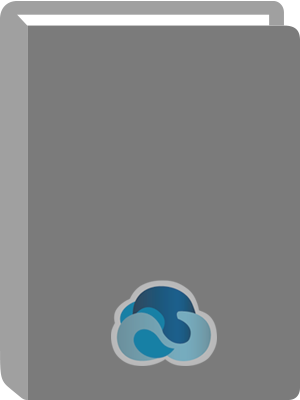
New Appoaches in the Process Industries : The Manufacturing Plant of the Future.
Title:
New Appoaches in the Process Industries : The Manufacturing Plant of the Future.
Author:
Dal Pont, Jean-Pierre.
ISBN:
9781118984529
Personal Author:
Edition:
1st ed.
Physical Description:
1 online resource (278 pages)
Series:
FOCUS Series
Contents:
Cover -- Title Page -- Copyright -- Contents -- Foreword -- Acknowledgements -- Introduction -- Chapter 1. Project Management - Systems Engineering - The Industrialization Process -- 1.1. Projects and project management -- 1.1.1. Definitions -- 1.1.2. Project critical success factors -- 1.2. Systems engineering -- 1.2.1. Systems classification -- 1.3. The industrialization process -- 1.3.1. Definition: the industrialization steps -- 1.3.2. Origin of projects - the initialization phase - preliminary projects -- 1.3.3. Industrialization steps. Typical costs and relevant documents - time scale -- 1.3.4. Validation steps and project stakeholders' involvement -- 1.4. Project engineering -- 1.4.1. Conceptual engineering and WBS -- 1.4.2. Project organization: customer/contractor relationship -- 1.4.3. Project scope control: engineering tools -- 1.4.4. The project on the owner's side - the investment file - impact on company profitability -- 1.5. Bibliography -- Chapter 2. Metrics For Sustainability Assessment of Chemical Processes -- 2.1. Sustainable development in chemical process engineering -- 2.2. Indicators, indices and metrics for sustainability -- 2.3. Frontiers of the system -- 2.4. Metrics -- 2.4.1. Stages in sustainable process design -- 2.4.2. AIChE metrics -- 2.4.3. IChemE metrics -- 2.4.4. Using metrics for sustainable development -- 2.4.5. Potential environmental impact index (waste reduction algorithm, WAR) -- 2.4.6. Sustainable process index (SPI) -- 2.4.7. Exergy as a thermodynamic base for sustainable development metrics -- 2.4.8. Indicators from system-based environmental assessment management -- 2.4.9. Toward a sustainable lifecycle assessment -- 2.5. Design methods for sustainable processes and systems.
2.5.1. Several roads to more sustainable processes and systems -- 2.5.2. Industrial ecology -- 2.5.3. Lifecycle assessment -- 2.5.4. Green chemistry/green engineering, process intensification and waste management -- 2.6. Conclusions -- 2.7. Bibliography -- Chapter 3. From Preliminary Projects to Projects -- 3.1. Introduction -- 3.2. Process design: an interactive and multiple-step activity -- 3.3. Process flowsheeting -- 3.4. Optimization methods -- 3.4.1. Multi-objective optimization (MOOP) -- 3.4.2. MCDM (Multiple Choice Decision-Making) methods -- 3.5. Literature review in process modeling/optimization techniques and tools based on LCA -- 3.6. Case study: eco-designing a biodiesel production process -- 3.6.1. Biodiesel as an alternative to fossil fuel -- 3.6.2. Methodology and tools -- 3.6.3. Biodiesel production simulation -- 3.6.4. Inventory data and identification of potential factors -- 3.6.5. Optimization of biodiesel production -- 3.7. Conclusions and suggestions -- 3.8. Bibliography -- Chapter 4. Analysis of the Strategy of the Enterprise and the Enterprise Strategic Plan -- 4.1. The industrial enterprise: basic main features -- 4.2. The couple "product/market" -- 4.2.1. Product viewed at the enterprise level -- 4.2.2. The product seen by the customer -- 4.3. Product profitability: turnover and margins -- 4.3.1. Product cost evaluation -- 4.3.2. Margin analysis -- 4.4. Company and industrial processes evaluation -- 4.4.1. Benchmarking -- 4.4.2. Industrial site selection and existing site evaluation -- 4.4.3. BCG analysis -- 4.4.4. SWOT analysis -- 4.5. Enterprise industrial strategic analysis -- 4.6. Enterprise industrial strategic action plan -- 4.7. Bibliography -- Chapter 5. Excellence in Manufacturing and Operations Control -- 5.1. Importance of manufacturing.
5.2. The manufacturing facility - the heart of the industrial enterprise -- 5.2.1. The supply chain concept -- 5.3. Typology of industrial facilities and technology considerations -- 5.3.1. Production unit - main types -- 5.3.2. VAT analysis -- 5.3.3. Plant support functions -- 5.3.4. Interaction between manufacturing site and the corporate functions -- 5.3.5. Plant architecture -- 5.4. Operations management -- 5.4.1. The two modes of a company/manufacturing operations: the operational mode and the entrepreneurial mode -- 5.4.2. Plant operations monitoring and control -- 5.5. Excellence in manufacturing - Toyota system - World Class Manufacturing -- 5.5.1. TOYOTISM" or "Toyota production system (TPS)" -- 5.5.2. Excellence in manufacturing - other methods -- 5.5.3. World Class Manufacturing (WCM) -- 5.5.4. Human aspects - production personnel -- 5.6. Bibiliography -- Chapter 6. Innovation and Change Management -- 6.1. Innovation -- 6.2. Change management -- 6.2.1. The company, a multitude of processes (processes, methods, procedures) -- 6.2.2. The expertise of the company - knowledge management -- 6.2.3. Core competencies -- 6.2.4. Human aspects of change -- 6.2.5. Change management key success drivers -- 6.2.6. Incremental improvement or breakthrough -- 6.3. Looking for breakthroughs - process improvement team (PTI) -- 6.4. Re-engineering, the American way -- 6.5. Bibliography -- Chapter 7. Water and Energy Challenges -- 7.1. The energy challenge -- 7.2. The water-energy nexus in process industries -- 7.3. The key role of process systems engineering -- 7.3.1. Energy integration: HEN, pinch analysis, exergy and mathematical optimization modeling -- 7.3.2. Mass integration, mass exchange networks and application to water allocation networks (WAN).
7.3.3. Minimizing water and energy consumptions in water and heat exchange networks -- 7.3.4. Multi-objective optimization of the hydrogen supply Chain (HSC) in the Midi-Pyrénées Region, France -- 7.4. Conclusions -- 7.5. Bibliography -- Chapter 8. Engineers as Key Players for Sustainability: The Role of Pse Academia -- 8.1. The path to sustainability education for engineers -- 8.2. Process systems engineering as the cornerstone of sustainability -- 8.3. Reinforcing engineering ethics -- 8.4. Implementing sustainability in engineering education -- 8.4.1. Tier 1 - sustainability at the core of chemical and process engineering curricula -- 8.4.2. Tier 2 - sustainable energy systems engineering -- 8.4.3. Tier 3 - sustainable development as a whole: a systems thinking discipline based on complexity theory -- 8.5. Conclusions -- 8.6. Bibliography -- Chapter 9. Plant of the Future -- 9.1. The enterprise, its manufacturing plants and society -- 9.1.1. Corporate social responsibility (CSR) -- 9.1.2. Circular economy -- 9.2. Engineering revisited -- 9.2.1. Enterprise and engineering company cooperation - Project scope definition -- 9.2.2. Project scope (Box A) -- 9.2.3. HSE Matters (Box B) -- 9.2.4. Human factors - operations control (Box C) -- 9.2.5. Project owner's clients and suppliers (Box D) -- 9.2.6. CAPEX - OPEX optimization -- 9.3. Equipment manufacturers and project engineering -- 9.3.1. Case study -- pump selection -- 9.3.2. Case study: TWIN SCREW Extruder -- 9.4. Modular process systems - skid mounted systems -- 9.4.1. Modular construction -- 9.4.2. Equipment on skid - Transportable units and artifacts - miscellaneous prefabrication -- 9.4.3. Container modules - The F3 factory - process intensification -- 9.5. Designing for flexibility -- 9.5.1. Raw materials - energy -- 9.5.2. Operations.
9.5.3. Flexibility and customer satisfaction -- 9.5.4. Innovative plant -- 9.6. Manufacturing and process industries toward the 4.0 plant -- 9.6.1. Traceability -- 9.6.2. 3D printing -- 9.6.3. The 4.0 plant - the digital plant -- 9.7. Operations abroad -- 9.7.1. Transfer of technology - facility building -- 9.7.2. The case of developing countries -- 9.7.3. International management: expatriation -- 9.8. The manufacturing plant of the future -- 9.8.1. First tier: products, markets, sales, competition, R&D benchmarking, globalization, societal demands and constraints, and enterprise strategy -- 9.8.2. Second tier: process selection (raw materials, water and energy availability), risks assessment, site selection, CAPEX, OPEX, plant architecture and project scope -- 9.8.3. Third tier: realization engineering -- 9.8.4. Fourth tier: the enterprise organization, plant operations and management, the workplace, knowledge worker, customer satisfaction, continuous improvement, flexibility and innovation for survival -- 9.9. Bibliography -- Appendix -- Index.
Abstract:
Competition from emerging and developing countries, challenges related to energy and water, the continuing increase in the global population and the obligation to be sustainable are all impacting developed countries such as the United States, France, etc. Manufacturing has been almost totally neglected by these developed countries and thus there is a strong need to review R&D and the development and industrialization processes. This is a prerequisite for maintaining and improving welfare and quality of life. The industrialization process can be defined as the process of converting research or laboratory experiments into a physical tool capable of producing a product of value for customers of specified markets. Such a process implies knowledge of BAT (best available techniques) in chemical engineering, plant design, production competitiveness, the proper utilization of tools (toolbox concept) such as value assessment, value engineering, eco-design, LCA (lifecycle analysis), process simulation, modeling, innovation and appropriate metrics usage. These are mandatory to ensure commercial success and covered by the authors of this book.
Local Note:
Electronic reproduction. Ann Arbor, Michigan : ProQuest Ebook Central, 2017. Available via World Wide Web. Access may be limited to ProQuest Ebook Central affiliated libraries.
Genre:
Added Author:
Electronic Access:
Click to View