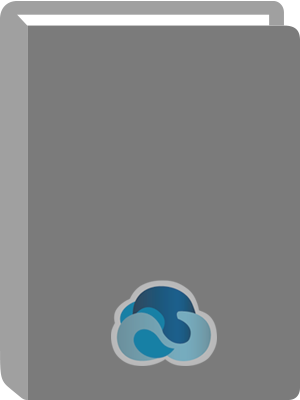
Advances in Modeling and Design of Adhesively Bonded Systems.
Title:
Advances in Modeling and Design of Adhesively Bonded Systems.
Author:
Kumar, S.
ISBN:
9781118754207
Personal Author:
Edition:
1st ed.
Physical Description:
1 online resource (280 pages)
Series:
Adhesion and Adhesives: Fundamental and Applied Aspects Ser.
Contents:
Cover -- Title Page -- Copyright Page -- Contents -- Preface -- Acknowledgements -- 1 Stress and Strain Analysis of Symmetric Composite Single Lap Joints Under Combined Tension and In-Plane Shear Loading -- 1.1 Introduction -- 1.2 Equations and Solution -- 1.2.1 Model Description -- 1.2.2 Governing Equations for Tension Loading Nx -- 1.2.3 Governing Equation for In-Plane Shear Loading Nxy -- 1.2.4 Solutions -- 1.2.4.1 Adhesive Peel Stress azz Due to Nx -- 1.2.4.2 Adhesive Shear Stress axz Due to Nx -- 1.2.4.3 Adhesive Shear Stress ayz Due to Nxy -- 1.3 Solution Verification -- 1.4 Yield Criterion -- 1.5 Case Studies -- 1.6 Summary -- References -- 2 Finite Element Modeling of Viscoelastic Behavior and Interface Damage in Adhesively Bonded Joints -- 2.1 Introduction -- 2.2 Finite Element Analysis of Viscoelastic Adhesively Bonded Joints -- 2.2.1 Constitutive Relation -- 2.2.2 Numerical Example -- 2.2.2.1 Stress Distribution along Overlap Length -- 2.2.2.2 Effect of Thermal Expansion -- 2.3 Damage Analysis of Viscoelastic Adhesively Bonded Joints -- 2.3.1 Constitutive Relation of Cohesive Element -- 2.3.1.1 Linear Elastic Traction-Separation Law -- 2.3.1.2 Damage Initiation and Evolution -- 2.3.2 Numerical Example -- 2.3.2.1 Joint Stiffness -- 2.3.2.2 Damage of Cohesive Elements -- 2.3.2.3 Effects of Interface Damage on Adhesive Layer -- 2.4 Summary and Conclusions -- Acknowledgements -- References -- 3 Modeling of Cylindrical Joints with a Functionally Graded Adhesive Interlayer -- 3.1 Introduction -- 3.2 Axisymmetric Model -- 3.2.1 Stress Fields in the Bonded Assembly -- 3.2.1.1 Inner Adherend -- 3.2.1.2 Adhesive -- 3.2.1.3 Outer Adherend -- 3.2.2 Stiffness Tailored Adhesive Interlayer -- 3.2.2.1 Tubular Joints -- 3.2.2.2 Shaft-Tube Joints -- 3.3 Constitutive Models of the Adherends and FMGB Adhesive -- 3.4 Variational Approach.
3.4.1 Case I: FMGB1 -- 3.4.2 Case II: FMGB -- 3.4.3 Case III: MMB1 -- 3.4.4 Case IV: MMB -- 3.5 Solution Procedure -- 3.6 Results and discussion -- 3.6.1 Influence of Bond Length (L) -- 3.6.2 Influence of Modulus Function -- 3.6.3 Influence of Stiffness Mismatch -- 3.7 Summary -- References -- 4 A Simplified Stress Analysis of Bonded Joints Using Macro-Elements -- 4.1 Introduction -- 4.1.1 Context -- 4.1.2 Objective -- 4.1.3 Overview of the Simplified Linear Elastic Method -- 4.1.4 Overview of the Paper -- 4.2 Linear Elastic 1D-Bar and 1D-Beam Models -- 4.2.1 1D-Bar Model -- 4.2.1.1 Formulation of the BBa Element -- 4.2.1.2 Assembly of the Stiffness Matrix for a Single-Lap Joint -- 4.2.2 1D-Beam Model -- 4.2.2.1 Formulation of the BBe Element -- 4.2.2.2 Validation on the Example Single-Lap Joint -- 4.3 Assuming a Non-linear Adhesive Material -- 4.3.1 Numerical Approach -- 4.3.2 Example of Application to Structures: Single-Lap Joint, In-Plane Loading -- 4.3.2.1 Equilibrium of the Structure -- 4.3.2.2 Determination of the Nodal Residue -- 4.3.2.3 Projected Stresses -- 4.3.2.4 Solution Procedure -- 4.3.3 Considering a Bi-Triangular Damage Evolution Adhesive Behavior -- 4.4 Validation -- 4.4.1 Overview -- 4.4.2 FE Models for a Validation Purpose -- 4.4.2.1 1D-Bar or 1D-Beam FE Models -- 4.4.2.2 3D FE Model Forced for 1D-Bar Analysis -- 4.4.3 1D-Bar Model -- 4.4.3.1 Linear Shear Stress in the Adherends -- 4.4.3.2 Elastic Perfectly Plastic Adhesive Material Behavior -- 4.4.3.3 Elastic Perfectly Plastic and Bi-linear Adhesive Material Behavior with Elastic Unloading -- 4.4.3.4 Bi-triangular Damage Evolution Adhesive Material Behavior with Elastic Unloading -- 4.4.4 1D-Beam Model -- 4.4.4.1 Linear Shear Stress in the Adherends -- 4.4.4.2 Thermal Expansion in the Adherends -- 4.5 Comparison With Finite Element Predictions -- 4.5.1 Overview.
4.5.2 Description of the 3D FE Model -- 4.5.3 Comparison of Results -- 4.5.3.1 Present 1D-Beam Model vs. 3D FE Models -- 4.5.3.2 Evolution of Adhesive Stress Distribution with the Applied Load -- 4.5.4 Assessment of the Relevance of the Model -- 4.6 Conclusion -- Acknowledgment -- References -- 5 Simulation of Bonded Joints Failure using Progressive Mixed-Mode Damage Models -- 5.1 Introduction -- 5.2 Cohesive Damage Model -- 5.3 Measurement of Cohesive Parameters -- 5.3.1 Double Cantilever Beam (DCB) Test -- 5.3.2 End Notched Flexure (ENF) Test -- 5.3.3 Determination of Cohesive Parameters of the Trapezoidal Law -- 5.3.4 Bonded Joints Strength Prediction -- 5.4 Continuum Damage Models -- 5.4.1 Application to DCB Test -- 5.4.2 Application to Single-Lap Joints -- 5.5 Conclusion -- References -- 6 Testing of Dual Adhesive Ceramic-Metal Joints for Aerospace Applications -- 6.1 Introduction -- 6.2 Experimental Details -- 6.2.1 Materials -- 6.2.2 Specimens -- 6.2.3 Static Testing at Low and High Temperature -- 6.2.4 Impact Testing at Room Temperature -- 6.3 Results -- 6.3.1 Static Testing -- 6.3.2 Impact Testing -- 6.4 Conclusions -- Acknowledgments -- References -- 7 Modelling of Composite Sandwich T-Joints Under Tension and Bending -- 7.1 Introduction -- 7.2 Description of the Experiment -- 7.3 Description of the Finite Element Model -- 7.4 Description of the Peel Stress Model: Strength of Materials Approach -- 7.4.1 Tensile Model: Stress Based Assessment -- 7.4.2 Bending Model: Stress Based Assessment -- 7.5 Results and Discussion -- 7.5.1 Experimental Measurement and Finite Element Analysis -- 7.5.2 Peel Stress Analysis: Finite Element and Peel Stress Models -- 7.5.2.1 Tensile Model -- 7.5.2.2 Bending Model -- 7.5.2.3 Limitations of Peel Stress Model -- 7.6 Concluding Remarks -- Acknowledgement -- References.
8 Strength Prediction Methods for Adhesively Bonded Lap Joints between Composite-Composite/Metal Adherends -- 8.1 Introduction -- 8.1.1 Literature on the Stress Analysis of Bonded Joints -- 8.1.1.1 Two-Dimensional Analysis -- 8.1.1.2 Three-Dimensional Solutions -- 8.1.2 Strength Prediction of Bonded Joints -- 8.1.2.1 Elastic Singularities at the Ends of Lap Length -- 8.2 Strength Prediction Using Characteristic Distances in Problems with Singular Stresses -- 8.2.1 Point Stress Criterion -- 8.2.2 Average Stress Criterion -- 8.3 Strength Prediction in Aluminium-Aluminium Joints -- 8.3.1 Experimental Failure Load Determination -- 8.3.2 FE Analysis -- 8.4 Strength Prediction in CFRP-Aluminium and CFRP-CFRP Joints -- 8.4.1 Details of the Experiment -- 8.4.2 FE Analysis of CFRP Composite-Al and CFRP-CFRP Bonded Joints -- 8.5 Results and Discussion -- 8.5.1 Convergence Study of FEA Results -- 8.5.2 Characteristic Distance in Single Lap Adhesively Bonded Joints Using Point Stress Criterion -- 8.6 Conclusions -- Acknowledgments -- References -- 9 Interface Failure Detection in Adhesively Bonded Composite Joints Using a Novel Vibration-Based Approach -- 9.1 Introduction -- 9.2 Conventionally Used Non-destructive Techniques (NDTs) for Damage Detection -- 9.2.1 Ultrasonic -- 9.2.2 Optical Fibers -- 9.2.3 Vibration Signature -- 9.2.4 Lamb Waves -- 9.3 Motivation and Methodology -- 9.3.1 Hilbert-Huang Transform -- 9.3.2 Energy Damage Index (EDI) -- 9.4 Experimental Procedure -- 9.4.1 Specimens Preparation and Description of Damage Cases -- 9.4.2 Test Procedure and Equipment -- 9.5 Experimental Results -- 9.6 Finite Element Modeling Investigation -- 9.6.1 Adhesive Single Lap Joint Model -- 9.6.2 Finite Element Model Verification and Results -- 9.6.2.1 Model Verification -- 9.6.2.2 Disbond Damage in FRP/FRP ABJs -- 9.6.2.3 Disbond Damage in FRP/Aluminum ABJs.
9.6.2.4 Disbond Damage in Aluminum/Aluminum ABJs -- 9.6.2.5 Delamination Damage in ABJs -- 9.7 Summary and Conclusions -- Acknowledgments -- References.
Abstract:
The book comprehensively charts a way for industry to employ adhesively bonded joints to make systems more efficient and cost-effective Adhesively bonded systems have found applications in a wide spectrum of industries (e.g., aerospace, electronics, construction, ship building, biomedical, etc.) for a variety of purposes. Emerging adhesive materials with improved mechanical properties have allowed adhesion strength approaching that of the bonded materials themselves. Due to advances in adhesive materials and the many potential merits that adhesive bonding offers, adhesive bonding has replaced other joining methods in many applications. Containing nine articles written by world-renowned experts, the book deals with the advances in theoretical and computational modeling as well as the design and experimental aspects of adhesively bonded structural systems. Stress analysis and strength prediction of adhesively bonded structural systems, considering a range of material models under a variety of loading conditions, are discussed. Finite element modeling using macro-elements is elaborated on. Recent developments in modeling and experimental aspects of bonded systems with graded adhesive layers and dual adhesives are described. Simulation of progressive damage in bonded joints is addressed. A novel vibration-based approach to detect disbonding and delamination in composite joints is also discussed. Readership The book is central to a range of engineers including mechanical, reliability, construction and surface engineers as well as materials scientists who are engaged in the mechanics of structural adhesive joints. Industries that will use this book include aerospace, electronics, biomedical, automotive, ship building, and construction.
Local Note:
Electronic reproduction. Ann Arbor, Michigan : ProQuest Ebook Central, 2017. Available via World Wide Web. Access may be limited to ProQuest Ebook Central affiliated libraries.
Genre:
Added Author:
Electronic Access:
Click to View