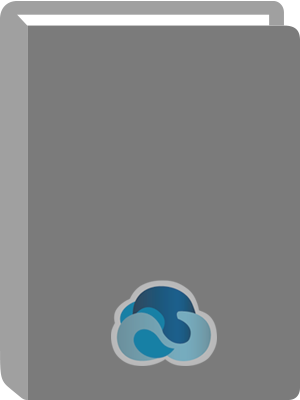
Process Planning : The Design/Manufacture Interface.
Title:
Process Planning : The Design/Manufacture Interface.
Author:
Scallan, Peter.
ISBN:
9780080473994
Personal Author:
Edition:
1st ed.
Physical Description:
1 online resource (497 pages)
Contents:
front cover -- copyright -- table of contents -- front matter -- Preface -- Acknowledgements -- body -- 1 Introduction to manufacturing -- 1.1 Introduction -- 1.2 Aims and objectives -- 1.3 What is manufacturing? -- 1.4 What is a manufacturing system? -- 1.5 Inputs and outputs of a manufacturing system -- 1.6 Common characteristics of a manufacturing system -- 1.7 Developing a manufacturing strategy -- 1.8 Manufacturing organizational structures -- 1.9 Categories of manufacturing system -- 1.10 Processing strategies -- 1.11 Plant layout -- 1.12 Manufacturing engineering -- 1.13 Summary -- Case study 1.1: Re- organization at Edward Marks Ltd* -- Case study 1.2: Manufacturing at Stickley Furniture* -- 2 What is process planning? -- 2.1 Introduction -- 2.2 Aims and objectives -- 2.3 Design and manufacture cycle -- 2.4 What is process planning? -- 2.5 Process planning Ò the design/ manufacture interface -- 2.6 Process planning activities -- 2.7 Process planning and industrial engineering -- 2.8 Process planning and quality assurance -- 2.9 Process planning and production planning -- 2.10 Process planning methods -- 2.11 Basic process planning terminology -- 2.12 Summary -- Case study 2.1: Manufacturing at McCall Diesel Works* -- Case study 2.2: Planning at High Performance Pumps* -- 3 Drawing interpretation -- 3.1 Introduction -- 3.2 Aims and objectives -- 3.3 Engineering communication -- 3.4 Identifying useful supplementary information -- 3.5 Material and specification -- 3.7 Equivalent parts ( interchangeability and standardization) -- 3.6 Special material treatments -- 3.9 Tool references -- 3.8 Screw thread forms -- 3.10 Dimensional tolerances -- 3.11 Limits and fits -- 3.12 Gauge references -- 3.13 Geometrical tolerances -- 3.14 Surface finish -- 3.15 Identifying the critical processing factors -- 3.16 Summary.
Case study 3.1: Standardization at JH Engineering* -- Case study 3.2: Analysis and interpretation of adapter ring -- Material evaluation and process selection -- 4.1 Introduction -- 4.2 Aims and objectives -- 4.3 Basic classification of materials for manufacture -- 4.4 Basic material properties -- 4.5 Metals -- 4.6 Ceramics -- 4.7 Polymers -- 4.8 Composites and semiconductors -- 4.9 Material selection process and methods -- 4.10 Material evaluation method -- 4.11 Manufacturing processes -- 4.12 Process selection -- 4.13 Process and operations sequencing -- 4.14 Summary -- Case study 4.1: Material evaluation for a car alternator* -- Case study 4.2: Material and process selection for car bumpers* -- 5 Production equipment and tooling selection -- 5.1 Introduction -- 5.2 Aims and objectives -- 5.3 Production equipment for specific processes -- 5.4 Factors in equipment selection -- 5.5 Machine selection method -- 5.6 Tooling for specific production equipment -- 5.7 Factors in tooling selection -- 5.8 Tooling selection method -- 5.9 Summary -- 6 Process parameters -- 6.1 Introduction -- 6.2 Aims and objectives -- 6.3 Factors affecting speeds, feeds and depth of cut -- 6.4 Surface cutting speeds -- 6.5 Spindle speeds and number of strokes -- 6.6 Feed rates -- 6.7 Speeds and feeds for NC machines -- 6.8 Depth of cut -- 6.9 Machining times -- 6.10 Summary -- 7 Workholding devices -- 7.1 Introduction -- 7.2 Aims and objectives -- 7.3 General-purpose workholding devices -- 7.4 What are jigs and fixtures? -- 7.5 General factors in workholder design and selection -- 7.6 Basic principles of jig and fixture design -- 7.7 Design methodology for jig and fixture design -- 7.8 Types of jig and fixture -- 7.9 Principles and practice of location -- 7.10 Principles and practice of clamping -- 7.11 Standard parts for jigs and fixtures -- 7.12 Workholding for NC machines.
7.13 Further workholding devices -- 7.14 Summary -- Case study 7.1: Designing a jig for a simple pin -- Case study 7.2: Designing a plate- type jig -- Case study 7.3: Designing a sandwich jig -- Selection of quality assurance methods -- 8.1 Introduction -- 8.2 Aims and objectives -- 8.3 What is quality assurance? -- 8.4 Statistical quality control -- 8.5 Process control -- 8.6 Statistical process control -- 8.7 Process capability -- 8.8 Inspection and measurement -- 8.9 Summary -- 9 Economics of process planning -- 9.1 Introduction -- 9.2 Aims and objectives -- 9.3 Manufacturing costs -- 9.4 Cost categories -- 9.5 Job/batch costing -- 9.6 Marginal costing -- 9.7 Manufacturing materials and costs -- 9.8 Manufacturing processes and costs -- 9.9 The 'make or buy?' decision -- 9.10 Summary -- 10 From design to manufacture -- 10.1 Introduction -- 10.2 Aims and objectives -- 10.3 Organization -- 10.4 Component -- 10.5 Drawing interpretation and material evaluation -- 10.6 Process selection and sequencing -- 10.7 Machine selection and operations sequencing -- 10.8 Tooling selection -- 10.9 Setting the process parameters -- 10.10 Determining workholding requirements -- 10.11 Selection of quality assurance methods -- 10.12 Documenting the process plan -- 10.13 Costing the plan -- 10.14 Summary -- back matter -- Appendices -- Appendix A: Control chart factors for variables -- Appendix B: Blank control charts -- Appendix C: Blank process planning documents -- index.
Abstract:
Process Planning covers the selection of processes, equipment, tooling and the sequencing of operations required to transform a chosen raw material into a finished product. Initial chapters review materials and processes for manufacturing and are followed by chapters detailing the core activities involved in process planning, from drawing interpretation to preparing the final process plan. The concept of maximising or 'adding value' runs throughout the book and is supported with activities. Designed as a teaching and learning resource, each chapter begins with learning objectives, explores the theory behind process planning, and sets it in a 'real-life' context through the use of case studies and examples. Furthermore, the questions in the book develop the problem-solving skills of the reader. ISO standards are used throughout the book (these are cross-referenced to corresponding British standards). This is a core textbook, aimed at undergraduate students of manufacturing engineering, mechanical engineering with manufacturing options and materials science. * Features numerous case studies and examples from industry to help provide an easy guide to a complex subject * Fills a gap in the market for which there are currently no suitable texts * Learning aims and objectives are provided at the beginning of each chapter - a user-friendly method to consolidate learning.
Local Note:
Electronic reproduction. Ann Arbor, Michigan : ProQuest Ebook Central, 2017. Available via World Wide Web. Access may be limited to ProQuest Ebook Central affiliated libraries.
Genre:
Electronic Access:
Click to View