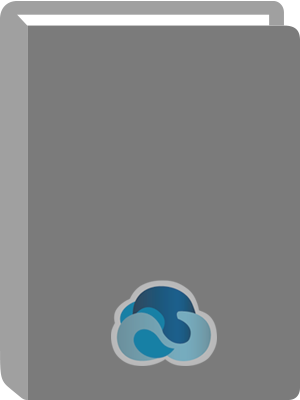
Flow-Induced Vibrations : Classifications and Lessons from Practical Experiences.
Title:
Flow-Induced Vibrations : Classifications and Lessons from Practical Experiences.
Author:
Nakamura, Tomomichi.
ISBN:
9780080983523
Personal Author:
Edition:
2nd ed.
Physical Description:
1 online resource (425 pages)
Contents:
Front Cover -- Flow-Induced Vibrations: Classifications and Lessons from Practical Experiences -- Copyright Page -- Contents -- Preface -- 1 Introduction -- 1.1 General overview -- 1.1.1 History of FIV research -- 1.1.2 Origin of this book -- 1.2 Modeling approaches -- 1.2.1 The importance of modeling -- 1.2.2 Classification of FIV and modeling -- 1.2.3 Modeling procedure -- 1.2.3.1 Simplified treatment -- 1.2.3.2 Detailed treatment -- 1.2.4 Analytical approach -- 1.2.5 Experimental approach -- 1.2.5.1 Test facilities -- 1.2.5.2 Similarity laws -- 1.2.5.2.1 Structural model -- 1.2.5.2.2 Fluid model -- 1.3 Fundamental mechanisms of FIV -- 1.3.1 Self-induced oscillation mechanisms -- 1.3.1.1 One-degree-of-freedom system -- 1.3.1.2 Two-degrees-of-freedom system -- 1.3.1.3 Multi-degrees-of-freedom system -- 1.3.2 Forced vibration and added mass and damping -- 1.3.2.1 Forced vibration system -- 1.3.2.2 Added mass -- 1.3.2.3 Fluid damping -- References -- 2 Vibration Induced by Cross-Flow -- 2.1 Single circular cylinder -- 2.1.1 Structures under evaluation -- 2.1.2 Vibration mechanisms and historical review -- 2.1.2.1 Vibration mechanisms -- 2.1.2.1.1 Bending vibration of a circular cylindrical structure in steady flow -- 2.1.2.1.2 Vibration of a circular cylinder in oscillating flow -- 2.1.2.1.3 Ovalling vibrations of cylindrical shells in steady flow -- 2.1.2.2 Historical background -- 2.1.2.2.1 Bending vibrations of a circular cylinder in steady flow -- 2.1.2.2.2 Vibration of a circular cylinder in oscillating flow -- 2.1.2.2.3 Ovalling vibrations of cylindrical shells in steady flow -- 2.1.3 Evaluation methods -- 2.1.3.1 Bending vibrations of a circular cylinder in steady flow -- 2.1.3.1.1 Vibration induced by single-phase flow -- 2.1.3.1.2 Vibration induced by two-phase flow -- 2.1.3.2 Vibration of a circular cylinder in oscillating flow.
2.1.3.3 Ovalling vibrations of cylindrical shells in steady flow -- 2.1.4 Examples of component failures due to vortex-induced vibration -- 2.2 Two circular cylinders in cross-flow -- 2.2.1 Outline of structures of interest -- 2.2.1.1 Examples -- 2.2.1.2 Classification based on flow type -- 2.2.1.3 Classification based on spatial configuration -- 2.2.2 Historical background -- 2.2.2.1 Excitation phenomena -- 2.2.2.1.1 Vibration of cylinder pairs subjected to steady cross-flow -- 2.2.2.1.2 Oscillatory-flow-induced vibration -- 2.2.2.2 Research background -- 2.2.2.2.1 Steady-flow-induced cylinder vibration -- 2.2.2.2.2 Oscillatory flow -- 2.2.2.2.3 Vibration of cylinder pairs in two-phase flow -- 2.2.3 Evaluation methodology -- 2.2.3.1 Experimental evaluation -- 2.2.3.1.1 Vibration of cylinder pair in single-phase flow -- 2.2.3.2 Theoretical modeling -- 2.2.3.2.1 Wake interference mathematical model -- 2.2.3.2.2 Fluid-structure coupled analysis -- 2.2.3.2.3 Determination of instability boundary by unsteady fluid force models -- 2.2.3.2.4 Quasi-steady theory -- 2.2.4 Examples of practical problems -- 2.3 Multiple circular cylinders -- 2.3.1 Outline of structures considered -- 2.3.2 Vibration evaluation history -- 2.3.2.1 Excitation mechanisms -- 2.3.2.2 Historical background -- 2.3.3 Estimation method -- 2.3.3.1 Vibration in single-phase flow -- 2.3.3.1.1 Steady flow -- 2.3.3.1.2 Non-uniform flow -- 2.3.3.2 Vibration induced by two-phase flow -- 2.3.3.2.1 Vortex shedding -- 2.3.3.2.2 Fluidelastic vibration -- 2.3.3.2.3 Random vibration -- 2.3.4 Examples of component failures -- 2.4 Bodies of rectangular and other cross-section shapes -- 2.4.1 General description of cross-section shapes -- 2.4.1.1 Products focused on -- 2.4.1.2 Classification based on fluid flow -- 2.4.1.3 Classification by vibration mode of structure.
2.4.1.3.1 Two-dimensional vibration within the cross-section plane -- 2.4.1.3.2 Axial vibration -- 2.4.1.4 Objectives -- 2.4.2 FIV of rectangular-cross-section structures and historical review -- 2.4.2.1 FIV phenomena -- 2.4.2.1.1 Vortex-induced vibration -- 2.4.2.1.2 Turbulence-induced vibration -- 2.4.2.1.3 Galloping -- 2.4.2.2 Historical background -- 2.4.2.2.1 Vortex-induced vibration -- 2.4.2.2.2 Turbulence-induced vibration -- 2.4.2.2.3 Galloping -- 2.4.3 Evaluation methods -- 2.4.3.1 Vortex-induced vibration -- 2.4.3.1.1 Strouhal number for zero attack angle of rectangular-cross-section body -- 2.4.3.1.2 Strouhal number for a rectangular-cross-section body inclined to the flow -- 2.4.3.1.3 Flow speed range of vortex-induced vibrations for a rectangular-cross-section body -- 2.4.3.1.4 Vibration amplitude of vortex-induced vibrations for a rectangular-cross-section body -- 2.4.3.2 Turbulence-induced vibration -- 2.4.3.3 Galloping -- 2.4.4 Examples of structural failures and suggestions for countermeasures -- 2.5 Acoustic resonance in tube bundles -- 2.5.1 Relevant industrial products and a brief description of the phenomenon -- 2.5.1.1 Relevant industrial products -- 2.5.1.2 Mechanism underlying resonance -- 2.5.1.3 Classification of resonance phenomena -- 2.5.2 Historical background -- 2.5.2.1 Review of research on transverse mode resonance -- 2.5.2.1.1 Resonance prediction methods -- 2.5.2.1.2 Baffle plate design method -- 2.5.2.1.3 Studies on the feedback mechanism -- 2.5.2.2 Review of research on longitudinal mode resonance -- 2.5.3 Resonance prediction method at the design stage -- 2.5.3.1 Prediction based on the first condition: coincidence of vortex shedding frequency with natural frequencies of acous... -- 2.5.3.2 Prediction based on the second condition: balance between energy supplied by vortex shedding and the energy dissipa...
2.5.3.2.1 Y.N. Chen's method -- 2.5.3.2.2 Eisinger's method -- 2.5.4 Examples of acoustic resonance problems and hints for anti-resonance design -- 2.5.4.1 Waste heat recovery boiler -- 2.5.4.2 Shell and tube type heat exchanger -- 2.5.4.3 Coal-fired boiler -- 2.6 Prevention of FIV -- References -- 3 Vibration Induced by External Axial Flow -- 3.1 Single cylinder/multiple cylinders -- 3.1.1 Summary of objectives -- 3.1.2 Random vibration due to flow turbulence -- 3.1.2.1 Historical background of evaluation methodologies -- 3.1.2.2 Evaluation of random vibration in single-phase flow -- 3.1.2.3 Random vibration evaluation in two-phase flow -- 3.1.2.4 Semi-empirical formulae for vibration amplitude prediction -- 3.1.3 Flutter and divergence -- 3.1.3.1 Historical background -- 3.1.3.2 Evaluation methods and countermeasures against instability -- 3.1.4 Examples of reported component-vibration problems and hints for countermeasures -- 3.2 Vibration of elastic plates and shells -- 3.2.1 Bending-torsion flutter -- 3.2.1.1 Historical background -- 3.2.1.2 Evaluation method -- 3.2.2 Panel flutter -- 3.2.2.1 Historical background -- 3.2.2.2 Evaluation method -- 3.2.3 Shell flutter due to annular flow -- 3.2.4 Turbulence-induced vibration -- 3.2.4.1 Summary -- 3.2.4.2 Evaluation method -- 3.2.5 Hints for countermeasures -- 3.2.5.1 Self-excited vibrations -- 3.2.5.2 Turbulence-induced vibrations -- 3.3 Vibration induced by leakage flow -- 3.3.1 General description of the problem -- 3.3.1.1 Single-degree-of-freedom translational systems -- 3.3.1.2 Other cases -- 3.3.2 Evaluation method for single-degree-of-freedom translational system -- 3.3.2.1 Basic equations of leakage flow -- 3.3.2.2 Relation between steady flow rate and pressure difference across the passage -- 3.3.2.3 Unsteady fluid forces of a tapered passage.
3.3.3 Analysis method for single-degree-of-freedom translational system with leakage-flow passage of arbitrary shape -- 3.3.3.1 Steady fluid force -- 3.3.3.2 Unsteady fluid force -- 3.3.4 Mechanism of self-excited vibration -- 3.3.5 Self-excited vibrations in other cases -- 3.3.5.1 Rotational vibration of one-dimensional tapered passage wall -- 3.3.5.2 Two-degrees-of-freedom translational and rotational systems and continuous systems -- 3.3.5.3 Annular flow passage -- 3.3.6 Hints for countermeasures -- 3.3.7 Examples of leakage-flow-induced vibration -- References -- 4 Vibrations Induced by Internal Fluid Flow -- 4.1 Vibration of straight and curved pipes conveying fluid -- 4.1.1 Vibration of pipes conveying fluid -- 4.1.1.1 Research history -- 4.1.1.2 Modeling and stability analysis of straight pipes conveying fluid -- 4.1.1.3 Stability of straight pipes conveying fluid -- 4.1.1.4 Stability of curved pipes conveying fluid -- 4.1.1.5 Shell flutter and random vibration induced by internal fluid flow -- 4.1.1.6 Hints for countermeasures -- 4.1.2 Vibration of pipes excited by oscillating and two-phase fluid flow -- 4.1.2.1 Research history -- 4.1.2.2 Frequency response of pipes with bends -- 4.1.2.3 Hints for countermeasures -- 4.1.3 Piping vibration caused by gas-liquid two-phase flow -- 4.1.3.1 Summary -- 4.1.3.2 Two-phase flow regimes -- 4.1.3.3 Evaluation method -- 4.1.3.4 Case examples and methods to reduce piping vibration -- 4.2 Vibration related to bellows -- 4.2.1 Vibration of bellows -- 4.2.1.1 Mechanism of flow-induced vibration -- 4.2.1.2 Other vibration mechanisms -- 4.2.1.3 History of studies on bellows vibration -- 4.2.1.3.1 Studies on mechanical natural frequencies of bellows -- 4.2.1.3.2 Studies on bellows Strouhal numbers -- 4.2.1.4 Evaluation method for the flow-induced vibration of bellows.
4.2.1.4.1 Fluid added mass for axial vibration of single bellows.
Abstract:
In many plants, vibration and noise problems occur due to fluid flow, which can greatly disrupt smooth plant operations. These flow-related phenomena are called flow-induced vibration. This book explains how and why such vibrations happen and provides hints and tips on how to avoid them in future plant design. The world-leading author team doesn't assume prior knowledge of mathematical methods and provides the reader with information on the basics of modeling. The book includes several practical examples and thorough explanations of the structure, the evaluation method and the mechanisms to aid understanding of flow-induced vibrations. Helps ensure smooth plant operations Explains the structure, evaluation method and mechanisms Shows how to avoid vibrations in future plant design.
Local Note:
Electronic reproduction. Ann Arbor, Michigan : ProQuest Ebook Central, 2017. Available via World Wide Web. Access may be limited to ProQuest Ebook Central affiliated libraries.
Genre:
Electronic Access:
Click to View