.6.2 Liner Measurements -- 7.6.3 Results of Finite Element Analysis -- 7.6.4 Piston Motion -- 7.6.5 Wear Profile -- 7.6.6 Engine Oil Consumption -- 7.6.7 Methods Used to Reduce Liner Wear -- 7.7 Summary -- References -- 8 Abrasive Wear of Piston Grooves in Highly Loaded Diesel Engines -- 8.1 Introduction.
8.2 Wear Phenomenon in Piston Grooves -- 8.2.1 Abrasive Wear -- 8.2.2 Wear Mechanism -- 8.3 Wear Model -- 8.3.1 Real Contact Pressure -- 8.3.2 Approach -- 8.3.3 Wear Rate -- 8.4 Experimental Validation -- 8.4.1 Validation of the Model -- 8.4.2 Wear Measurement -- 8.5 Estimation of Wear Using Sarkar's Model -- 8.5.1 Parametric Study -- 8.6 Summary -- References -- 9 Abrasive Wear of Liners and Piston Rings -- 9.1 Introduction -- 9.2 Wear of Liner and Ring Surfaces -- 9.3 Design Parameters -- 9.3.1 Piston and Rings Assembly -- 9.3.2 Abrasive Wear -- 9.3.3 Sources of Abrasives -- 9.4 Study of Abrasive Wear on Off-highway Engines -- 9.4.1 Abrasive Wear of Rings -- 9.4.2 Abrasive Wear of Piston Pin and Liners -- 9.4.3 Accelerated Abrasive Wear Test on an Engine to Simulate Operation in the Field -- 9.5 Winnowing Effect -- 9.6 Scanning Electron Microscopy of Abrasive Wear -- 9.7 Critical Dosage of Sand and Life of Piston-Ring-Liner Assembly -- 9.7.1 Simulation of Engine Life -- 9.8 Summary -- References -- 10 Corrosive Wear -- 10.1 Introduction -- 10.2 Operating Parameters -- 10.2.1 Corrosive Wear -- 10.3 Corrosive Wear Study on Off-road Application Engines -- 10.3.1 Accelerated Corrosive Wear Test -- 10.4 Wear Related to Coolants in an Engine -- 10.4.1 Under-cooling of Liners by Design -- 10.4.2 Coolant Related Wear -- 10.5 Summary -- References -- 11 Tribological Tests to Simulate Wear on Piston Rings -- 11.1 Introduction -- 11.2 Friction and Wear Tests -- 11.2.1 Testing Friction and Wear of the Tribo-System Piston Ring and Cylinder Liner Outside of Engines -- 11.3 Test Procedures Assigned to the High Frequency, Linear Oscillating Test Machine -- 11.4 Load, Friction and Wear Tests -- 11.4.1 EP Test -- 11.4.2 Scuffing Test -- 11.4.3 Reagents and Materials -- 11.5 Test Results -- 11.5.1 Selection of Coatings for Piston Rings.
11.5.2 Scuffing Tribological Test -- 11.5.3 Hot Endurance Test -- 11.6 Selection of Lubricants -- 11.7 High Performance Bio-lubricants and Tribo-reactive Materials for Clean Automotive Applications -- 11.7.1 Synthetic Esters -- 11.7.2 Polyalkyleneglycols -- 11.8 Tribo-Active Materials -- 11.8.1 Thematic 'Piston Rings' -- 11.9 EP Tribological Tests -- 11.9.1 Piston Ring Cylinder Liner Simulation -- Acknowledgements -- References -- PART IV ENGINE BEARINGS -- 12 Friction and Wear in Engine Bearings -- 12.1 Introduction -- 12.2 Engine Bearing Materials -- 12.2.1 Babbitt or White Metal -- 12.2.2 Copper-Lead Alloys -- 12.2.3 Aluminium-based Materials -- 12.3 Functions of Engine Bearing Layers -- 12.4 Types of Overlays/Coatings in Engine Bearings -- 12.4.1 Lead-based Overlays -- 12.4.2 Tin-based Overlays -- 12.4.3 Sputter Bearing Overlays -- 12.4.4 Polymer-based Overlays -- 12.5 Coatings for Engine Bearings -- 12.6 Relevance of Lubrication Regimes in the Study of Bearing Wear -- 12.6.1 Boundary Lubrication -- 12.6.2 Mixed Film Lubrication -- 12.6.3 Fluid Film Lubrication -- 12.7 Theoretical Friction and Wear in Bearings -- 12.7.1 Friction -- 12.8 Wear -- 12.9 Mechanisms of Wear -- 12.9.1 Adhesive Wear -- 12.9.2 Abrasive Wear -- 12.9.3 Erosive Wear -- 12.10 Requirements of Engine Bearing Materials -- 12.11 Characterization Tests for Wear Behaviour of Engine Bearings -- 12.11.1 Fatigue Strength -- 12.11.2 Pin-on-disk Test -- 12.11.3 Scratch Test for Bond Strength -- 12.12 Summary -- References -- PART V LUBRICATING OILS FOR MODERN ENGINES -- 13 Heavy Duty Diesel Engine Oils, Emission Strategies and their Effect on Engine Oils -- 13.1 Introduction -- 13.2 What Drives the Changes in Diesel Engine Oil Specifications? -- 13.2.1 Role of the Government -- 13.2.2 OEMs' Role -- 13.2.3 The Consumer's Role -- 13.3 Engine Oil Requirements.
13.3.1 Overview and What an Engine Oil Must Do.
Abstract:
The critical parts of a heavy duty engine are theoretically designed for infinite life without mechanical fatigue failure. Yet the life of an engine is in reality determined by wear of the critical parts. Even if an engine is designed and built to have normal wear life, abnormal wear takes place either due to special working conditions or increased loading. Understanding abnormal and normal wear enables the engineer to control the external conditions leading to premature wear, or to design the critical parts that have longer wear life and hence lower costs. The literature on wear phenomenon related to engines is scattered in numerous periodicals and books. For the first time, Lakshminarayanan and Nayak bring the tribological aspects of different critical engine components together in one volume, covering key components like the liner, piston, rings, valve, valve train and bearings, with methods to identify and quantify wear. The first book to combine solutions to critical component wear in one volume Presents real world case studies with suitable mathematical models for earth movers, power generators, and sea going vessels Includes material from researchers at Schaeffer Manufacturing (USA), Tekniker (Spain), Fuchs (Germany), BAM (Germany), Kirloskar Oil Engines Ltd (India) and Tarabusi (Spain) Wear simulations and calculations included in the appendices Instructor presentations slides with book figures available from the companion site Critical Component Wear in Heavy Duty Engines is aimed at postgraduates in automotive engineering, engine design, tribology, combustion and practitioners involved in engine R&D for applications such as commercial vehicles, cars, stationary engines (for generators, pumps, etc.), boats and ships. This book is also a key reference for senior undergraduates looking to move onto advanced study in the above topics,
consultants and product mangers in industry, as well as engineers involved in design of furnaces, gas turbines, and rocket combustion. Companion website for the book: www.wiley.com/go/lakshmi.
Local Note:
Electronic reproduction. Ann Arbor, Michigan : ProQuest Ebook Central, 2017. Available via World Wide Web. Access may be limited to ProQuest Ebook Central affiliated libraries.
Genre:
Added Author:
Electronic Access:
Click to View