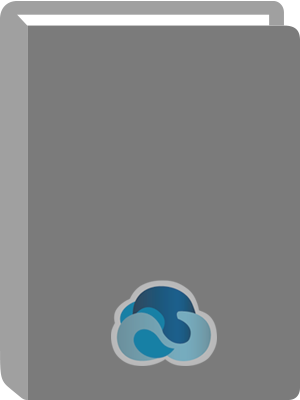
Flexible Manufacturing System.
Başlık:
Flexible Manufacturing System.
Yazar:
Shivanand, H.K.
ISBN:
9788122425598
Yazar Ek Girişi:
Basım Bilgisi:
1st ed.
Fiziksel Tanımlama:
1 online resource (165 pages)
İçerik:
Cover -- Foreword -- Preface -- Acknowledgement -- Contents -- Chapter 1 FMS Introduction and Description -- 1.1 Introduction -- 1.2 Definition -- 1.3 Basic Components of FMS -- 1.4 The Significance of FMS in the 1990s -- 1.5 Different Types of FMS -- 1.6 Types of FMS Layouts -- 1.6.1 Factors Influencing the FMS Layouts -- 1.6.2 Seeking Benefits on Flexibility -- 1.7 FMS-An Example of Technology and an Alternative Layout -- 1.8 Objectives of an FMS -- 1.9 AIMS of FMS -- 1.10 The Principle Objectives of FMS -- 1.11 Advantages and Disadvantages of FMS Implementation -- 1.11.1 Advantages -- 1.11.2 Disadvantages -- 1.12 Area of Application of a FMS in Industry -- 1.13 Various Equipments and Their Functions Required for an FMS -- 1.14 Innovations that have Advanced the Manufacturing Industries -- 1.15 CIM Technology -- 1.16 Hierarchy of CIM -- 1.17 Direct Real Time Schedule Control -- 1.18 FMS Concepts -- Chapter 2 Manufacturing Cell -- 2.1 Introduction -- 2.1.1 Definition of Cell -- 2.2 Classification of Cell -- 2.2.1 Standalone NC Machine Tools -- 2.2.2 Single NC Machine Cell or Mini Cell -- 2.2.3 Integrated Multi Machine Cell -- 2.2.4 Flexible Manufacturing System -- 2.3 Unattended Machining -- 2.3.1 Features and Requirement -- 2.4 Defferences Between FMC and FMS -- Chapter 3 JIT and KANBAN System -- 3.1 Introduction -- 3.2 Definition -- 3.2.1 Big JIT -- 3.2.2 Little JIT -- 3.3 JIT Concept -- 3.4 Goals of JIT -- 3.4.1 Waste of Over Productions -- 3.4.2 Waste of Waiting -- 3.4.3 Waste of Transportation -- 3.4.4 Waste of Processing -- 3.4.5 Waste of Stock -- 3.4.6 Waste of Motion -- 3.4.7 Waste of Making Defective Parts -- 3.5 What JIT Really Is? -- 3.6 Objectives of JIT -- 3.7 Ingredients of JIT -- 3.8 Quality and Quantity Principles of JIT -- 3.9 The Primary Quantity JIT Principles -- 3.10 Benefits of JIT -- 3.11 JIT Implementation.
3.12 Kanban/Card System -- 3.12.1 Introduction -- 3.13 What is Kanban? -- 3.14 Push vs. Pull System -- 3.15 Types of Kanban -- 3.15.1 Dual-Card Kanban -- 3.15.2 Single-Card Kanban -- Chapter 4 Group Technology -- 4.1 Introduction -- 4.2 Definition -- 4.3 Reasons for Adopting Group Technology -- 4.3.1 Visual Inspection -- 4.3.2 Part Classification and Coding -- 4.3.3 Production Flow Analysis -- 4.4 Benefits of Group Technology Affecting Many Areas of a Company -- 4.5 Obstacles to Application of GT -- Chapter 5 Machining Centers -- 5.1 Introduction -- 5.2 Types of Machining Centers -- 5.2.1 Machining Center Innovations and Developments have Brought About the Following Improvements -- 5.3 Machining Centers -- 5.3.1 Axes and Format Information -- 5.3.2 Merits of Horizontal Machining Center -- 5.3.3 Demerits of Horizontal Machining Center -- 5.3.4 Merits of Vertical Machining Center -- 5.3.5 Demerits of Vertical Machining Center -- 5.3.6 Automated Features and Capabilities of Machining Center -- Chapter 6 Deburring and Wash Stations -- 6.1 Introduction -- 6.2 Deburring -- 6.2.1 Mechanical Deburring -- 6.2.2 Vibratory Deburring -- 6.2.3 Thermal Deburring -- 6.2.4 Electrochemical Deburring -- 6.3 Wash Stations -- 6.3.1 Classification of Wash Stations -- 6.4 Importance to Automated Manufacturing -- Chapter 7 Coordinate Measuring Machine -- 7.1 Introduction -- 7.2 CMM Construction -- 7.2.1 Probe -- 7.2.2 Mechanical Structure -- 7.3 Types of CMM -- 7.4 Functions of CMM Computer -- 7.5 Operational Cycle Description -- 7.6 CMM Applications -- 7.7 CMM Advantages -- Chapter 8 Automated Material Movement and Storage System -- 8.1 Introduction -- 8.2 Types of AGVS -- 8.2.1 Unit Load Carries: Low Built Vehicle 3 Types A and C -- 8.2.2 Side Loading and High Lifting Types -- 8.2.3 Tugger Systems -- 8.2.4 Automated Guided Transport Carts -- 8.3 ASRS Systems Available.
8.4 Analysis of AGV Systems -- 8.6 Automated Storage and Retrieval Systems (AS/RS) -- 8.6.1 Unit Load AS/RS -- 8.6.2 Mini Load AS/RS -- 8.6.3 Carousel AS/RS -- 8.7 Advanced Automated Storage and Retrieval System -- 8.8 Analysis of AS/RS -- 8.9 Quantitative Analysis -- 8.10 Industrial Robots -- 8.10.1 Definition of an Industrial Robot -- 8.10.2 Basic Components of a Robotic System -- 8.10.3 Types of Robots -- 8.10.4 ROBOTIC ARMS -- 8.10.5 Basic Configurations Are -- 8.10.6 Applications of Industrial Robots -- Chapter 9 Cutting Tools and Tool Management -- 9.1 Introduction -- 9.2 Tool Management -- 9.2.1 Tool Room Service -- 9.2.2 Tool Delivery -- 9.2.3 Tool Allocation and Data Flow -- 9.2.4 Fault Sensing -- 9.3 Tool Strategies -- 9.3.1 Mass Exchange -- 9.3.2 Tool Sharing -- 9.3.3 Tool Migration -- 9.3.4 Assigned Tools -- 9.4 Tool Preset, Identification and Data Transfer -- 9.4.1 Bar Code Scanning -- 9.4.2 Machine Vision -- 9.4.3 Radio Frequency Identification -- 9.4.4 Optical Character Recognition -- 9.4.5 The Microchip -- 9.5 Data Transfer -- 9.6 Tool Monitoring and Fault Detection -- 9.7 Experimental Setup and Data Collection -- 9.7.1 The Need -- 9.7.2 Monitoring Model Derivation -- 9.7.3 Monitoring by Sensors -- Chapter 10 System Hardware and General Functionality -- 10.1 Introduction -- 10.2 Programmable Logic Controllers -- 10.3 Cell Controllers -- 10.4 Communication Networks -- 10.5 Networks -- 10.5.1 Star or Radial -- 10.5.2 Ring or Loop -- 10.5.3 Bus -- Chapter 11 FMS Software Structure, Functions and Description -- 11.1 Introduction -- 11.2 General Structure and Requirements -- 11.3 Advantages of Modular Software Design and Development -- 11.4 Activities and Functions to be Performed by FMS Software, Within The System -- 11.5 Requirements of FMS Software -- 11.6 Types of FMS Software Modules -- 11.6.1 Work-Order Processing.
11.6.1.1 The Objectives -- 11.6.2 Data Distribution and Collection -- 11.6.3 System Diagnostics and Maintenance -- 11.6.4 Tool Management -- 11.6.5 Traffic Management and Control -- 11.6.6 Quality Control Management -- 11.6.7 Fixtures and Workpiece Control -- 11.6.8 Planning Scheduling and Simulation -- 11.6.9 Computer Simulation -- 11.7 General Phases of Simulation Analysis -- 11.8 Reasons to Integrate FMS Computer System to a Central Host Computers -- 11.9 Functions of an FMS Host Computer -- 11.10 The Major FMS Host Functions -- 11.11 FMS Master Host Tasks -- 11.12 Subordinate FMS Host Tasks -- 11.13 Area Controller Host Tasks -- 11.14 Data Exchanges -- Chapter 12 FMS Installation and Implementation -- 12.1 FMS Installation -- 12.1.1 Introduction -- 12.1.2 System Installation -- 12.2 FMS Implementation -- 12.2.1 Introduction -- 12.2.2 Acceptance Testing -- Chapter 13 Case Studies -- 13.1 Case I : The Toyota Production System -- 13.1.1 Automobile Manufacturing -- 13.1.2 Toyota Production System -- 13.1.3 Production Methods -- 13.1.4 Toyota Production System -- 13.1.5 Just-in-Time Production -- 13.1.6 Kanban System -- 13.1.7 Autonamation -- 13.2 Case II : General Motors Leverages Common Architecture to Strategic Advantage -- 13.2.1 Executive Overview -- 13.2.2 GM Corporate Mantra -- 13.2.3 Common Engineering Benefits New Initiatives -- 12.2.4 Common Processes Accelerate Time-to-Market -- 13.2.5 Common Manufacturing Systems Lower Costs -- 13.2.6 Common Manufacturing Systems Improve Production Efficiency and Lower Costs -- 13.2.7 Common Controls Architecture Lies at the Foundation of GM NA.s Strategy -- 13.2.8 GM NA.s Common Control System Architecture -- 13.2.9 Components Contribute to the Bottom Line Common -- 13.2.10 Implementation and Validation Team -- 13.2.11 Common Networks -- 13.2.12 Common Control Panels -- 13.2.13 Common HMI.
13.2.14 A Common Goal: Connecting the Plant Floor with Business System -- 13.2.15 Common Controls Architecture Enables Collaborative Manufacturing -- 13.2.16 Acronym Reference -- 13.3 Case III : The Rover LM-500 FM S -- 13.3.1 Introduction -- 13.3.2 The FMS Layout Incorporate -- 13.3.3 The FMS Host Control -- 13.3.4 Control of the Automatic Clamping Area -- 13.4 Case IV : The HNH (Hattersley Mewman Hender)FMS -- 13.4.1 The System Layout and Facilities -- 13.4.2 HNH Secondary Facilities -- 13.4.3 Production Strategy -- Bibliography.
Özet:
About the Book: The book is intended to serve as a textbook for the final and pre-final year B.E., B.Tech. and M.Tech. students of Mechanical, Production, Manufacturing, Computer Integrated Manufacturing, Automobile Engg., disciplines. This book can be used in industries, technical training institutes. This covers the main areas of interest in flexible manufacturing namely automation, flexible cells, workstation, AGV?s, AS/RS etc. Separate chapters have been devoted to the important topics. This book emphasizes the basic principles of working and the applications of a wide range of manufacturing, flexibility, devices and machines. It also reveals the constructions and principles of working of the mechanisms, devices, layouts, automation through coloured sketches and most simple explanations. It offers simple and systematic working principles and techniques in the different topics of the various chapters. Contents: FMS Introduction and Description Manufacturing Cell JIT and KANBAN System Group Technology Machining Centers Deburring and Wash Stations Coordinate Measuring Machines Automated Material Movement and Storage System Cutting Tools and Tool Management System Hardware and General Functionality FMS Software Structure, Functions and Description Case Studies.
Notlar:
Electronic reproduction. Ann Arbor, Michigan : ProQuest Ebook Central, 2017. Available via World Wide Web. Access may be limited to ProQuest Ebook Central affiliated libraries.
Tür:
Elektronik Erişim:
Click to View