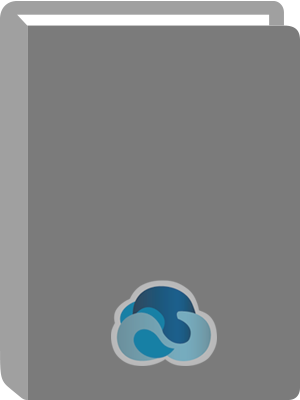
The Investigation of energy absorption characteristics of TPU TPMS structures subjected to impact loading
Başlık:
The Investigation of energy absorption characteristics of TPU TPMS structures subjected to impact loading
Yazar:
Bakıcı, Çetin, author.
Yazar Ek Girişi:
Fiziksel Tanımlama:
xii, 106 leaves: charts;+ 1 computer laser optical disc
Özet:
In this thesis, the energy absorption capability of a schwarz based TPMS structure both experimentally and numerically was invetigated. In the product, TPU material and FDM printer was used. Instead of the regular schwarz primitive cell structure, which has been frequently examined in the literature, the sandwich structure design was prepared with the geometry selected from the region between two cells was used and its advantages were compared. In the selection of the TPMS structure, both its high energy absorption capability per unit weight and its geometry suitable for mass production in the future was important. A hyperelastic material TPU and a printer suitable for its production were selected to show deformation behaviour of the structure against multiple loading. After material characterization with TPU specimens, the determined printer parameters were kept constant, and single and multiple cell structures were produced. Static and dynamic tests were performed, and single and multiple-cell structures were modeled and validated in the LS-DYNA finite element package program. It was observed that as the strain rate increases, the structures densification point also decreased and the first peak force and the energy absorption per unit weight (SAE) increase. In addition, it was observed that the deformation behaviour of single and multiple-cell structures were rate dependent. It has been observed that the structure with 9 cells absorbs 20% more energy than the structure with unit cell, which is 9 times higher than the unit cell structure due to the interaction of cells. The developed structure was numerically exposed to blast loads following Nato Stanag 4569 standart. In this standart, from the defined of the injury criteria,on the lower and upper tibia joint should experienced force values lower than 2.6 kN and 5.4 kN respectively. From the numerial simulations, it was found that the structure was able to mitigate the blast load transmitted to the during the accaptable limits.
Yazar Ek Girişi:
Tüzel Kişi Ek Girişi:
Tek Biçim Eser Adı:
Thesis (Master)--İzmir Institute of Technology: Mechanical Engineering.
İzmir Institute of Technology: Mechanical Engineering--Thesis (Master).
Elektronik Erişim:
Access to Electronic Versiyon.