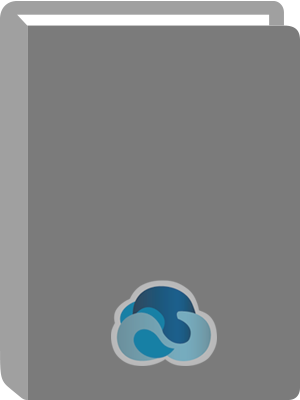
Process Plant Equipment : Operation, Control, and Reliability.
Başlık:
Process Plant Equipment : Operation, Control, and Reliability.
Yazar:
Holloway, Michael D.
ISBN:
9781118162521
Yazar Ek Girişi:
Basım Bilgisi:
1st ed.
Fiziksel Tanımlama:
1 online resource (725 pages)
İçerik:
Process Plant Equipment -- CONTENTS -- Contributors -- Preface -- SECTION I PROCESS EQUIPMENT OPERATION -- 1 Introduction -- 2 Valves -- 2.1 Types of Control Valves -- 2.1.1 Linear-Motion Control Valves -- 2.1.2 Rotary-Motion Control Valves -- 2.1.3 Nonreturn Valves -- 2.1.4 Relief Valves -- 2.2 Control Valve Actuators -- 2.2.1 Pneumatic Valve Actuators -- 2.2.2 Electric Valve Actuators -- 2.2.3 Hydraulic Valve Actuators -- 2.3 Control Valve Sizing and Selection -- 2.3.1 Selecting a Valve Type -- 2.3.2 Sizing and Selection: Letting the Computer Do It All -- 2.4 Common Problems of Control Valves -- 2.4.1 Control Valve Cavitation -- 2.4.2 Control Valve Leakage -- 2.4.3 Control Valve Nonlinearities -- 2.5 Diagnosing Control Valve Problems -- 2.6 Control Valve Reliability and Selection -- 2.7 Control Valve Maintenance -- 2.7.1 Detecting Control Valve Stiction -- 2.8 Control Valve Troubleshooting -- References -- 3 Pumps -- 3.1 Types of Pumps -- 3.1.1 Positive-Displacement Pumps -- 3.1.2 Dynamic Pumps -- 3.2 Pump Applications -- 3.2.1 Flooded Suction Applications -- 3.2.2 Suction Lift Applications -- 3.2.3 Staged Pumping -- 3.2.4 Solids-Handling Applications -- 3.3 Pump Sizing and Selection -- 3.3.1 System Head Curve -- 3.3.2 Pump Performance Curves -- 3.3.3 Actual Pump Sizing and Selection -- 3.3.4 Net Positive Suction Head -- 3.3.5 Net Positive Suction Head Available -- 3.4 Pump Maintenance -- 3.4.1 Bearing Lubrication -- 3.4.2 Seal Maintenance -- 3.4.3 Maintaining Performance -- 3.4.4 Winterizing and Long-Term Storage -- 3.4.5 Cold Temperature Installations -- 3.5 Pump Troubleshooting -- 4 Pipes -- 4.1 Types of Pipes -- 4.1.1 Seamless Pipe -- 4.1.2 Welded Pipe -- 4.2 Pipe Selection -- 4.2.1 Pipe Strength -- 4.2.2 Pipe Toughness -- 4.2.3 Pipe Weldability -- 4.2.4 Piping Material -- 4.3 Pipeline Network Design and Optimization -- 4.4 Pipeline Failure.
4.4.1 Pipe External Corrosion -- 4.4.2 Pipe Internal Corrosion -- 4.4.3 Stress Corrosion Cracking -- 4.5 Pipeline Inspection and Leak Detection -- 4.5.1 Pipeline Inspection -- 4.5.2 Pipeline Inspection Tools -- 4.5.3 Pipeline Leak Detection -- 4.6 Pipe Maintenance -- 4.6.1 Pipeline Coatings -- 4.6.2 Pipeline Repair -- 4.7 Pipe Troubleshooting -- References -- 5 Cooling Towers -- 5.1 Cooling Tower Operation -- 5.1.1 Cooling Tower Psychrometrics -- 5.1.2 Principles of Cooling -- 5.1.3 Heat Exchange -- 5.1.4 Components of Cooling Towers -- 5.2 Types of Cooling Towers -- 5.2.1 Natural-Draft Cooling Towers -- 5.2.2 Mechanical-Draft Cooling Towers -- 5.3 Common Problems of Cooling Towers -- 5.3.1 Scale Deposits -- 5.3.2 Delignification of Wood -- 5.3.3 Poor Pump Performance -- 5.3.4 Poor Airflow -- 5.3.5 Makeup Water -- 5.3.6 Clogging of Distribution Nozzles -- 5.4 Measuring Cooling Tower Performance -- 5.4.1 Performance Assessment -- 5.5 Cooling Tower Maintenance -- References -- 6 Filters and Membranes -- 6.1 Types of Filters -- 6.1.1 Gas Filters -- 6.1.2 Liquid Filters -- 6.2 Mechanisms of Filtration -- 6.2.1 Depth Straining -- 6.2.2 Surface Straining -- 6.2.3 Depth Filtration -- 6.2.4 Cake Filtration -- 6.3 Filter Selection -- 6.3.1 Chemical Compatibility -- 6.3.2 Accurate Pore Size -- 6.4 Particle-Size Measurement Techniques -- 6.4.1 Image Analysis -- 6.4.2 Direct Mechanical Measurement -- 6.4.3 Ultrasonics -- 6.4.4 Laser Scattering Technology -- 6.5 Filter Location -- 6.5.1 Pressure Line Filters -- 6.5.2 Suction Line Filters -- 6.5.3 Return Line Filters -- 6.6 Membrane Filtration -- 6.6.1 Ultrafiltration -- 6.6.2 Microfiltration -- 6.6.3 Reverse Osmosis -- 6.6.4 Nanofiltration -- 6.7 Filter Maintenance -- 6.7.1 Preparation for Maintenance -- References -- 7 Sealing Devices -- 7.1 Gaskets -- 7.1.1 Gasket Materials -- 7.1.2 Gasket and Seal Construction.
7.1.3 Principles of Gasket Operation -- 7.1.4 Gasket and Metal Seal Applications -- 7.1.5 Gasket Selection -- 7.2 Compression Packings -- 7.2.1 Packing Materials -- 7.2.2 Packing Construction -- 7.2.3 Packing Selection -- 7.2.4 Packing Installation -- 7.3 Mechanical Seals -- 7.3.1 Considerations for Using Mechanical Seals -- 7.3.2 Types of Mechanical Seals -- 7.3.3 Mechanical Seal Applications -- 7.3.4 Environmental Controls -- 7.3.5 Failure Analysis -- 7.3.6 Troubleshooting Mechanical Seals -- 7.4 Expansion Joints -- 7.4.1 Joint Construction -- 7.4.2 Principles of Joint Operation -- 7.4.3 Joint Selection -- 7.4.4 Industrial Use of Expansion Joints -- 7.4.5 Joint Installation -- 7.4.6 Joint Troubleshooting -- 7.5 General Sealing Device Selection -- 7.5.1 Product Selection -- 7.5.2 Understanding the Forces -- 7.5.3 STAMPS Criteria -- References -- 8 Steam Traps -- 8.1 Steam Trap Operation -- 8.2 Types of Steam Traps -- 8.2.1 Thermodynamic Steam Traps -- 8.2.2 Mechanical Steam Traps -- 8.2.3 Thermostatic Steam Traps -- 8.3 Steam Trap Installation -- 8.3.1 Outlets of Steam-Using Equipment -- 8.3.2 On Steam Lines -- 8.4 Steam Trap Checking -- 8.4.1 Sight Method -- 8.4.2 Sound Method -- 8.4.3 Temperature Method -- 8.4.4 Fluid Conductivity Method -- 8.5 Common Problems of Steam Traps -- 8.5.1 Air Binding -- 8.5.2 Dirt -- 8.5.3 Improper Sizing -- 8.5.4 Steam Trap Leakage -- 8.5.5 Steam Locking -- 8.5.6 Water Hammer -- 8.5.7 Erosion of Seat and Valve Sealing Faces -- 8.5.8 Life Expectancy -- 8.6 Steam Trap Selection -- 8.7 Steam Trap Applications -- 8.7.1 Protection Service -- 8.7.2 Process Service -- 8.7.3 Other Applications -- 8.8 Steam Trap Sizing -- 8.8.1 Basic Considerations -- 8.9 Steam Trap Maintenance -- References -- 9 Process Compressors -- 9.1 Types of Compressors -- 9.2 Continuous Compression Compressors -- 9.2.1 Ejectors.
9.2.2 Dynamic, Rotodynamic, or Turbocompressors -- 9.3 Intermittent Compression Compressors -- 9.3.1 Positive-Displacement Compressors (Intermittent Flow) -- 9.3.2 Rotary Compressors (Continuous Flow) -- 9.4 Centrifugal Compressors -- 9.4.1 Major Components of Centrifugal Compressors -- 9.4.2 Thermodynamics of Centrifugal Compressors -- 9.4.3 Energy Transfer in Centrifugal Compressors -- 9.4.4 Slip in Centrifugal Impellers -- 9.4.5 Losses and Efficiencies -- 9.4.6 Performance, Stall, and Surge -- 9.4.7 Drivers -- 9.5 Reciprocating Piston Compressors -- 9.5.1 Compressor Operation -- 9.5.2 Thermodynamic Laws -- 9.5.3 Compression Cycles -- 9.5.4 Power Requirements -- 9.5.5 Multistage Compression -- 9.5.6 Cylinder Clearance and Volumetric Efficiency -- 9.5.7 Valve Losses -- 9.5.8 Major Components of Reciprocating Piston Compressors -- 9.5.9 Drivers -- 9.6 Compressor Troubleshooting -- References -- Further Reading -- 10 Conveyors -- 10.1 Industrial Use of Conveyors -- 10.2 Types of Conveyors -- 10.2.1 Belt Conveyors -- 10.2.2 Bucket Conveyors -- 10.2.3 Cart-on-Track Conveyors -- 10.2.4 Chute Conveyors -- 10.2.5 Gravity Wheel Conveyors -- 10.2.6 Monorails -- 10.2.7 Chain Conveyors -- 10.2.8 Pneumatic Conveyors -- 10.2.9 Roller Conveyors -- 10.2.10 Screw Conveyors -- 10.2.11 Slat Conveyors -- 10.2.12 Sortation Conveyors -- 10.2.13 Vane-Type Throwing Machines -- 10.2.14 Tow Conveyors -- 10.2.15 Trolley Conveyors -- 10.2.16 Vertical Conveyors -- 10.2.17 Vibrating Conveyors -- 10.2.18 Troughed Belt Conveyors -- 10.2.19 Magnetic Belt Conveyors -- 10.2.20 Power-and-Free Conveyors -- 10.3 Conveyor Selection -- 10.4 Conveyor Safety -- 10.5 Conveyor Maintenance -- 10.6 Summary -- References -- 11 Storage Tanks -- 11.1 Types of Storage Tanks -- 11.1.1 Aboveground Tanks -- 11.1.2 Underground Tanks -- 11.2 Storage Tank Classification -- 11.2.1 Aboveground Tanks.
11.2.2 Underground Tanks -- 11.3 Construction Materials -- 11.3.1 Tank Materials -- 11.3.2 Protective Coatings -- 11.3.3 Insulation -- 11.4 Common Problems of Storage Tanks -- 11.4.1 Corrosion -- 11.4.2 Vapor Losses -- 11.4.3 Storage Tank Fires -- 11.5 Storage Tank Maintenance -- 11.5.1 Tank Blanketing -- 11.5.2 Holiday Detection -- 11.5.3 Tank Cleaning -- 11.6 Tank Appurtenances -- 11.6.1 Mixers -- 11.6.2 Dikes -- 11.6.3 Insulators -- 11.6.4 Platforms and Ladders -- 11.6.5 Gauging Devices -- 11.6.6 Valves -- 11.6.7 Manways -- 11.6.8 Diffusers -- 11.6.9 Water Cannons -- 11.6.10 Vents -- 11.6.11 Grounding -- 11.6.12 Supporting Structures -- 11.7 Storage Tank Maintenance -- References -- 12 Mixers -- 12.1 Mixing Concepts: Theory and Practice -- 12.1.1 Batch and Continuous Mixing -- 12.1.2 Selection of Mixing Equipment -- 12.1.3 Design of Mixing Equipment -- 12.1.4 Scale-Up of Mixing Equipment -- 12.2 Fluid Mixing -- 12.2.1 Fluid Mixing Applications -- 12.2.2 Mixing Regimes -- 12.2.3 Power Consumption in Agitated Vessels -- 12.2.4 Flow Characteristics -- 12.2.5 Liquid Agitation Equipment -- 12.3 Solid Blending -- 12.3.1 Properties of Solids Affecting Blending -- 12.3.2 Types of Blend Structures -- 12.3.3 Mechanisms of Solid Blending -- 12.3.4 Segregation Mechanisms -- 12.3.5 Scale-Up of Solid Mixers -- 12.3.6 Solid Blending Equipment -- 12.4 Mixing High-Viscosity Materials and Pastes -- 12.4.1 Dispersive, Distributive, and Convective Mixing -- 12.4.2 Power for Viscous Mixing -- 12.4.3 Scale-Up of High-Viscosity Mixers -- 12.4.4 Heat Transfer -- 12.4.5 Equipment for Mixing High-Viscosity Materials and Pastes -- 12.5 Mechanical Components in Mixing Equipment -- 12.5.1 Motors -- 12.5.2 Mixer Speed Reducers -- 12.5.3 Couplings -- 12.5.4 Bearings -- 12.5.5 Shaft Seals -- 12.5.6 Variable-Speed Operation Devices.
12.5.7 Mixer Installation, Startup, and Maintenance.
Özet:
"Process Plant Equipment Book is another great publication from Wiley as a reference book for final year students as well as those who will work or are working in chemical production plants and refinery…" -Associate Prof. Dr. Ramli Mat, Deputy Dean (Academic), Faculty of Chemical Engineering, Universiti Teknologi Malaysia "…give[s] readers access to both fundamental information on process plant equipment and to practical ideas, best practices and experiences of highly successful engineers from around the world… The book is illustrated throughout with numerous black & white photos and diagrams and also contains case studies demonstrating how actual process plants have implemented the tools and techniques discussed in the book. An extensive list of references enables readers to explore each individual topic in greater depth…" -Stainless Steel World and Valve World, November 2012 Discover how to optimize process plant equipment, from selection to operation to troubleshooting From energy to pharmaceuticals to food, the world depends on processing plants to manufacture the products that enable people to survive and flourish. With this book as their guide, readers have the information and practical guidelines needed to select, operate, maintain, control, and troubleshoot process plant equipment so that it is efficient, cost-effective, and reliable throughout its lifetime. Following the authors' careful explanations and instructions, readers will find that they are better able to reduce downtime and unscheduled shutdowns, streamline operations, and maximize the service life of processing equipment. Process Plant Equipment: Operation, Control, and Reliability is divided into three sections: Section One: Process Equipment Operations covers such key equipment as valves, pumps, cooling towers, conveyors, and storage tanks Section Two: Process
Plant Reliability sets forth a variety of tested and proven tools and methods to assess and ensure the reliability and mechanical integrity of process equipment, including failure analysis, Fitness-for-Service assessment, engineering economics for chemical processes, and process component function and performance criteria Section Three: Process Measurement, Control, and Modeling examines flow meters, process control, and process modeling and simulation Throughout the book, numerous photos and diagrams illustrate the operation and control of key process equipment. There are also case studies demonstrating how actual process plants have implemented the tools and techniques discussed in the book. At the end of each chapter, an extensive list of references enables readers to explore each individual topic in greater depth. In summary, this text offers students, process engineers, and plant managers the expertise and technical support needed to streamline and optimize the operation of process plant equipment, from its initial selection to operations to troubleshooting.
Notlar:
Electronic reproduction. Ann Arbor, Michigan : ProQuest Ebook Central, 2017. Available via World Wide Web. Access may be limited to ProQuest Ebook Central affiliated libraries.
Tür:
Elektronik Erişim:
Click to View