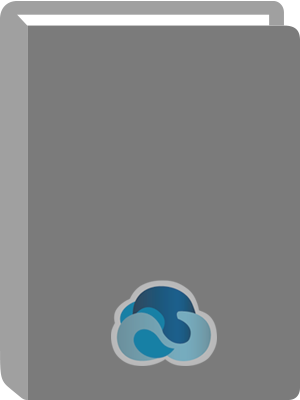
Applied Welding Engineering : Processes, Codes, and Standards.
Title:
Applied Welding Engineering : Processes, Codes, and Standards.
Author:
Singh, Ramesh.
ISBN:
9780123919175
Personal Author:
Physical Description:
1 online resource (374 pages)
Contents:
Front Cover -- Applied Welding Engineering: Processes, Codes and Standards -- Copyright Page -- Contents -- Preface -- Acknowledgment -- 1. Introduction to Basic Metallurgy -- 1. Introduction -- Pure Metals and Alloys -- Smelting -- Iron -- Sponge Iron -- 2. Alloys -- Alloys -- Effects of Alloying Elements -- Carbon Steels -- Sulfur -- Manganese -- Phosphorus -- Silicon -- Alloy Steels -- The Effect of Alloying Elements on Ferrite -- Effects of Alloying Elements on Carbide -- 3. Physical Metallurgy -- Crystal Lattices -- Crystal Structure Nomenclature -- Solidification -- Lever Rule of Solidification -- Constitutional Supercooling -- Elementary Theory of Nucleation -- Allotropy -- Crystal Imperfections -- Grain Size -- 4. Structure of Materials -- Phase Diagrams -- Different Types of Phase Diagrams -- Iron-Iron Carbide Phase Diagram -- Explanation of the Iron-Carbon Phase Diagram -- Rationale for Letter Designations in the Iron-Iron Carbide Phase Diagram -- 5. Production of Steel -- The Electric Arc Furnace (EAF) Process -- Furnace Charging -- Melting -- Refining -- Phosphorus Removal -- Sulfur Removal -- Nitrogen and Hydrogen Control -- De-Slagging -- Tapping -- Basic Oxygen Furnace (BOF) -- Refining Reactions -- Carbon -- Silicon -- Manganese -- Phosphorus -- Sulfur Removal -- Deoxidation of Steel -- Rimmed Steel -- Capped Steel -- Semi-Killed Steel -- Killed Steel -- Deoxidation Equilibria -- The Iron-Iron Carbide Phase Diagram -- 6. Classification of Steels -- Carbon Steels -- Low-Carbon -- Medium-Carbon -- High-Carbon -- Ultrahigh-Carbon -- High-Strength Low-Alloy (HSLA) Steels -- Classification of HSLA -- Low-Alloy Steels -- Low-Carbon Quenched and Tempered Steels -- Medium-Carbon Ultrahigh-Strength Steels -- Bearing Steels -- Chromium-Molybdenum Heat-Resistant Steels -- AISI Series -- Some Examples AISI Classifications -- 7. Cast Iron.
Types of Cast Iron -- White Cast Iron -- Malleable Cast Iron -- Ferritic Malleable Iron -- White Heart Cast Iron -- Black Heart Cast Iron -- Pearlite Malleable Cast Iron -- Martensitic Malleable Iron -- Gray Cast Iron -- Castability of Gray Cast Iron -- Chilled Cast Iron -- Nodular (Spheroidal Graphite) Cast Iron -- Castability, Solidification and Shrinkage -- Alloy Cast Irons -- 8. Stainless Steels -- Stainless Steel Production -- Forming -- Heat Treatment -- Cutting Stainless Steel -- Finishing -- Fabrication of Stainless Steel -- Welding and Joining -- Types of Stainless Steels -- Classification of Stainless Steel -- Martensitic Stainless Steels -- Ferritic Stainless Steels -- Pitting Resistance Equivalent (PRE) -- Austenitic Stainless Steels -- Duplex Stainless Steels -- Precipitation-Hardening (PH) Stainless Steels -- 9. Non-Ferrous Materials -- Copper and Copper Alloys -- Aluminum and Aluminum Alloys -- Physical Metallurgy of Aluminum -- Effect of Alloying Elements on Aluminum -- Effect of Iron -- Effect of Silicon -- Effect of Manganese -- Effect of Magnesium -- Effect of Copper -- Effect of Zinc -- Effect of Chromium -- Effect of Zirconium -- Effect of Lithium -- Age Hardenable Alloys -- Nickel and Nickel Alloys -- Titanium and Titanium Alloys -- 10. Working With Metals -- Elastic Limit -- Plastic Deformation -- Fracture -- Polycrystalline Materials -- Cold Working -- Stored Energy -- Restoring the Lattice Structure of Metal after Cold Work - Annealing -- Grain Growth -- Hot Working -- 11. Mechanical Properties and Testing of Metals -- Strength of Materials -- Elastic and Plastic Behavior -- Ductile vs. Brittle Behavior -- Failure -- Fracture -- Fracture Control -- Crack Growth and Fracture -- Damage Tolerance -- Failure Analysis -- Testing of Metals -- Tensile Test -- Hardness Test -- Impact Test -- Creep Test -- Fatigue Test.
12. Heat Treatment of Steels -- TTT and CCT Curves -- Isothermal-Transformation (IT) or (TTT) Diagrams -- Cooling Curves -- Cooling-Transformation (C-T) Diagrams -- Stress Relief Annealing -- Normalizing -- Annealing -- Spheroidizing -- Tempering -- Austempering of Steels -- Martempering -- Hardening -- Hardening by Martensite Transformation -- Case Hardening and Carburizing -- Process of Quenching -- Heat Treatment of Non-Ferrous Material -- Heat Treatment of Copper and Copper Alloys -- Heat Treating Aluminum and its Alloys -- Heat-Treating Furnaces -- Liquid Heating Baths -- 2. Welding Metallurgy and Welding Processes -- 1. Introduction -- Welding Procedures -- 2. Physics of Welding -- Heat -- Details of the Heat-Flow in Welding -- Heat in Arc Welding Processes -- Heat in Plasma Arc Cutting and Welding -- Heat in Resistance Welding -- Heat in Electroslag Welding (ESW) -- Heat in Welding Processes using Chemical Sources -- Thermit Welding -- Heat Generated by Mechanical Processes -- Friction Welding -- Ultrasonic Welding -- Explosion Welding -- Heat by Focused Sources -- Laser Beam Welding (LBW) -- Electron Beam Welding (EBW) -- Other Sources of Heat in Welding -- Application of the Principles of Welding Physics -- Pre-Heating -- Determining the Need for Pre-Heat and the Temperature -- Post-Weld Heat Treatment (PWHT) -- Heat and Time in Welding -- Heat Input -- Energy Distribution -- Rate of Heating -- Maximum Temperature -- Heat Generation and Temperature Distribution - Practical Application -- Time at Temperature -- Cooling Rates -- Base Metal Mass -- 3. Welding and Joining Processes -- Shielded Metal Arc Welding (SMAW): Process Fundamentals -- How the Process Works -- Covered Electrodes Used in the SMAW Process -- Joint Design and Preparation -- Gas Tungsten Arc Welding (GTAW): Process Description -- Process Advantages and Limitations.
Electrodes -- Joint Design -- Gas Metal Arc Welding (GMAW) -- Process Description -- Electrode Selection -- Joint Design -- Flux Cored Arc Welding (FCAW) -- Process Fundamentals -- Principal Applications of FCAW -- Shielding Gases -- Electrodes -- Submerged Arc Welding (SAW) -- Process Description -- Materials -- Other Common Joining and Welding Processes -- Electroslag Welding (ESW) -- Plasma Arc Welding (PAW) -- Stud Welding -- Oxy-fuel Gas Welding (OFW) -- Brazing and Soldering -- Arc-Welding Power Sources -- Constant Voltage Power Source -- Constant-Current Power Source -- Transformers -- Thyristor-Silicon Controlled Rectifiers (SCR) -- Generators -- Alternators -- 4. Physical Effect of Heat on Material During Welding -- The Molten Metal -- The Welded Plate -- Influence of Cooling Rate -- 5. Stresses, Shrinkage and Distortion in Weldments -- Stresses in Weldments -- Definitions of Terms -- Development of Stresses -- Moving a Localized Heat Source -- Distribution of Stress in a Simple Weld -- Residual Stresses -- Shrinkages -- Shrinkage Transverse to a Butt Weld -- Shrinkage Longitudinal to a Butt Weld -- Distortion in Weldments -- General Description -- Angular Distortion -- Longitudinal Bowing -- Buckling -- Corrective Measures -- Thermal Straightening -- Designing Weld Joints -- Assessing the Strength of Welds -- Throat of a Weld -- Sizing a Fillet Weld -- Stress Causing Fatigue in Weld -- Weld Size and Cost Control -- Control of Welding Stresses to Minimize Through-Thickness Failures -- 6. Welding Corrosion Resistant Alloys - Stainless Steel -- Corrosion Resistant Alloys (CRAs) -- Stainless Steel -- Welding Stainless Steel -- General Welding Characteristics -- Welding Processes -- Protection against Oxidation -- Welding Hygiene -- Austenitic Stainless Steels -- Metallurgical Concerns Associated with Welding Austenitic Stainless Steels.
Mechanical Properties of Stainless Steels -- Welding of Austenitic Stainless Steels -- Superaustenitic Stainless Steels -- Material Properties and Applications -- Welding and Joining of Superaustenitic Stainless Steels -- Difficulties Associated with Welding Stainless Steel -- Martensitic Stainless Steels -- Properties and Application -- Welding Martensitic Stainless Steels -- Ferritic Stainless Steels -- Properties and Application -- Welding Ferritic Steel -- Precipitation Hardened Stainless Steels -- Properties and Application of Precipitation Hardened Steels -- Welding Precipitation Hardened (PH) Steels -- Duplex Stainless Steels -- Mechanical Properties -- Heat Treatment -- Welding and Fabrication -- 7. Welding Non-Ferrous Metals and Alloys -- Aluminum and its Alloys -- The Confusing Thing about Aluminum -- Weld Hygiene -- Preheating -- The Conductivity of Heat -- Welding Filler Metals -- Welding Aluminum with the Shield Metal Arc Welding (SMAW) process -- Welding Aluminum with the Gas Tungsten Arc Welding (GTAW) process -- Type of Current and Electrode -- Grinding the Tip of the Electrodes -- Welding Aluminum with the Gas Metal Arc Welding (GMAW) Process -- Power Source -- Wire Feeder -- Welding Guns -- Welding Technique -- The Push Technique -- Travel Speed -- Shielding Gas -- Welding Wire -- Friction Stir Welding (FSW) -- Nickel Alloys -- Heat Treatment -- Mechanical Properties -- Fabrication -- Precipitation Hardenable Nickel-Based Alloys -- Heat Treatment of PH Nickel Alloys -- Mechanical Properties -- Welding -- Titanium Alloys -- Heat Treatment -- Alpha (α) Titanium -- Alpha/beta (α-β) Titanium -- Beta (β) Titanium -- 8. Weld Defects and Inspection -- Weld Quality -- Acceptance Standards -- Discontinuities in Fusion Welded Joints -- Classification of Weld Joint Discontinuities -- Typical Weld Defects -- Porosity -- Inclusions.
Incomplete Fusion.
Abstract:
While there are several books on market that are designed to serve a company's daily shop-floor needs. Their focus is mainly on the physically making specific types of welds on specific types of materials with specific welding processes. There is nearly zero focus on the design, maintenance and troubleshooting of the welding systems and equipment. Applied Welding Engineering: Processes, Codes and Standards is designed to provide a practical in-depth instruction for the selection of the materials incorporated in the joint, joint inspection, and the quality control for the final product. Welding Engineers will also find this book a valuable source for developing new welding processes or procedures for new materials as well as a guide for working closely with design engineers to develop efficient welding designs and fabrication procedures. Applied Welding Engineering: Processes, Codes and Standards is based on a practical approach. The book's four part treatment starts with a clear and rigorous exposition of the science of metallurgy including but not limited to: Alloys, Physical Metallurgy, Structure of Materials, Non-Ferrous Materials, Mechanical Properties and Testing of Metals and Heal Treatment of Steels. This is followed by self-contained sections concerning applications regarding Section 2: Welding Metallurgy & Welding Processes, Section 3: Nondestructive Testing, and Section 4: Codes and Standards. The author's objective is to keep engineers moored in the theory taught in the university and colleges while exploring the real world of practical welding engineering. Other topics include: Mechanical Properties and Testing of Metals, Heat Treatment of Steels, Effect of Heat on Material During Welding, Stresses, Shrinkage and Distortion in Welding, Welding, Corrosion Resistant Alloys-Stainless Steel, Welding Defects and Inspection, Codes,
Specifications and Standards. The book is designed to support welding and joining operations where engineers pass plans and projects to mid-management personnel who must carry out the planning, organization and delivery of manufacturing projects. In this book, the author places emphasis on developing the skills needed to lead projects and interface with engineering and development teams. In writing this book, the book leaned heavily on the author's own experience as well as the American Society of Mechanical Engineers (www.asme.org), American Welding Society (www.aws.org), American Society of Metals (www.asminternational.org), NACE International (www.nace.org), American Petroleum Institute (www.api.org), etc. Other sources includes The Welding Institute, UK (www.twi.co.uk), and Indian Air force training manuals, ASNT (www.asnt.org), the Canadian Standard Association (www.cas.com) and Canadian General Standard Board (CGSB) (www.tpsgc-pwgsc.gc.ca). Rules for developing efficient welding designs and fabrication procedures Expert advice for complying with international codes and standards from the American Welding Society, American Society of Mechanical Engineers, and The Welding Institute(UK) Practical in-depth instruction for the selection of the materials incorporated in the joint, joint inspection, and the quality control for the final product.
Local Note:
Electronic reproduction. Ann Arbor, Michigan : ProQuest Ebook Central, 2017. Available via World Wide Web. Access may be limited to ProQuest Ebook Central affiliated libraries.
Genre:
Electronic Access:
Click to View