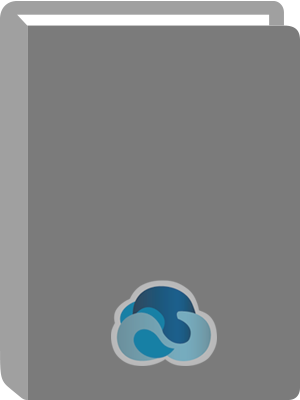
Handbook of Troubleshooting Plastics Processes : A Practical Guide.
Başlık:
Handbook of Troubleshooting Plastics Processes : A Practical Guide.
Yazar:
Wagner, John R.
ISBN:
9781118511169
Yazar Ek Girişi:
Basım Bilgisi:
1st ed.
Fiziksel Tanımlama:
1 online resource (506 pages)
İçerik:
Handbook of Troubleshooting Plastics Processes: A Practical Guide -- Contents -- Preface -- List of Contributors -- Part 1: Troubleshooting Basics -- 1 The Economics of Troubleshooting Polymer Processing Systems -- 1.1 Introduction -- 1.2 Economic Incentives and Necessities -- 1.3 Troubleshooting Resources and Their Cost -- 1.4 Managing Resources and Costs -- 1.5 Troubleshooting Techniques and Their Relative Costs -- 1.6 Case Histories -- 1.6.1 Single Screw Extrusion Instability -- 1.6.2 Compounding Extruder Catastrophic Failure -- 1.6.3 Polymer Degradation During Melt Processing -- 1.7 Conclusions -- References -- 2 Troubleshooting Philosophy -- 2.1 Introduction -- 2.2 Troubleshooting Methodology -- Bibliography -- 3 Statistical Tools for Trouble Shooting a Process -- 3.1 Introduction -- 3.2 Basic Statistical Concepts -- 3.2.1 Histogram -- 3.2.2 Scatter Diagram -- 3.3 Sample Mean and Standard Deviation -- 3.4 Design of Experiments (DOE) -- 3.4.1 Factorial Design -- 3.4.2 Fractional Factorial Design -- 3.5 Process Capability -- 3.6 Control Charts -- 3.7.1 Central Limit Theorem -- 3.7.2 Variable Data Control Charts -- 3.7.3 Control Charts for Attribute Data -- References -- Bibliography -- Statistics -- Design of Experiments -- Statistical Process Control -- Part 2: Extrusion Processes -- 4 Single Screw Extrusion -- 4.1 Introduction -- 4.2 Process Description -- References -- 5 Troubleshooting the Co-rotating Fully Intermeshing Twin-screw Compounding System -- 5.1 Introduction -- 5.2 Equipment Description -- 5.3 Troubleshooting -- 5.3.1 What is Troubleshooting? -- 5.4 Tools of the Successful Troubleshooter -- 5.4.1 Experience -- 5.4.2 Vent Flow Problem -- 5.5 Product, Process and Equipment Knowledge -- 5.5.1 High Discharge Pressure Problem -- 5.5.2 Barrel Temperatures Higher than Set Points Problem -- 5.5.3 Climbing Discharge Temperature Problem.
5.5.4 Gels and Un-melts in the Extrudate Problem -- 5.5.5 Holes or Bubbles in the Extrudate Problem -- 5.5.6 Process Surging Problem -- 5.6 Conclusion -- References -- 6 Troubleshooting for Injection Molding -- 6.1 Introduction -- 6.1.1 The Basic Approach -- 6.2 Understanding Temperature Control -- 6.3 Product Shift to a Different Machine -- 6.3.1 Calculate the New Pressure Settings -- 6.3.2 Procedure -- 6.4 Part Weight as an Analytical Tool -- 6.4.1 Example - Part Weight for Process Variability Analysis -- 6.4.2 Long Term Variability Analysis -- 6.4.3 Short Term Variability Analysis -- 6.4.4 Variability Evaluation -- 6.4.5 Process Benchmarking for Quality -- 6.4.6 Benchmark Evaluation -- 6.4.7 Summary -- 6.5 Part Weight as Dimensional Aimpoint Control -- 6.5.1 Unconstrained Process -- 6.5.2 Partially Constrained Process -- 6.5.3 Constrained Process -- 6.5.4 Warpage -- 6.5.5 Relationship of Shot Weight and Hydraulic Pressure -- 6.6 Determining the Gate Freeze-Off Time -- 6.6.1 Procedure to Determine the Freeze-Off Point -- 6.6.2 Time Analysis -- 6.6.3 Pressure Procedure -- References -- 7 Blown Film -- 7.1 Introduction -- 7.2 Process Description -- 7.2.1 Extruders -- 7.2.2 Dies -- 7.2.3 Process Cooling -- 7.2.4 The Bubble Collapsing Process and Systems -- 7.2.5 Haul-Off/Primary Nip -- 7.2.6 Film Winding -- 7.2.6.1 Center-drive Winder -- 7.2.6.2 Surface Winders -- 7.3 Special Tools for Troubleshooting -- 7.3.1 Winding Systems -- 7.4 Case Studies -- 7.4.1 Case Study 1: Carbon Buildup -- 7.4.2 Case Study 2: Poor Gauge Uniformity -- References -- 8 Cast Film Troubleshooting -- 8.1 Coextrusion Film Systems -- 8.2 Troubleshooting Method -- 8.2.1 The Problem Statement -- 8.2.2 The Hypothesis -- 8.2.3 Testing the Hypothesis -- 8.2.4 Evaluating the Results -- 8.3 Common Problems, Hypotheses and Tests -- 8.3.1 Gels in Film -- 8.3.2 Film Clarity.
8.3.3 Wrinkling -- 8.3.4 Inability to Reach Output -- 8.3.5 Poor Melt Mixing -- 8.3.6 Melt Temperature Too Low -- 8.3.7 Melt Temperature Too High -- 8.3.8 Extruder Power Insufficient -- 8.3.9 Film Streaks or Lines -- 8.3.10 Melt Appearance Defects -- 8.3.11 Thickness Variation - Cross Direction -- 8.3.12 Thickness Variation - Machine Direction -- 8.3.13 Poor Wound Roll Appearance -- 8.3.14 Edge Tear (Unstable Edges) -- 8.3.15 Pin Holes -- 8.3.16 Extruder Surging -- 8.3.17 Draw Resonance -- 8.3.18 Film Discoloration -- 8.3.19 Poor Heat Seal Strength -- 8.3.20 Odor - Flavor Scalping -- 8.3.21 Poor Strength -- 8.3.22 Film Blocking -- 8.3.23 Poor Printability -- 8.3.24 Camber or Curl -- 8.3.25 Scratches -- References -- 9 Oriented Films-Troubleshooting and Characterization -- 9.1 Introduction -- 9.2 Process Overview: Biaxial Orientation -- 9.3 Oriented Film Markets -- 9.3.1 Oriented Polypropylene OPP or BOPP -- 9.3.2 Oriented Polyester OPET -- 9.3.3 Oriented Polystyrene OPS -- 9.3.4 Oriented Polyamide (Nylon) OPA -- 9.4 Troubleshooting the Film Orientation Process as Applied to OPP Films -- 9.4.1 Control Variables -- 9.4.1.1 Resin Drying -- 9.4.1.2 Extrusion -- 9.4.1.3 Casting and Pinning -- 9.4.1.4 Machine Direction Orientation -- 9.4.1.5 Transverse Direction Orientation -- 9.4.1.6 Web Handling and Surface Treatment -- 9.4.1.7 Winding -- 9.4.2 Noise Variables -- 9.4.3 Dependent Variables -- 9.5 Special Tools for Troubleshooting -- 9.6 Case Studies -- 9.6.1 Casting Capacity Limitation in PET Film Production -- 9.6.2 Floating Gauge - Extrusion Instability and MDO Heat Transfer Limitations -- 9.6.3 Output Limitation from Coextrusionlnstability -- References -- Bibliography -- 10 Troubleshooting the Thermoforming Process -- 10.1 General Concepts in Thermoforming -- 10.2 Categorization of the Process -- 10.2.1 Thick-Gauge Process -- 10.2.2 Thin-Gauge Process.
10.3 Specific Aspects of the Thermoforming Process -- 10.3.1 Critical Material Issues -- 10.3.2 Molds and Mold Design -- 10.3.3 Incoming Sheet Quality Issues -- 10.3.4 Materials Handling - Ingress -- 10.3.5 Heating -- 10.3.6 Pre-stretching (Plug Assist) -- 10.3.7 Pre-stretching (Vacuum/Air Pressure Formation) -- 10.3.8 Contacting the Mold -- 10.3.9 Cooling and Rigidifying the Formed Part -- 10.3.10 Removing the Formed Part from the Mold -- 10.3.11 Materials Handling - Egress -- 10.3.12 Trimming -- 10.3.13 Post-trimming Issues -- 10.3.14 Regrind -- 10.4 Problem Solving Methodology -- 10.4.1 Trimming -- 10.5 General Preventative Maintenance Concepts -- 10.5.1 Crisis Maintenance -- 10.5.2 Routine Maintenance -- 10.6 General Predictive Maintenance Concepts -- 10.7 Safety during Troubleshooting -- 10.7.1 Make-up of a Troubleshooting Team -- Appendix 1: Thermoforming References with Troubleshooting Sections -- Appendix 2: Plastic Materials References -- Appendix 3: Troubleshooting Guidelines for Thick-Gauge Thermoforming -- Appendix 4: Troubleshooting Guidelines for Thin-Gauge Thermoforming -- Appendix 5: Time-dependent Ranking of Typical Courses of Action -- Appendix 6: Troubleshooting Guidelines for Trimming Parts -- Thin-Gauge -- Thick-Gauge -- 11 Proper Equipment Processing for Industrial/Technical Blow Molding -- 11.1 Introduction of Blow Molding -- 11.1.1 How Parts are Blow Molded -- 11.1.2 Positive Benefits of the Process -- 11.1.3 Negative Factors of Accumulator Head Blow Molding -- 11.2 Select the Proper Equipment -- 11.3 Extruder -- 11.4 Accumulator Head -- 11.5 Importance of Cleaning -- 11.6 Press -- 11.7 Hydraulics -- 11.8 Microprocessor -- 11.9 Pneumatic Systems -- 11.10 Part Take Out System -- 11.11 Selection of Equipment -- 12 PET Stretch Blow Molding -- 12.1 Introduction -- 12.2 The PET Universe -- 12.3 Technology History.
12.4 PET Chemistry -- 12.5 PET Morphology -- 12.6 Bottle Universe -- 12.7 Bottle Manufacturing -- 12.8 Commercial Manufacturing Processes -- 12.9 Process Elements -- 12.9.1 Injection Molding -- 12.9.1.1 IV Drop -- 12.9.1.2 Acetaldehyde -- 12.9.1.3 Molding Stresses -- 12.9.2 Hot Runner System -- 12.9.2.1 Gate Crystallinity and Separation -- 12.9.2.2 Gate Pin Holes -- 12.9.3 Mold Cooling -- 12.9.3.1 Preform Problem Analysis -- 12.9.4 Blow Molding -- 12.9.4.1 General Principles - Reheating and Preform Temperature -- 12.9.5 Preform Temperature Profiling -- 12.9.6 Blowing -- 12.9.6.1 Quality Attributes and Performance Issues -- 12.9.6.2 Blow Molding Process Monitoring -- 12.9.6.3 On Line Inspection -- 12.9.6.4 Testing and Test Procedures -- 12.9.6.5 Special Processes -- 12.10 Case Sample: Thermal Stability Failure of CSD Bottles -- References -- 13 Blow Molding - Problems and Solutions -- 13.1 Introduction -- 13.2 Troubleshooting -- 13.3 Variables Affecting the Blow Molding Process -- 13.3.1 PART I: Defects in Article -- 13.3.1.1 PART I - Defect in Finished Article -- 13.3.2 PART II: Parison Defects -- 13.3.2.1 PART II - Defects of the Parison -- 13.3.3 Noise -- 13.3.4 Ambient Conditions -- 13.4 Preventative Maintenance -- 13.4.1 Maintenance Recommendations -- 13.4.2 Machine Check Out -- 13.5 Injection and Stretch Blow Molding -- 13.6 Computer Integrated Manufacturing (CIM) in Extrusion Blow Molding -- Acknowledgement -- Bibliography -- 14 Extrusion Coating Troubleshooting -- 14.1 Coextrusion Extrusion Coating/Laminating Systems -- 14.2 Troubleshooting Method -- 14.3 Common Problems, Hypotheses and Tests -- 14.3.1 Gels in Film -- 14.3.2 Poor Adhesion -- 14.3.3 Wrinkling -- 14.3.4 Low Output -- 14.3.5 Poor Melt Mixing -- 14.3.6 Melt Temperature Too Low -- 14.3.7 Melt Temperature Too High -- 14.3.8 Extruder Power Insufficient -- 14.3.9 Die Lines.
14.3.10 Melt Appearance Defects.
Özet:
This handbook provides a framework for understanding how to characterize plastic manufacturing processes for use in troubleshooting problems. The 21 chapters are authored by well-known and experienced engineers who have specialized knowledge about the processes covered in this practical guide. From the Preface: "In every chapter, the process is described and the most common problems are discussed along with the root causes and potential technical solutions. Numerous case studies are provided that illustrate the troubleshooting process. Mark A. Spalding, The Dow Chemical Company.
Notlar:
Electronic reproduction. Ann Arbor, Michigan : ProQuest Ebook Central, 2017. Available via World Wide Web. Access may be limited to ProQuest Ebook Central affiliated libraries.
Tür:
Yazar Ek Girişi:
Elektronik Erişim:
Click to View