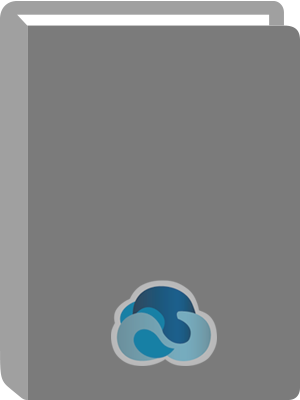
Vision-based monitoting and control of fiber laser welding
Başlık:
Vision-based monitoting and control of fiber laser welding
Yazar:
Tavkaya, Emre, author.
Yazar Ek Girişi:
Fiziksel Tanımlama:
xi, 90 leaves:+ 1 computer laser optical disc.
Özet:
Laser welding is an advanced emission process that applies the converted laser beam energy to join pieces by melting and welding them together. Fiber lasers, with their high efficiency, continuous wave and shorter wavelength, are mostly useful for deep penetration welding of materials. To avoid the defects in an automated fiber laser welding process such as pores, cracks or blow-out holes and to make the welding process controllable, off-line pre-process is required. Tuning welding parameters is critical during this stage since modeling of the process is hard and parameters change with respect to material and thickness. Therefore, real-time control of the laser welding becomes a challenge due to uncertainties in the process. A solution to such problem could be a vision-based monitoring and control system, which uses a path modification algorithm that matches CAD-based (Computer Aided Design-based) path data to target path before welding. In this thesis, a vision-based path modification algorithm is developed to determine the orientation of target welding path. Two subsystems are used in this developed technique including; a machine vision system and a CNC system. These subsystems are integrated through developed vision algorithm and subroutine logic of CNC system by calculating laser spot position on workpiece during operation. As a result of implemented technique, welding path modification data is stored as a CNC subprogram (file) under the CNC main program so that operational modification is made without the need of any change on the main CNC program. The proposed method is experimentally tested to assess the performance of the monitoring and control technique on line and curve welding paths for mild steel and stainless steel materials with two different material thicknesses. The accuracy of the measurements is carried out by comparing the measured and computed offset values that are exported from the vision algorithm with reference to effective laser beam diameter. The results of tests indicate that the vision system accuracy varies between %85 and %95 for 600 micron effective laser beam size. For thinner materials less than 1 millimeter, due to smaller effective laser beam size requirements, system performance is found to be decreased down to %58-70 as a result of 400 micron effective laser beam size.
Yazar Ek Girişi:
Tüzel Kişi Ek Girişi:
Tek Biçim Eser Adı:
Thesis (Master)--İzmir Institute of Technology: Mechanical Engineering.
İzmir Institute of Technology: Mechanical Engineering--Thesis (Master).
Elektronik Erişim:
Access to Electronic Versiyon.