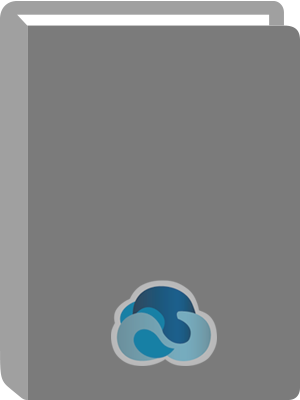
Welding Metallurgy and Weldability of Nickel-Base Alloys.
Title:
Welding Metallurgy and Weldability of Nickel-Base Alloys.
Author:
Lippold, John C.
ISBN:
9780470500217
Personal Author:
Edition:
1st ed.
Physical Description:
1 online resource (456 pages)
Contents:
WELDING METALLURGY AND WELDABILITY OF NICKEL-BASE ALLOYS -- CONTENTS -- Preface -- 1. Introduction -- 1.1 Ni-base Alloy Classification -- 1.1.1 Commercially Pure Nickel Alloys -- 1.1.2 Solid-Solution Strengthened Alloys -- 1.1.3 Precipitation-Strengthened Alloys -- 1.1.4 Other Specialty Alloys -- 1.2 History of Nickel and Ni-base Alloys -- 1.3 Corrosion Resistance -- 1.4 Nickel Alloy Production -- References -- 2. Alloying Additions, Phase Diagrams, and Phase Stability -- 2.1 Introduction -- 2.2 General Influence of Alloying Additions -- 2.3 Phase Diagrams for Solid-Solution Alloys -- 2.3.1 The Ni-Cu System -- 2.3.2 The Ni-Cr System -- 2.3.3 Ni-Mo System -- 2.3.4 The Ni-Fe-Cr System -- 2.3.5 Ni-Cr-Mo System -- 2.4 Phase Diagrams for Precipitation Hardened Alloys-γ' Formers -- 2.5 Phase Diagrams for Precipitation-Hardened Alloys-γ'' Formers -- 2.6 Calculated Phase Stability Diagrams -- 2.7 PHACOMP Phase Stability Calculations -- References -- 3. Solid-Solution Strengthened Ni-base Alloys -- 3.1 Standard Alloys and Consumables -- 3.2 Physical Metallurgy and Mechanical Properties -- 3.3 Welding Metallurgy -- 3.3.1 Microstructural Evolution in the Fusion Zone -- 3.3.1.1 Interfaces in Single Phase Austenitic Weld Metal -- 3.3.1.1.1 Solidification Subgrain Boundaries (SSGBs) -- 3.3.1.1.2 Solidification Grain Boundaries (SGBs) -- 3.3.1.1.3 Migrated Grain Boundaries (MGBs) -- 3.3.1.2 Elemental Segregation during Solidification -- 3.3.1.3 Phase Transformation Sequence -- 3.3.2 Heat Affected Zone -- 3.3.3 Postweld Heat Treatment -- 3.3.3.1 Stress Relief Heat Treatments -- 3.3.3.2 Homogenization of Weld Metal Microstructure -- 3.4 Mechanical Properties of Weldments -- 3.4.1 Hydrogen Effects -- 3.4.2 Postweld Heat Treatment -- 3.5 Weldability -- 3.5.1 Fusion Zone Solidification Cracking -- 3.5.2 HAZ Liquation Cracking.
3.5.3 Avoiding Solidification and Liquation Cracking -- 3.5.4 Ductility-Dip Cracking -- 3.5.4.1 Description of Ductility-Dip Cracking -- 3.5.4.2 Proposed Mechanisms for Ductility-Dip Cracking -- 3.5.4.3 Ductility-Dip Cracking in Ni-base Weld Metals -- 3.5.4.4 Avoiding Ductility-Dip Cracking -- 3.6 Corrosion Resistance -- 3.7 Case Studies -- 3.7.1 Pitting Corrosion in MONEL(®) Welds -- References -- 4. Precipitation-Strengthened Ni-base Alloys -- 4.1 Standard Alloys and Consumables -- 4.2 Physical Metallurgy and Mechanical Properties -- 4.3 Welding Metallurgy -- 4.3.1 Microstructural Evolution in the Fusion Zone -- 4.3.1.1 Elemental Segregation during Solidification -- 4.3.1.2 Phase Transformations-γ' Formation -- 4.3.1.3 Phase Transformations-Carbide Formation -- 4.3.1.4 Phase Transformations-γ'' Formation -- 4.3.1.5 Effect of Nb and C -- 4.3.1.6 Fusion Zone Microstructure Predictions using New PHACOMP -- 4.3.2 Heat-Affected Zone -- 4.3.3 Postweld Heat Treatment -- 4.4 Mechanical Properties of Weldments -- 4.5 Weldability -- 4.5.1 Solidification Cracking -- 4.5.1.1 Effect of Minor Element Additions-B and Zr -- 4.5.1.2 Effect of Nb Additions -- 4.5.1.3 Cast Pin Tear Test Results -- 4.5.1.4 Summary of Solidification Cracking -- 4.5.2 HAZ Liquation Cracking -- 4.5.2.1 Composition Effects -- 4.5.2.2 Effect of Grain Size -- 4.5.2.3 Effect of Heat Treatment -- 4.5.2.4 Effect of Thermal Stress/Strain -- 4.5.2.5 Summary of HAZ Liquation Cracking -- 4.5.3 Strain-Age Cracking -- 4.5.3.1 Mechanism for Strain-Age Cracking -- 4.5.3.2 Effect of Residual, Thermal and Aging Stresses, and Joint Restraint -- 4.5.3.3 Composition Effects -- 4.5.3.4 Grain Size -- 4.5.3.5 Preweld Condition of the Base Metal -- 4.5.3.6 Effect of Welding Procedure -- 4.5.3.7 Effect of Postweld Heat Treatment -- 4.5.3.8 Summary of Strain-Age Cracking -- References.
5. Oxide Dispersion Strengthened Alloys and Nickel Aluminides -- 5.1 Oxide Dispersion Strengthened Alloys -- 5.1.1 Physical and Mechanical Metallurgy -- 5.1.2 Welding Metallurgy -- 5.1.3 Summary of the Weldability of ODS Alloys -- 5.2 Nickel Aluminide Alloys -- 5.2.1 Physical and Mechanical Metallurgy -- 5.2.2 Weldability of the Ni-Aluminides -- 5.2.2.1 Elevated Temperature Cracking -- 5.2.2.2 Hot Ductility Behavior -- 5.2.2.3 Brazing -- 5.2.3 Summary of the Weldability of Nickel Aluminide Alloys -- References -- 6. Repair Welding of Ni-base Alloys -- 6.1 Solid-Solution Strengthened Alloys -- 6.2 Precipitation-Strengthened Alloys -- 6.2.1 Alloy 718 -- 6.2.1.1 Effect of δ-phase Formation -- 6.2.1.2 Rejuvenation Heat Treatments -- 6.2.1.3 Summary of Repair Weldability of Alloy 718 -- 6.2.2 Waspaloy -- 6.3 Single Crystal Superalloys -- 6.3.1 Control of Single Crystal Weld Repairs -- 6.3.2 Solidification Cracking -- 6.3.3 Optimizing Processing Parameters -- References -- 7. Dissimilar Welding -- 7.1 Application of Dissimilar Welds -- 7.2 Influence of Process Parameters on Fusion Zone Composition -- 7.3 Carbon, Low Alloy and Stainless Steels -- 7.3.1 Determining Weld Metal Constitution -- 7.3.2 Fusion Boundary Transition Region -- 7.3.3 Weldability -- 7.3.3.1 Solidification Cracking -- 7.3.3.2 Clad Disbonding -- 7.3.3.3 Creep Failure in the HAZ of Carbon Steel or Low Alloy Steel -- 7.3.3.4 Postweld Heat Treatment Cracking -- 7.4 Postweld Heat Treatment Cracking in Stainless Steels Welded with Ni-base Filler Metals -- 7.5 Super Austenitic Stainless Steels -- 7.6 Dissimilar Welds in Ni-base Alloys-Effect on Corrosion Resistance -- 7.7 9%Ni Steels -- 7.7.1 Physical Metallurgy of 9%Ni Steels -- 7.7.2 Hot Cracking of Ni-base Deposits -- 7.8 Super Duplex Stainless Steels -- 7.9 Case Studies.
7.9.1 Postweld Heat Treatment Cracking of Thick Section Welds in Alloy 800H Made with ENiCrFe-2 Filler Metal -- 7.9.2 Alloy 925 Welded with ERNiCrMo-15 (INCO-WELD 725NDUR) for Manufacturing Vacuum Insulated Oil Patch Tubing -- 7.9.3 Corrosion-Fatigue of Alloy 625 Weld Overlays -- 7.9.4 Overlay of "Safe-End" Welds using High-Cr, Ni-base Filler Metals -- References -- 8. Weldability Testing -- 8.1 Introduction -- 8.1.1 Weldability Testing Approaches -- 8.1.2 Types of Weldability Test Techniques -- 8.2 The Varestraint Test -- 8.2.1 Technique for Quantifying Weld Solidification Cracking -- 8.2.2 Technique for Quantifying HAZ Liquation Cracking -- 8.3 Modified Cast Pin Tear Test -- 8.4 The Sigmajig Test -- 8.5 The Hot Ductility Test -- 8.6 The Strain-to-Fracture Test -- 8.7 Other Weldability Tests -- References -- Appendix A Composition of Wrought and Cast Nickel-Base Alloys -- Appendix B Composition of Nickel and Nickel Alloy Consumables -- Appendix C Corrosion Acceptance Testing Methods -- Appendix D Etching Techniques for Ni-base Alloys and Welds -- Author Index -- Subject Index.
Abstract:
John N. DuPont, PhD, is the R.D. Stout Distinguished Professor in the Materials Science and Engineering Department at Lehigh University and Associate Director of the Energy Research Center. A Fellow of both the American Welding Society and ASM International, Dr. DuPont has won numerous awards for his research and teaching, including the Charles H. Jennings Memorial Award., the William Spraragen Memorial Award, the Masubuchi Award., the Lehigh Teaching Excellence Award, and the McKay-Helm award. He and his students have published over 200 articles in the area of solidification, high-temperature corrosion, and welding metallurgy. John C. Lippold, PhD, is a Professor in the Welding Engineering Program and leader of the Welding and Joining Metallurgy Group at The Ohio State University. A Fellow of both the American Welding Society and ASM International, Dr. Lippold has received numerous awards for his research and teaching, including the Charles H. Jennings Memorial Award, the William Spraragen Memorial Award, the McKay-Helm Award, the James F. Lincoln Gold Medal, the Comfort A. Adams Lecture Award, the Plummer Memorial Education Lecture Award, and the IIW Jaeger Lecture Award. Together with his students and colleagues, he has published over 250 articles on welding metallurgy and weldability of structural materials. Samuel D. Kiser is Director of Technology for the Special Metals Welding Products Co., formerly INCO. He is a professional welding engineer, a Fellow of the American Welding Society, and holds more than ten patents for nickel alloy welding products. Sam is the recipient of the A.F. Davis Silver Medal and the Samuel Wylie Miller Memorial Medal Awards, and has published more than eighty articles and lectured extensively at AWS meetings to audiences around the world.
Local Note:
Electronic reproduction. Ann Arbor, Michigan : ProQuest Ebook Central, 2017. Available via World Wide Web. Access may be limited to ProQuest Ebook Central affiliated libraries.
Genre:
Electronic Access:
Click to View