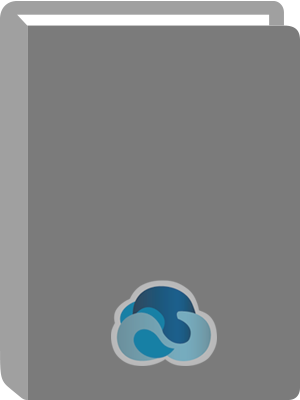
Advanced Automation Techniques in Adaptive Material Processing.
Başlık:
Advanced Automation Techniques in Adaptive Material Processing.
Yazar:
Chen, Xiaoqi.
ISBN:
9789812777775
Yazar Ek Girişi:
Fiziksel Tanımlama:
1 online resource (321 pages)
İçerik:
Contents -- Preface -- Chapter 1 Overview of Material Processing Automation -- 1. Constrained and Non-Constrained Material Processing -- 2. Multi-Facet Mechatronic Automation -- 3. Sensors for Material Processing -- 3.1 Measurands in Material Processing -- 3.2 Types of Sensors -- 3.3 Microsensors and Soft Sensors -- 4. Intelligent Control Techniques -- 4.1 Conventional Computer Numerical Control -- 4.2 Sensor Based Machine Tool Control -- 4.3 Open Architecture and Distributed Control -- 4.4 Intelligent Control and Computing Techniques -- 4.5 Human-Machine Interface -- References -- Chapter 2 Process Development and Approach for 3D Profile Grinding/Polishing -- 1. Introduction -- 2. Profile Grinding and Polishing of Superalloys -- 2.1 Superalloy Components and Manual Blending -- 2.2 CNC Milling -- 2.3 Wheel Grinding -- 3. Force Control in Material Removal -- 3.1 Robot Holding Tool -- 3.2 Robot Holding Workpiece -- 4. Model-Based Robotic Machining -- 5. Part Variations and Process Dynamics -- 6. System Concept of Adaptive Robotic Blending System -- 6.1 A Mechatronic Approach -- 6.2 Device and Process -- 6.3 Knowledge-Based Process Control (KBPC) -- 6.4 Data-Driven Supervisory Control (DDSC) -- 6.5 System Layout and Working Cycle -- 7. Process Optimisation -- 7.1 Grinding/Polishing Process Parameters -- 7.2 Tool Path Optimisation -- 7.3 Tool Wear Compensation -- 8. Concluding Remarks -- References -- Chapter 3 Adaptive Robotic System for 3D Profile Grinding/Polishing -- 1. Introduction -- 2. Finishing Robot and Control Interface -- 2.1 Finishing Robot -- 2.2 Self-Aligned End Effector -- 2.3 Control Interface -- 3. In-Situ Profile Measurement -- 3.1 Off-Line versus In-Situ Approach -- 3.2 Sensor Techniques -- 3.3 Coordinate Transform -- 4. Template-Based Optimal Profile Fitting -- 4.1 Template Generation.
4.2 Profile Fitting Requirements -- 4.3 A Fast Converging Minimisation Algorithm -- 4.4 Software Development -- 5. Adaptive Robot Path Planner -- 5.1 Definition of Tool Path -- 5.2 Derivation of End-Effector Orientation -- 5.3 Generation of Tool Path -- 6. Implementation of SMART 3D Blending System -- 7. Results -- 7.1 Dimension of Finish Profile -- 7.2 Surface Roughness and Finish Quality -- 7.3 Wall Thickness -- 8. Concluding Remarks -- References -- Chapter 4 Acoustic Emission Sensing and Signal Processing for Machining Monitoring and Control -- 1. Introduction -- 2. Sensors in Machining Process Monitoring -- 2.1 Motor Current & Power -- 2.2 Force/Torque -- 2.3 Vibration/Acceleration Signals -- 2.4 Optical and Vision System -- 3. Acoustic Emission Sensing -- 3.1 Acoustic Emission Mechanism -- 3.2 Acoustic Emission in Machining -- 3.3 Acoustic Emission Sensors -- 4. Advanced Signal Processing Techniques -- 4.1 Time Domain Analysis -- 4.2 Time Series Modelling -- 4.3 Frequency Domain Analysis -- 4.4 Time-Frequency Domain Analysis -- 4.5 Wavelet Analysis -- 5. Conclusions -- References -- Chapter 5 Techniques of Automatic Weld Seam Tracking -- 1. Introduction to Weld Seam Tracking -- 1.1 The Importance of Welding -- 1.2 What is Welding? -- 1.3 Automated Welding -- 1.4 Need for Seam Tracking -- 2. Through-the-Arc Sensing -- 2.1 Survey of Existing Methods -- 2.2 System Overview -- 2.3 Data Acquisition -- 2.4 Signal Processing -- 2.5 Robotic Welding System -- 2.6 Implementation of Seam Tracking Controller -- 2.6.1 The Algorithm -- 2.6.2 The PID Controller -- 2.7 Plant Identification and Control -- 3. Vision-Based Seam Tracking -- 3.1 The Technology -- 3.1.1 Triangulation Techniques -- 3.1.2 Measurement Range and Accuracy -- 3.1.3 The Principle of Laser Triangulation -- 3.2 Vision Based Seam Tracking Systems.
3.2.1 System Architecture -- 3.2.2 Vista Weld Laser Camera -- 3.2.3 Two Beam Laser Camera -- 3.2.4 Laser 3D Vision Sensor -- 3.2.5 Point Laser Scanner -- 3.2.6 Laser Camera -- 3.2.7 Fanuc's MIG EYE -- 3.3 System Description -- 3.3.1 Hardware-System Layout -- 3.3.2 Sensor Hardware -- 3.3.3 Mounting of Sensor Head -- 3.3.4 Data Acquisition System -- 3.3.5 Software Overview -- 3.4 Image Acquisition and Processing -- 3.4.1 Structured Light Approach -- 3.4.2 Capturing the Image -- 3.4.3 Image Preprocessing -- 3.4.4 Erosion -- 3.4.5 Blobs Tool Control -- 3.5 Seam Detection Algorithms -- 3.6 Implementation and Experimental Results -- 3.6.1 Evaluating Accuracy of Seam Tracking -- 3.6.2 Evaluating the Overall Accuracy -- 4. Concluding Remarks -- References -- Chapter 6 Weld Pool Geometry Sensing and Control in Arc Welding -- 1. Introduction -- 2. Survey of Weld Pool Inspection -- 2.1 Weld Pool Oscillation -- 2.1.1 Sensing Principle -- 2.1.2 Theoretical Models -- 2.1.3 Pool Oscillation Detection -- 2.1.4 Results -- 2.1.5 Disadvantages -- 2.2 Ultrasound -- 2.2.1 Contact Transducer -- 2.2.2 Laser Array and EMAT Ultrasonic Measurement -- 2.3 Infrared Sensing -- 2.3.1 Theoretical Foundations -- 2.3.2 Infrared Sensing Technology -- 2.3.3 Results -- 2.3.4 Limitation -- 2.4 Surface Depression Sensing -- 2.4.1 Background -- 2.4.2 Sensing Technology -- 2.4.3 Image Processing -- 2.4.4 Results -- 2.4.5 Disadvantages -- 3. Weld Pool Vision and Control System -- 3.1 Controlled Welding Process -- 3.2 Weld Pool Vision System -- 3.3 Set-Up of Weld Pool Vision and Control System -- 4. Weld Pool Geometry Extraction -- 4.1 Real-Time Weld Pool Geometry Extraction -- 4.2 Edge Detection -- 4.3 Connectivity Analysis -- 4.4 Relationship between Weld Pool Dimensions and Welding Parameters -- 5. Neurofuzzy Logic Control -- 5.1 Fuzzy Logic Control.
5.2 Neurofuzzy Logic System -- 5.3 System Optimisation and Integration -- 6. Results -- 6.1 Simulation Results of Neurofuzzy Logic Control System -- 6.2 Closed-Loop Control of Welding Speed -- 7. Conclusions -- References -- Chapter 7 Automatic GTAW System Control and Teleoperation -- 1. Introduction - The Automatic Welding of High Performance Alloys -- 2. Special Considerations for Welding Titanium -- 2.1 GTAW for Titanium -- 2.2 Features of an Intelligent Welding System -- 2.3 Subsystems and Components -- 3. Manipulator Configuration -- 3.1 Selection of Axes -- 3.2 The Experimental and Demonstration Welding Manipulator -- 3.3 Machine Kinematics -- 3.3.1 Assigning Coordinate Frames -- 3.3.2 Kinematic Simulation -- 3.3.3 Inverse Kinematics -- 3.3.4 Trajectory by Decomposition of Tool Transformation Matrix -- 4. Process Control -- 4.1 Critical Process Parameters -- 4.2 Inert Gas Shielding -- 4.3 Other Procedures -- 4.4 Sensing and Monitoring -- 4.5 Schemes for Process Control -- 4.6 Use of AI in Automatic Welding -- 5. CNC and Low-Level Control -- 6. Interactive and Tele-Operated Welding System -- 6.1 Visual Monitoring -- 6.2 Computer Enhanced Vision -- 6.2.1 Modelling of Camera Views -- 6.2.2 Modelling of Solid Objects -- 6.2.3 Implementation in Simulation Software -- 6.2.4 Integration of Models and Welding Workpiece Images -- 7. Conclusions -- References -- Chapter 8 Laser Material Processing and Its Quality Monitoring and Control -- 1. Introduction -- 1.1 Laser Equipmentm -- 1.2 Applications of Laser Material Processing -- 1.3 Automation of Laser Material Processing -- 1.3.1 In-Process Monitoring -- 1.3.2 In-Process Control -- 2. Survey of Real-Time Laser Welding Quality Monitoring -- 2.1 Acoustic Emission -- 2.2 Audible Sound -- 2.3 Infrared Sensing -- 2.4 Ultraviolet Sensing.
2.4.1 Ultraviolet Spectroscopic Analysis -- 2.4.2 Ultraviolet Signal Analysis -- 3. Analysis of Optical and Acoustic Signals Emitted from Plasma and Sensor Design -- 3.1 Laser-Induced Plasma During Welding of Thin Metal Sheets -- 3.2 Optical Emission from Laser-Induced Plasma -- 3.3 Waves in Plasma -- 3.4 Design of Optical and Acoustic Sensors -- 4. Signal Processing through FFT and Wavelet Analysis -- 4.1 FFT Analysis -- 4.1.1 Frequency Characteristics of Optical and Acoustic Signals Using Magnetically Restrained Discharge Laser -- 4.1.2 Frequency Characteristics of Optical and Acoustic Signals of Differnet Defects -- 4.2 Wavelet Analysis of Audible Acoustic Emission Signals -- 4.2.1 Wavelet Decomposition of AE Signals -- 4.2.2 Results of Wavelet Analysis of AE Signal -- 4.3 Definition and Applications of Detection Curve -- 4.3.1 Definition of Detection Curve -- 4.3.2 Example -- 5. Real-Time Monitoring of Laser Welding by ANN -- 5.1 Structure of the Neural Network -- 5.1.1 Construction of Features -- 5.1.2 Improvement of Features -- 5.1.3 BP Network Parameters and Effect of Different Features -- 5.2 Performance of the Neural Network -- 5.3 Discussion -- 6. Conclusions -- References -- INDEX.
Özet:
This volume presents the editors' research as well as related recent findings on the applications of modern technologies in electrical and electronic engineering to the automation of some of the common manufacturing processes that have traditionally been handled within the mechanical and material engineering disciplines. In particular, the book includes the latest research results achieved through applied research and development projects over the past few years at the Gintic Institute of Manufacturing Technology, Singapore. It discusses advanced automation technologies such as in-process sensors, laser vision systems, and laser strobe vision, as well as advanced techniques such as sensory signal processing, adaptive process control, fuzzy logic, neural networks, expert systems, laser processing control, etc. The methodologies and techniques are applied to some important material processing applications, including grinding, polishing, machining, and welding. Practical automation solutions, which are complicated by part distortions, tool wear, process dynamics, and variants, are explained. The research efforts featured in the book are driven by industrial needs. They combine theoretical research with practical automation considerations. The techniques developed have been either implemented in the factory or prototyped in the laboratory. Contents: Overview of Material Processing Automation; Process Development and Approach for 3D Profile Grinding/Polishing; Adaptive Robotic System for 3D Profile Grinding/Polishing; Acoustic Emission Sensing and Signal Processing for Machining Monitoring and Control; Techniques of Automatic Weld Seam Tracking; Weld Pool Geometry Sensing and Control in Arc Welding; Automatic GTAW System Control and Teleoperation; Laser Material Processing and Its Quality Monitoring and Control. Readership: Graduate students,
academics and researchers in robotics & automated systems as well as electrical & electronic, mechanical and materials engineering.
Notlar:
Electronic reproduction. Ann Arbor, Michigan : ProQuest Ebook Central, 2017. Available via World Wide Web. Access may be limited to ProQuest Ebook Central affiliated libraries.
Tür:
Elektronik Erişim:
Click to View